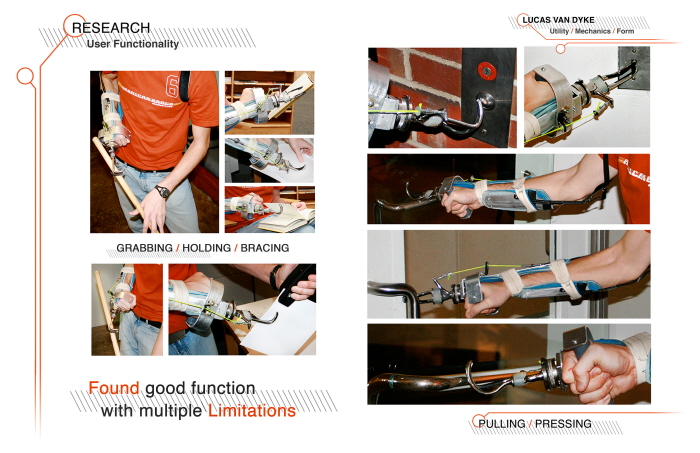
Nate and I used a prosthetic hook that could be worn on our arm and found there were positive and negative functions about the current design. The multiple limitations included: very difficult to push on anything cylindrical or round like a shopping cart or door handles. Also, due to the rounded nature of the hook, holding down a piece of paper was hard, for example the hook only acted as a point for the receipt to pivot around while trying to sign it. It was also very difficult to squeeze anything with a particular strength, To hold an egg lightly, the user would apply negative force against the rubber band but not too much force or it would release. And there is no ability to grip beyond the grip provided by the rubber bands. The more rubber bands on the hook meant the more force the user had to pull against every time they wanted to use it but the more gripping power the user would have, and visa versa.

Nate and I engineered linkage that allows the Prosthesis to act in both a Voluntary open and Voluntary close with one single pull of the shoulder. This provided the best of both worlds for the user, able to "feel" the grip they were delivering and also feel the resistance on the cable. The rounded nob in the thumb provided a smooth transition and constant pull pressure throughout the draw of the slider. The User would no longer need to struggle against unnecessary rubber bands, but would be able to squeeze with strength upon demand. The hook would return to its starting closed position with a small internal torsion spring.
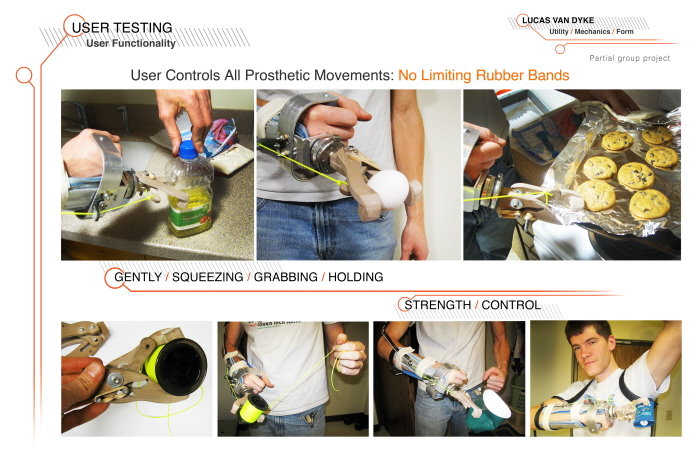
Nate is pictured here demonstrating the results of the new linkage. While baking cookies, he was able to have exact grip strength while holding a bottle still, carrying an egg without cracking or dropping it, Crushing a cup, and holding rounded objects without them being scissor pinched out of the "hand"
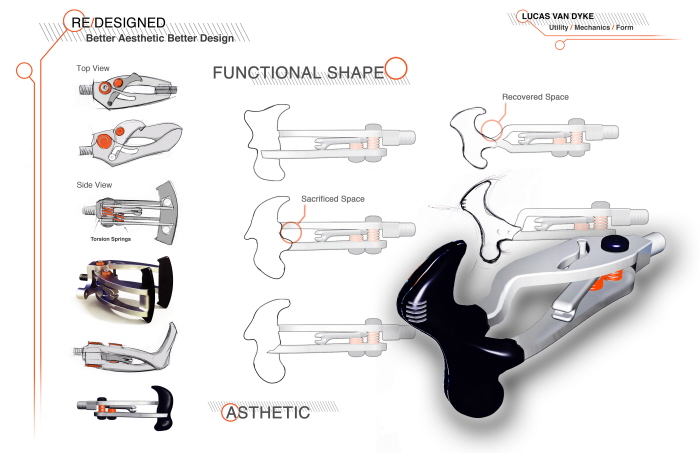
I then took the project a step further by redesigning the fingers of the prosthetic. The redesign of the fingers would allow greater functionality, and a reduction in both wasted space taken up by the mechanics, as well as in the amount of rotations of the mechanical wrist to accomplish tasks. The new finger shape deliver a variety of new functions. It will center itself when pressed against shopping cart handles and door nobs. It has two points of contact as to secure something from swiveling while pinned. It also can "hook" something using the bottom of the top of the fingers.
