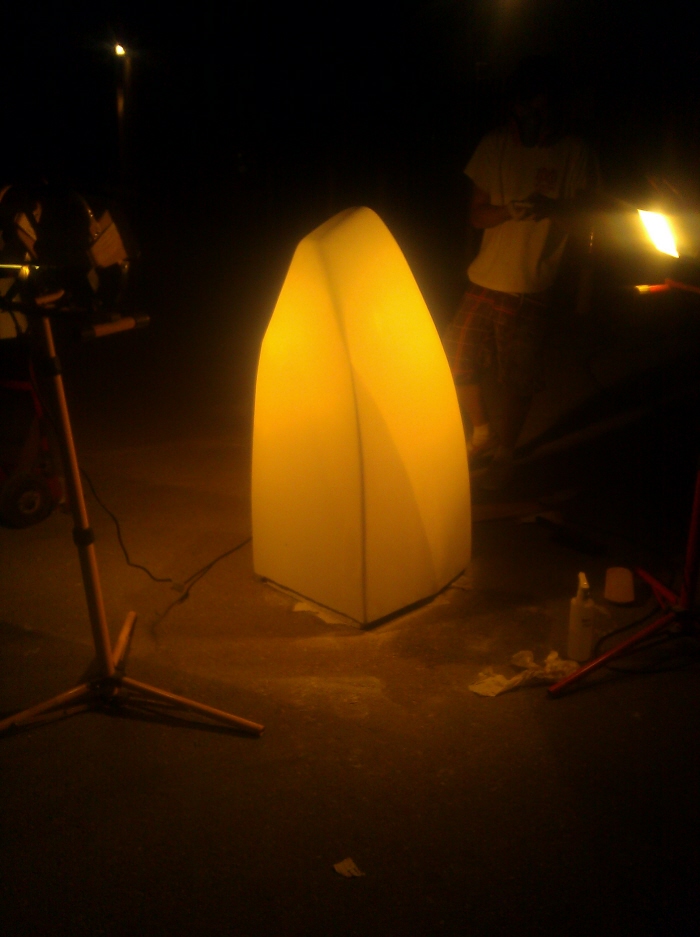
High build primer was used once the mold was the desired shape. The primer was wet-sanded to a smooth finish since the surface is transferred over to the mold. Mold release was sprayed on before the application of fiberglass mat and epoxy resin.
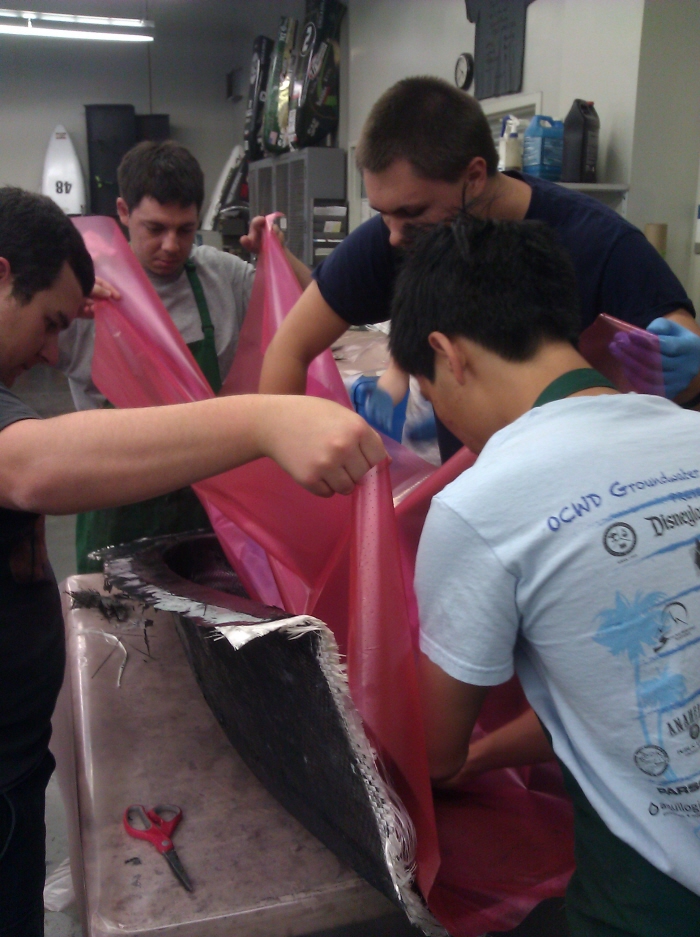
Mold preparation for the wet-layup consisted of polishing the mold, positioning the carbon weave, adding breather cloth and release film, then bagging the entire mold.
