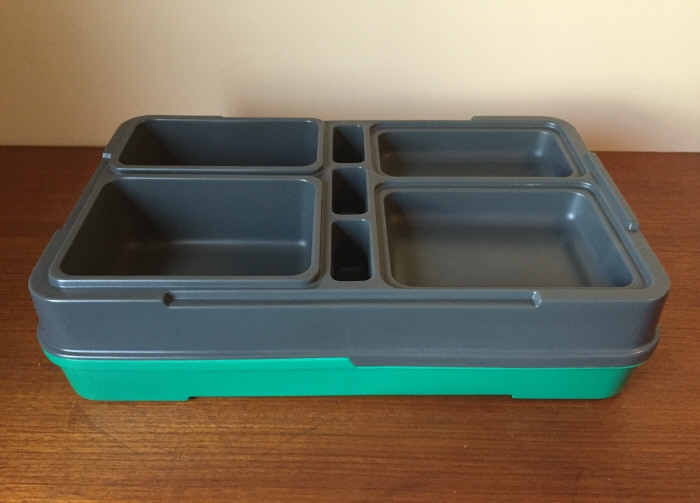
Form-fit prototype. Has original, deeper cavities and condiment wells. Prototype is also taller than final.

Prototype: gray and green parts are identical. Showing un-welded halves that together make one tray. Note their undersides where cavities and ribs abut each other thus doubling the material thickness of cavity floors, resulting in much greater strength than previous OTS designs with EPS injected into cavities between tray halves to reduce cavity floor collapse.
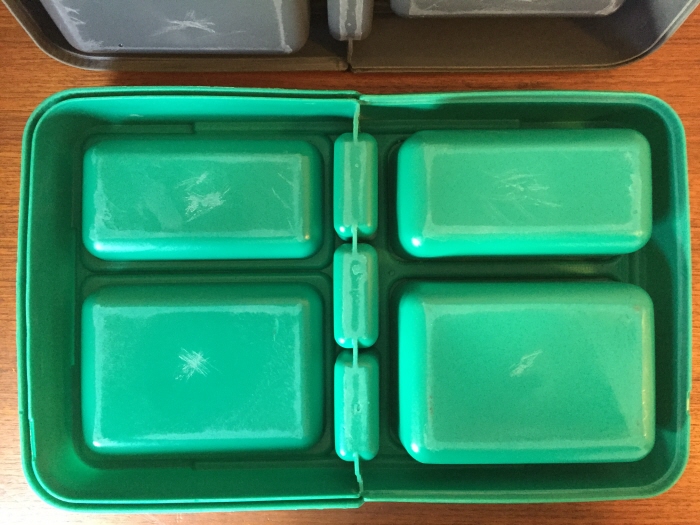
Prototype: gray and green parts are identical. Showing un-welded halves that together make one tray.
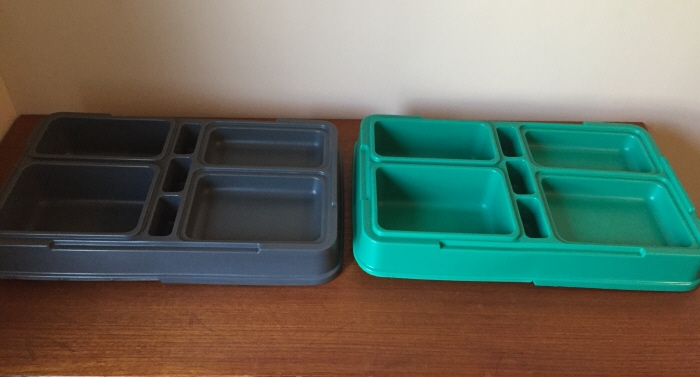
Prototype: showing identical halves in two colours. Note their individual asymmetry and lack of flat balance. Together, these make one tray.
