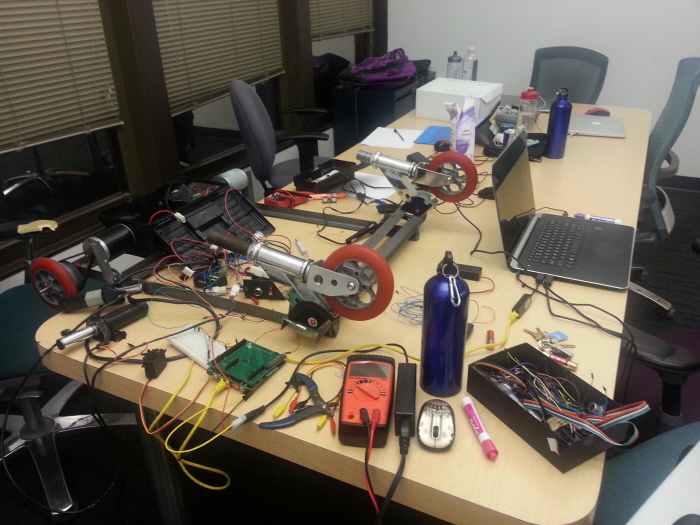
The picture above shows a scenario of our days and nights spent trying to figure out the circuit board and hardware integration. To achieve a controllable device, we programmed the SBRio board using Labview platform to transmit the signal from and to sensors and switches through different digital channels on the board.
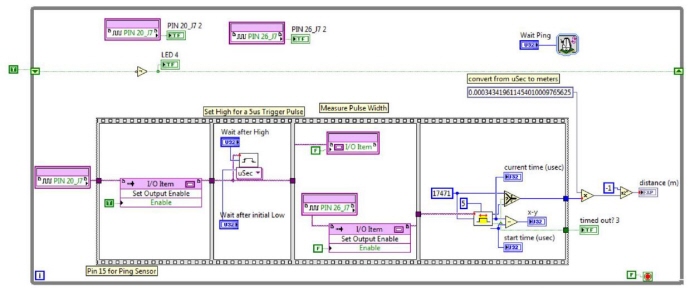
After the signals were successfully sent from and to the RIO Board by the Labview command, we processed the signals from sets of Boolean at different frequency, to some meaningful measurement values such as distance from the object. The picture above shows a broad picture of Labview code we used for obtaining the distance from a Ping))) ultrasonic sensor.
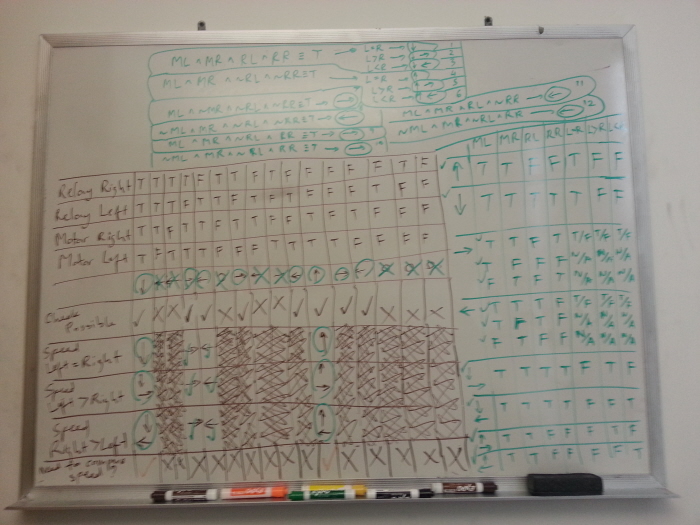
The encrypted data was used for calculating the logic, then send out the command to the system. To achieve the object avoidance, we mainly used the distance data to decide what direction the automated wheelchair should be headed toward, and how fast should each motor run. The above picture shows an example logic chart for a set of data displayed on the user interface.