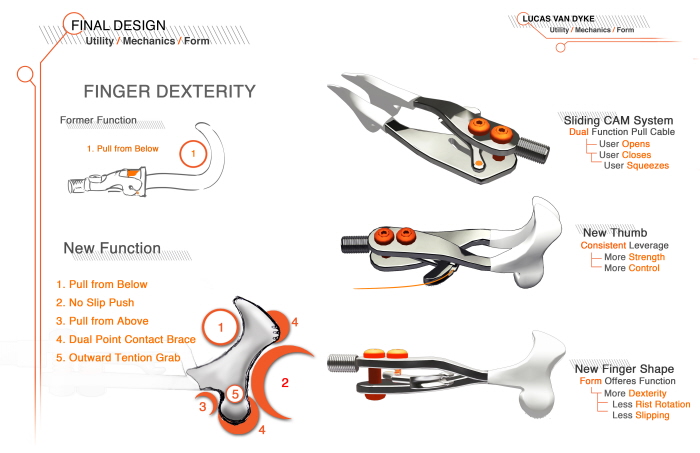
The new prosthetic is able to be inserted between things to apply an outward force. The Fingers are curved from top to bottom in a convex shape similar to this -> )) which helps it not catch on the users leg while walking. The convex curved shape also helps grip cylindrical objects like bottles or cans. The finger tips are thinner but deeper like paddles to increase effective gripping surface area and not have the prosthetic look like a sharp hook and have a rubberized covering which both help in not having it feel as cold to the touch. These improvements help so much including gentle tasks such as buttoning your child's pants or holding their hand while crossing the street.
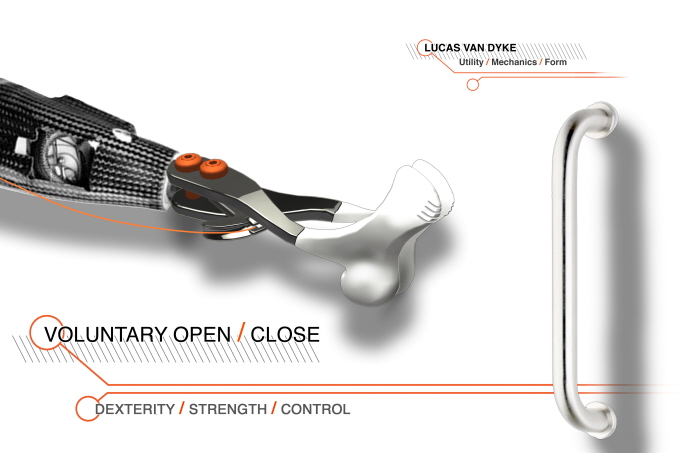
With the refreshed design and new technology in this prosthetic, there is improved dexterity, increased strength, and more precise control. While the design for something of this nature is never complete, this design is an improvement from the basic mechanical hook while still using the most appropriate technology without relying on electrical or computerized components.
Jonathan Kuniholm reviewed our designs and gave positive feedback for the improvements.
Here is a link to Jon Kuniholm talking at UNC for a TEDx Talk: http://www.youtube.com/watch?v=7AWRSVuN2ik
And here is a link to Open Prosthetics.org which is a project started by Jon Kuniholm in the attempt to open source design developments in the realm of prosthetic: http://www.openprosthetics.org/
gLike