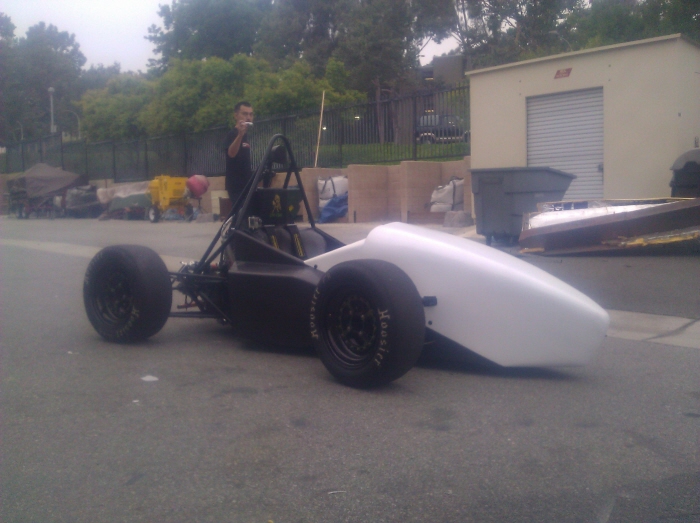
The trimmed, painted, and installed bodywork on the 2012 FSAE car.
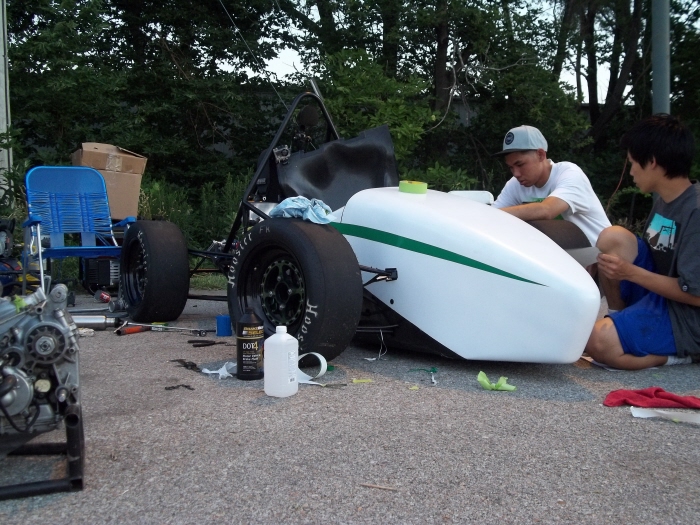
Vinyl is applied, which includes accents and sponsor logos.
