
This is a fully assembled airfoil section. The one major component that hasn't been discussed yet is the wooden band attached to the exterior of the right most rib. This 'sacrificial edge' is used as a fail-safe. The gap between the different sections was determined by applying a conservative load on the spar. The maximum deflection angle was determined with an FEA package. This angle was used to calculate the gap to prevent the sections from contacting one another during testing. However, this analysis was done with static conditions while the actual displacements experienced by the airfoil will be dynamic. Intuitively, this is not a safe assumption especially knowing the complex motion flutter can exhibit. To prevent the need to make another airfoil do to collisions during testing, wood can be removed from this 'sacrificial edge' to increase the gap. Intuition on the problem will prevent us from creating huge problems to fix later.
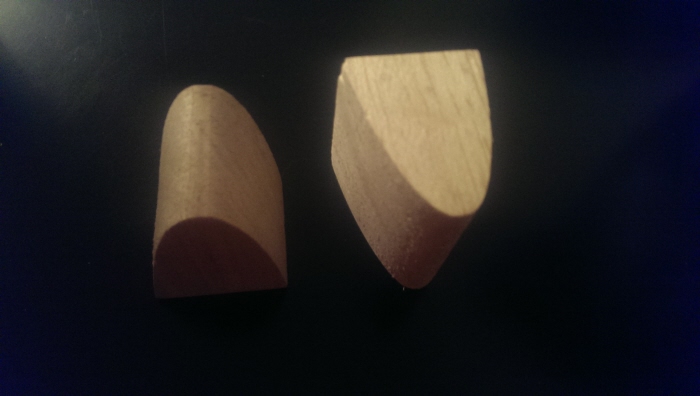
These were the first prototype leading edges cut on the CNC. The balsa required too much sanding after the cutting operations to meet our time restrictions so mahogany was used in the final versions.
gLike