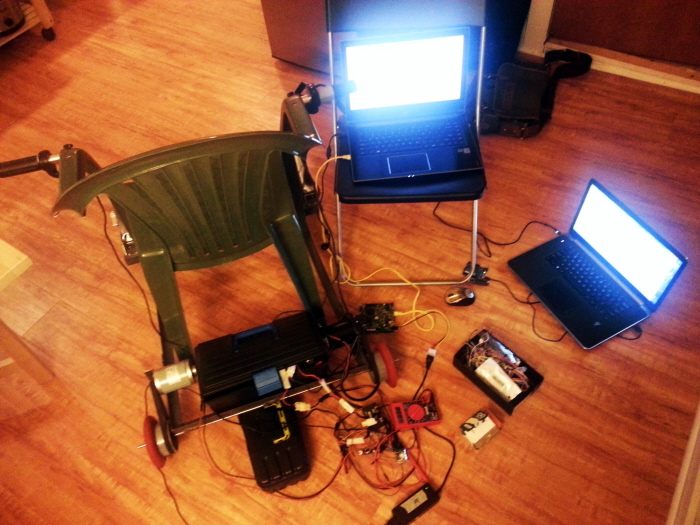
Calibration was needed for a system to perform smoothly. The main calibration we did on this automated wheelchair system was adjusting the duty cycle values for the pulse width modulation.
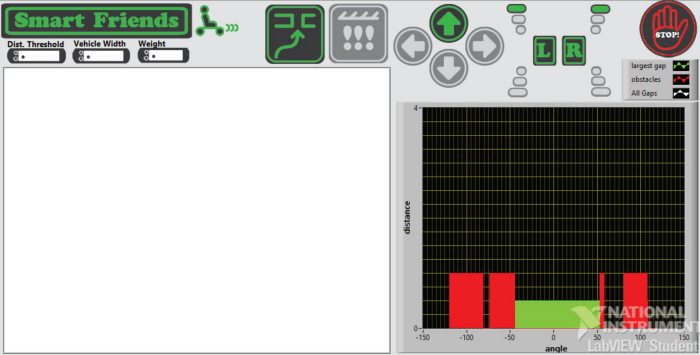
The user interface communicates between the end user and the system. It is used to show the wheelchair user where the wheelchair is heading toward and what command is the system calling, as well as a chart showing the distance from the obstacle. All the buttons were customized as shown above.
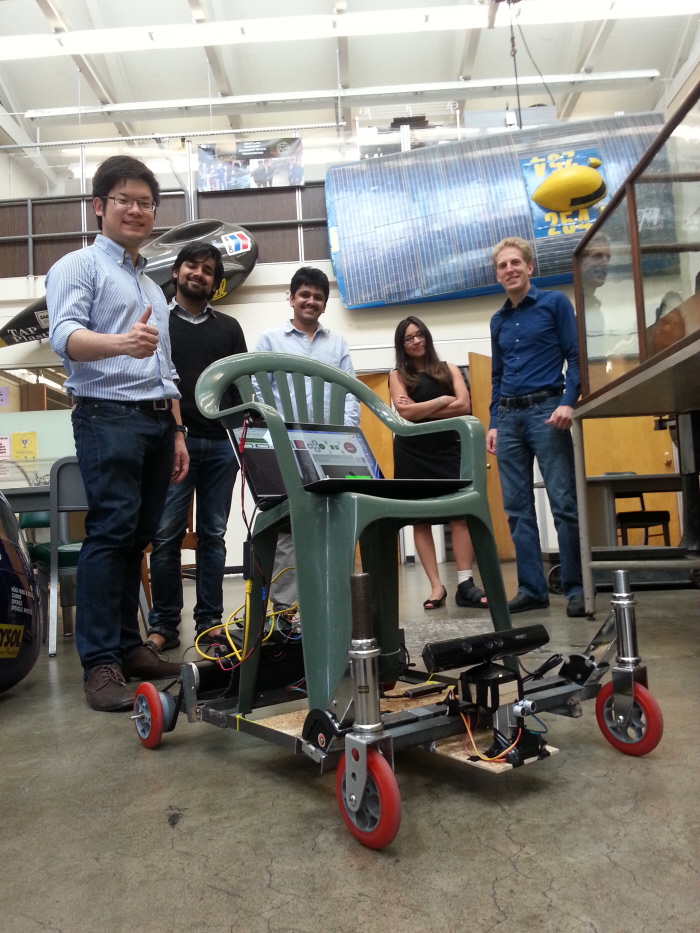
After we have improved the system to the last second, we were able to safely operated the system and have our professor tried out the system without crashing the automated wheelchair to any obstacles. Hence, time for celebrations!
gLike