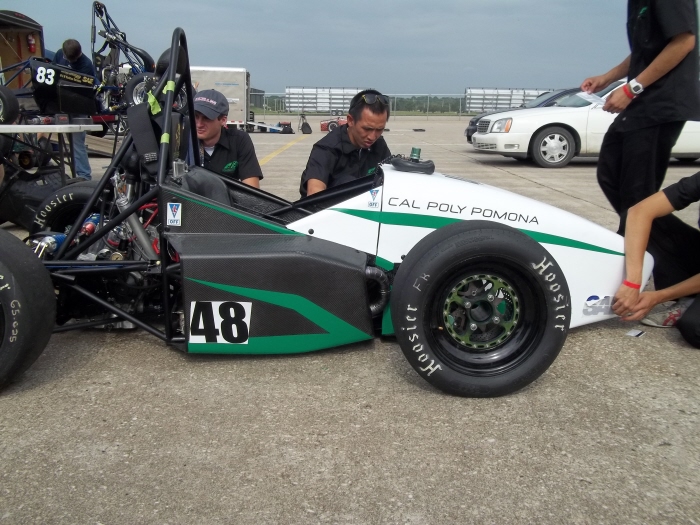
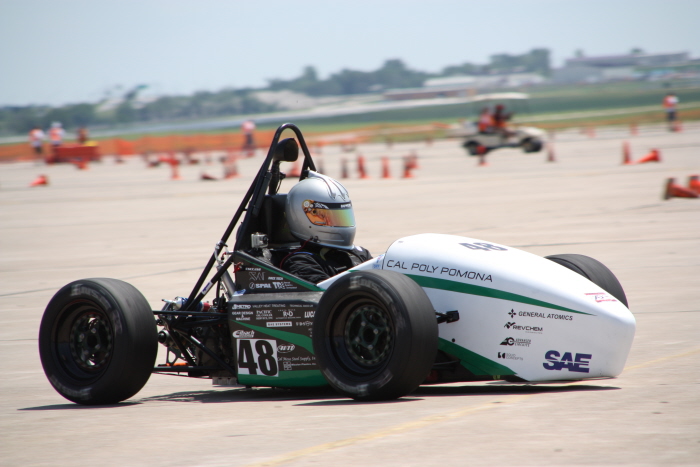
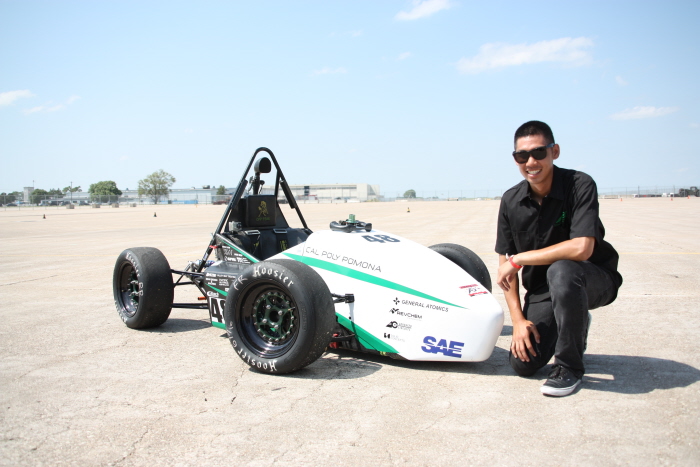
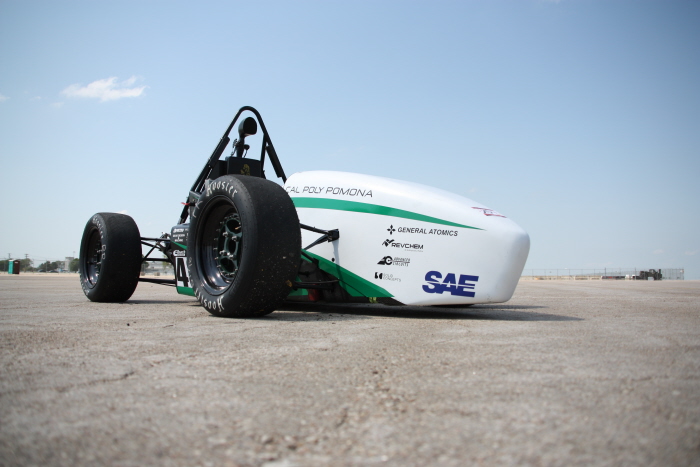
7th place overall finish, Lincoln Nebraska.
gLike