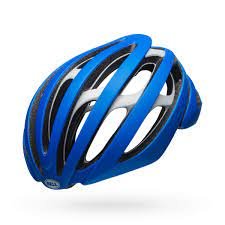
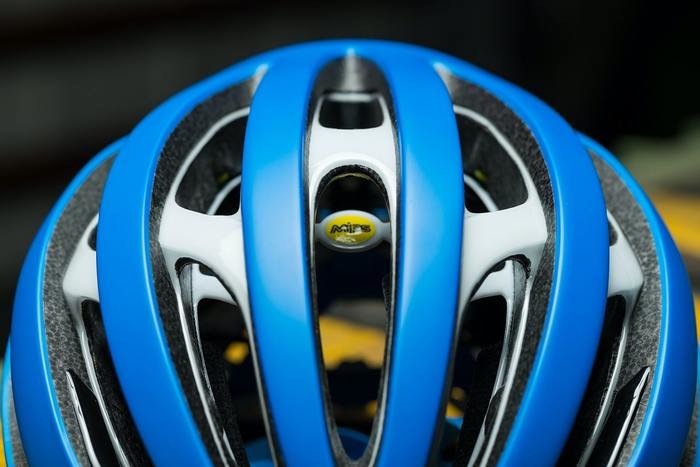
The Bell Zephyr close up front view.
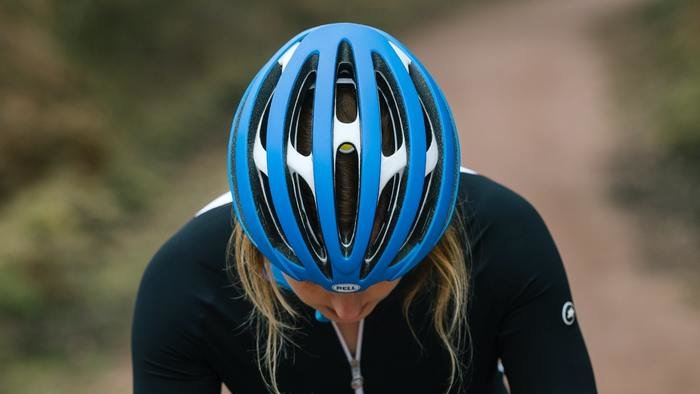
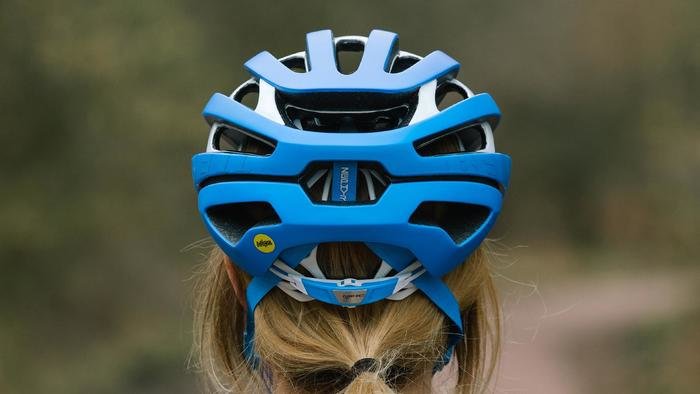
From the rear you see the open nature of the helmet, air able to pass through the body, distinguishing it as a high end road helmet. Attention to detail from the whole team is also visible in this view; fit system, logo strapping etc.
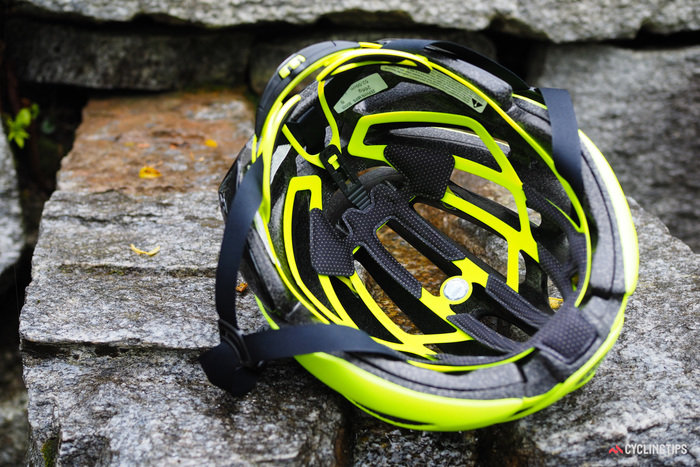
Integrated MIPS means the low friction layer which promotes rotation of the helmet during impact is fitted directly into the fit system gear system. Here also you can see a well thought out padding method and the sweat management; simply adding a tongue of foam onto the brow...seriously, the sweat drips down in from of your sun glasses, not onto the lenses...it really works.
