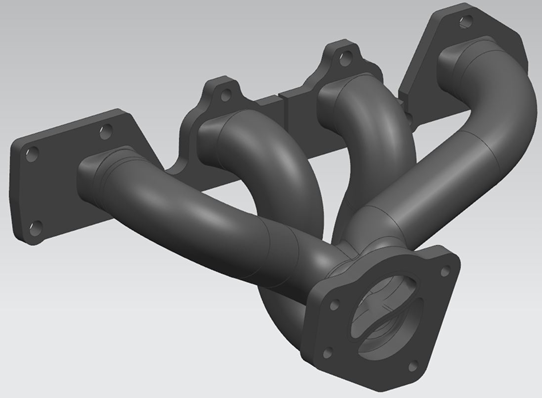
To study the flow restriction of the stock exhaust manifold for benchmarking, we remodeled the exhaust manifold using NX CAD software. The challenge lies on achieving the most accurate CAD as compared to the physical prototype.
After then, I ran a steady state CFD simulation for the flowbench test. Then we compared the results with those of four other different manifold design concepts that we designed in CAD. These simulations saved us time and resource to designing the optimal manifold shape, by bypassing the fabrications and physical tests for the less optimal designs.
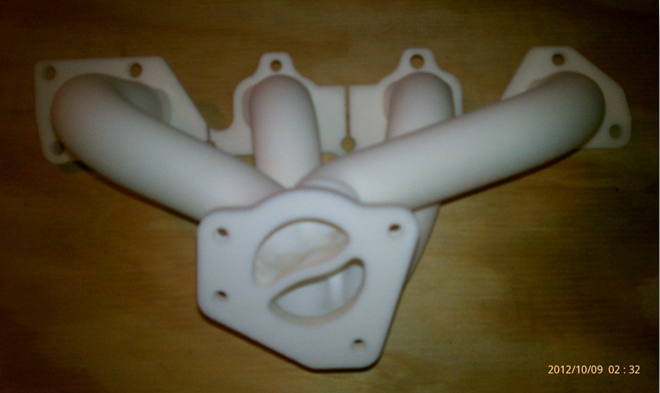
An 3D printed stock manifold was tested on the flowbench to compare the effect of the surface finishing on the flow restriction with the stock cast manifold.
After we found the results, we then continued on to fabricating the conceptually optimal manifold by tube bending and welding the stainless steel tubes. Then we again tested the optimal manifold on the flowbench to physically obtain the flow restriction measurements and compare it with the stock manifold.
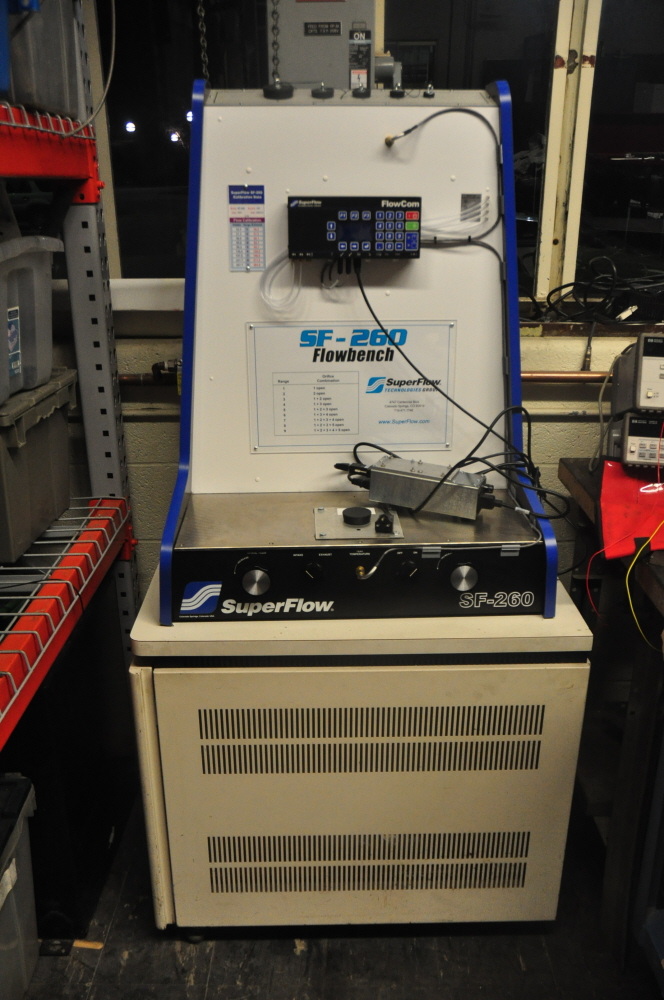
Flowbench was used for testing the steady state flow restriction on different exhaust manifold designs.
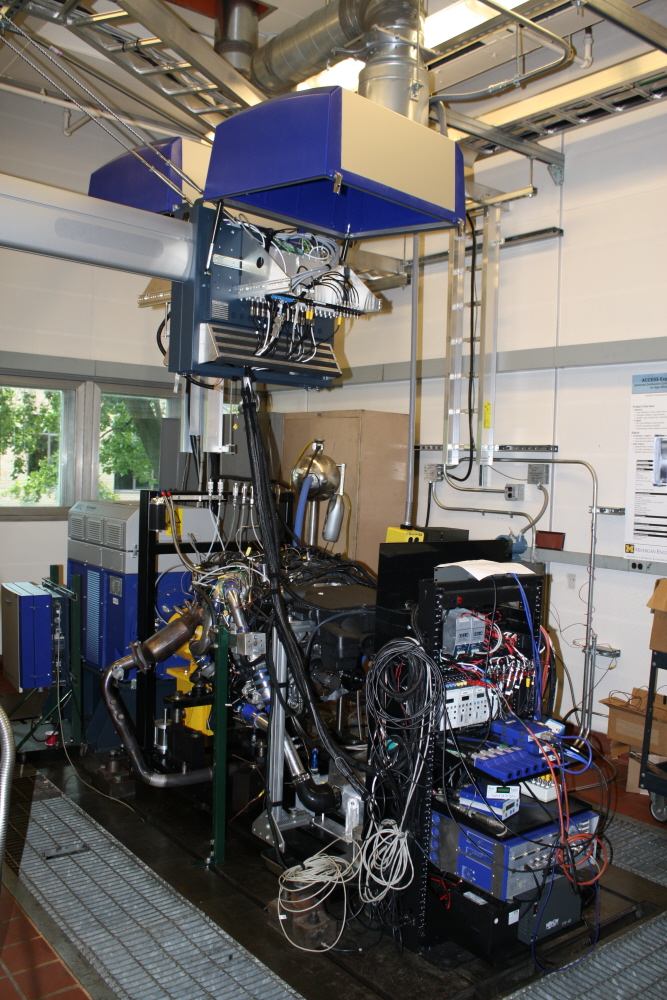
Cutting edge engine dynamometer test facility at the University of Michigan autolab was used to obtain the thermodynamics data.
To compare the performance of different manifolds on the real engine, we first validated the GT Power engine simulation model with the data obtained from the dynamometer test. After the model is validated, we used it to improve our exhaust manifold designs before start fabricating. Then we validated our final results of the manifold simulation again with that of the fabricated part in the dynamometer test.
gLike