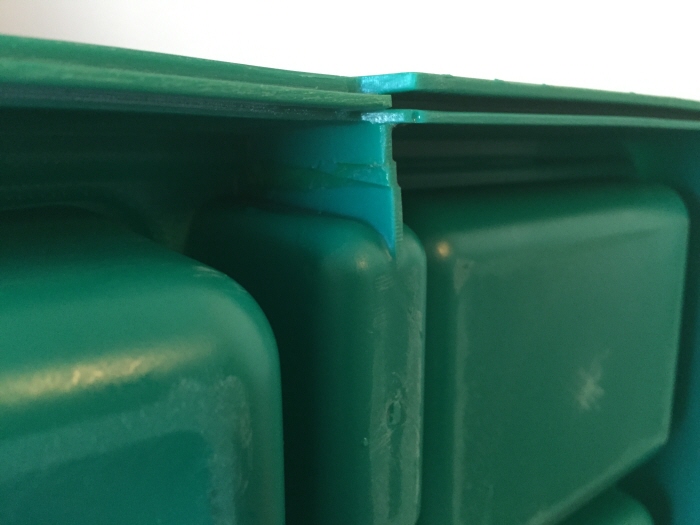
Prototype: showing the part's male and female perimeter weld channels
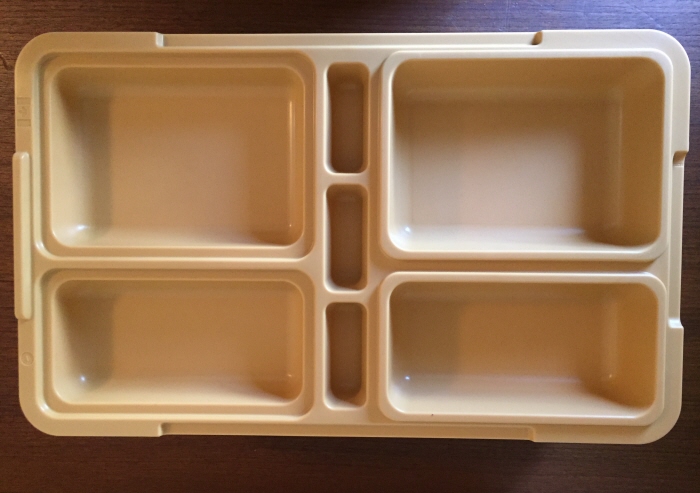
Final product: top view. Shallow food cavities on left.
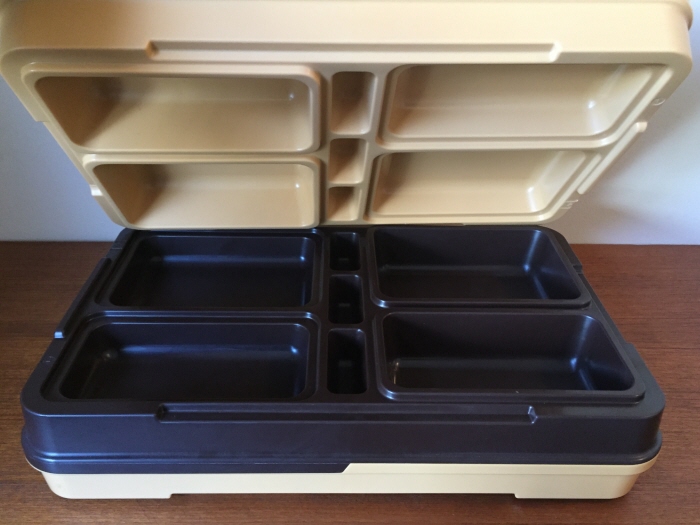
Final product: showing how one tray nests into another.
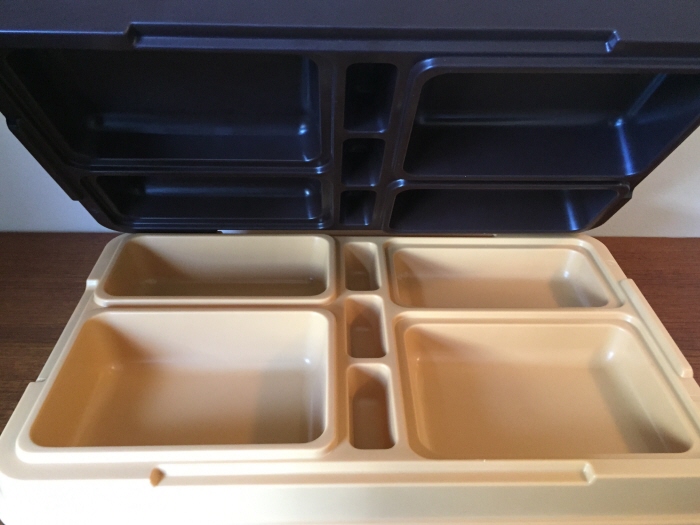
Final product: showing how trays nests into one another.

Final product: side view of two stacked units. To reiterate, the cream and brown halves are identical. This product design consists of one part*, made twice, then fused together to create one final tray.
* Each part is asymmetrical, with male and female cavity ridges, male and female perimeter weld channels, and stabilizing feet.