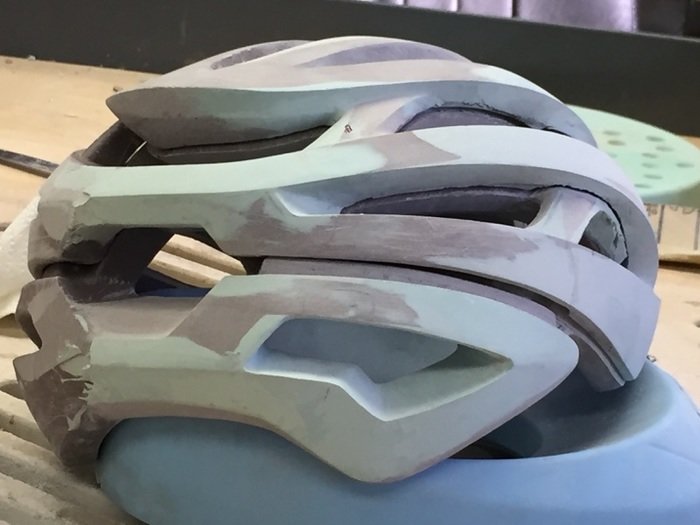
This shot taken in the shop in Scotts Valley CA is on the table of Hilgard Muller. He worked his ID magic over my initial 3D print. From this we white light scanned it and reworked the CAD prior to tooling release.
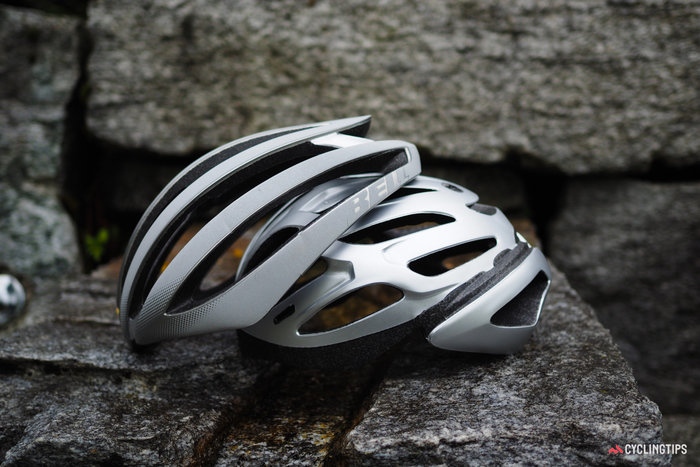
Here is a shot of the dual body construction.
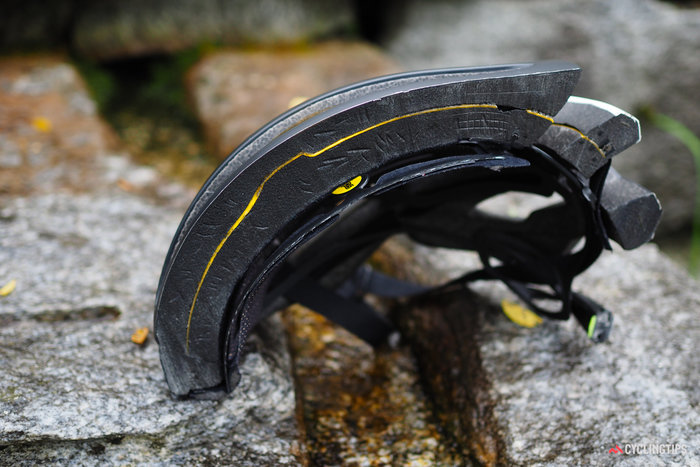
Cut in half you can see the separation between the higher density upper body and the lower density lower body.
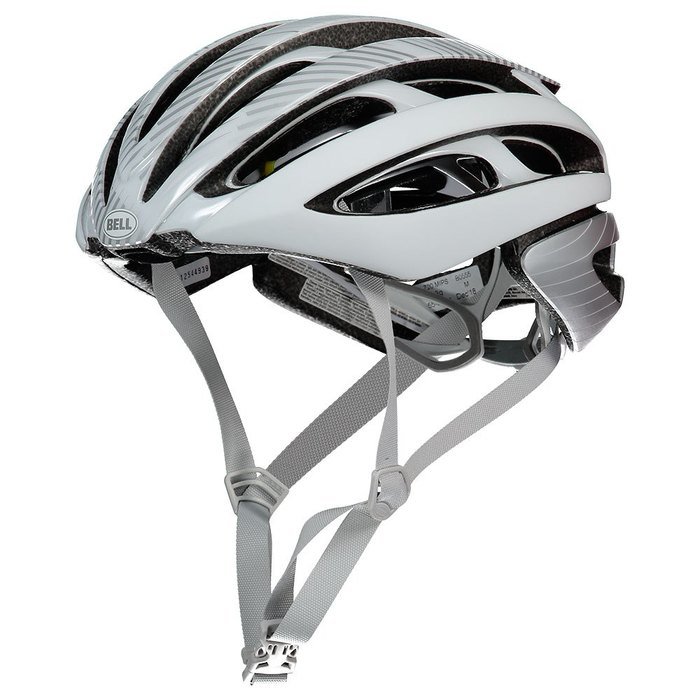
gLike