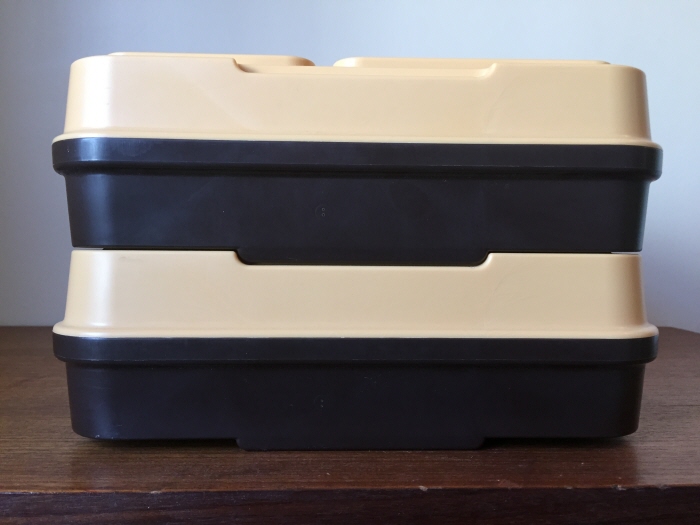
Final product: right view of two stacked units.
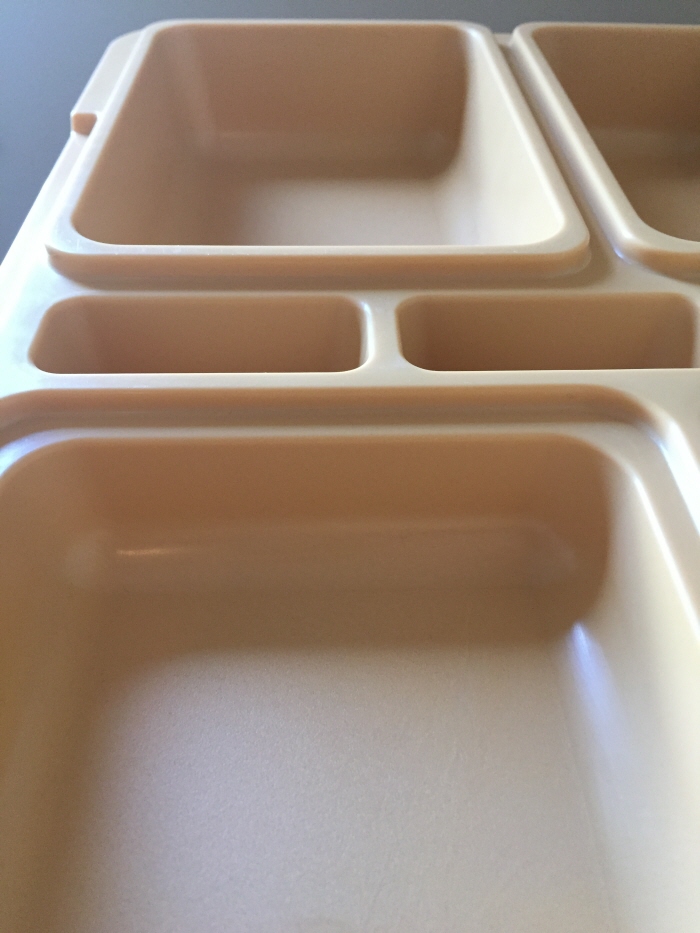
Final product: detail showing food and condiment cavities, as well as side prehension detail.
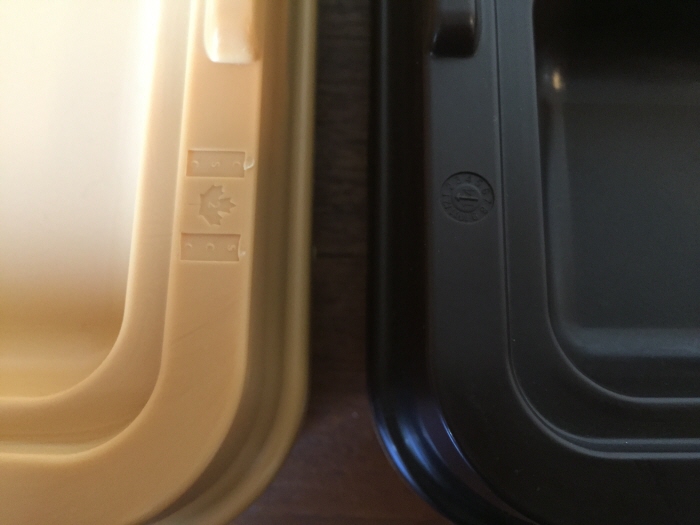
Final product: showing "CSC2" logo, and injection moulding date stamp.
gLike