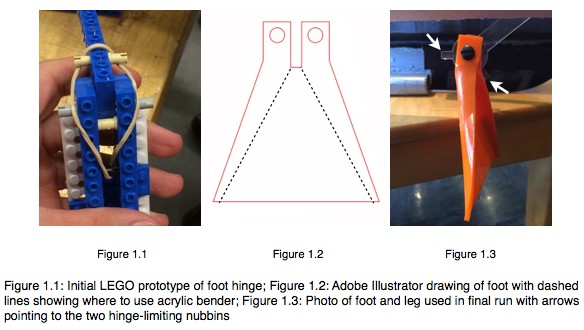
Description in picture
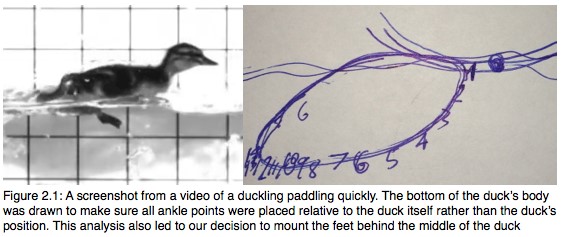
Description in picture
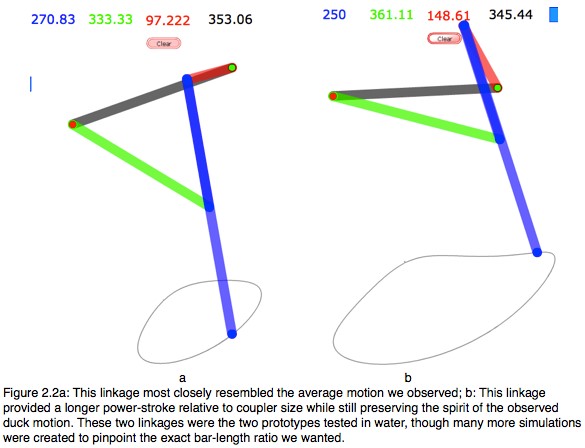
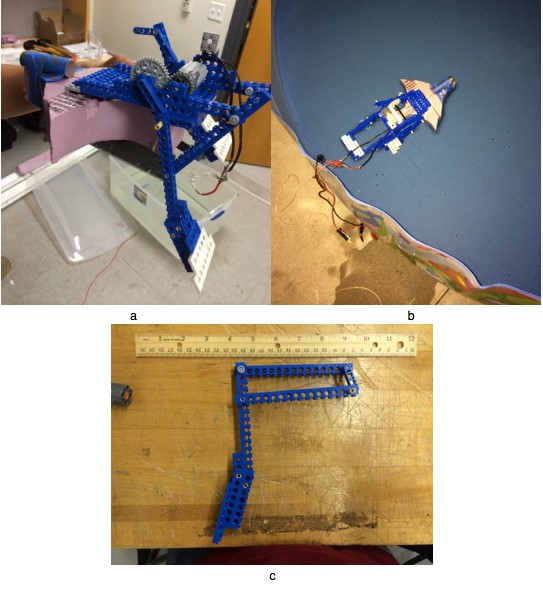
Figure 2.3a: One prototype linkage on a makeshift LEGO and foam duck prototype; b: the same linkage being tested in the water; c: linkage with foot attached to rocker arm
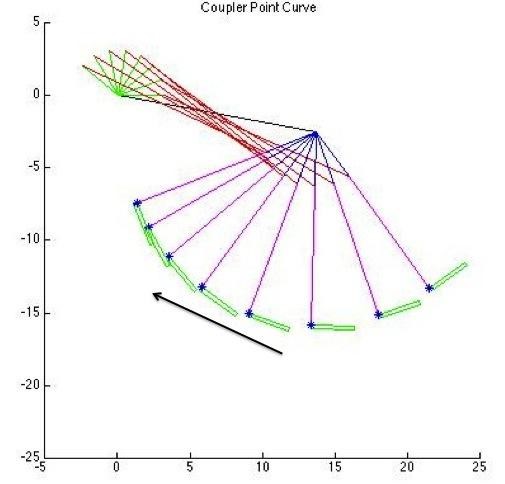
Matlab analysis of four-bar linkage coupler curve, of duck's RECOVERY stroke while paddling
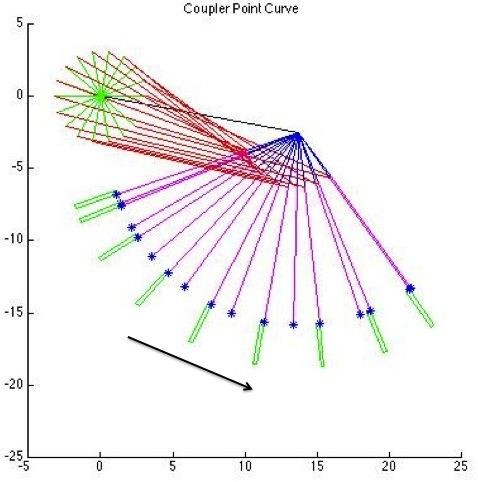
Matlab analysis of four-bar linkage coupler curve, of duck's POWER stroke while paddling
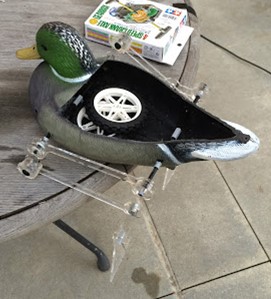
Final four-bar linkage design, fused to decoy body
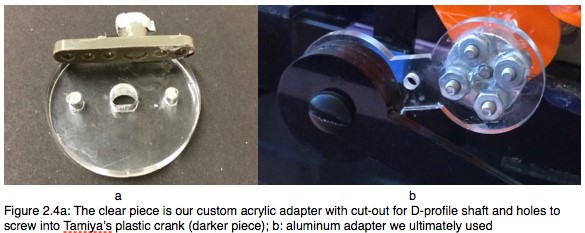
Description in picture
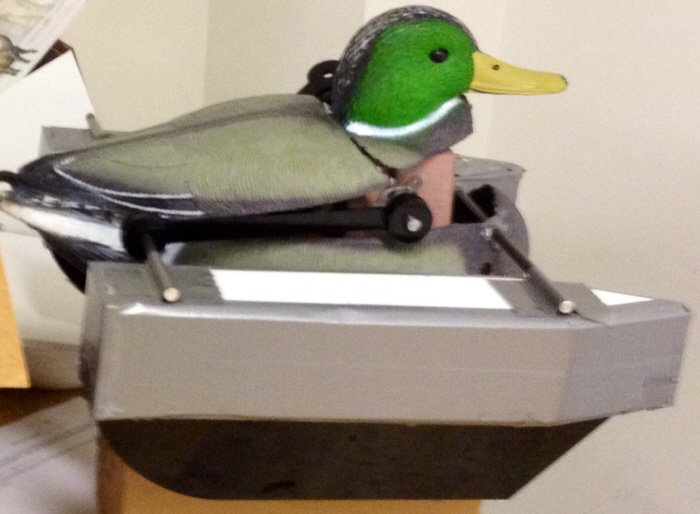
Third iteration of duck, adopting a trimaran, triple keel design for stability during paddling
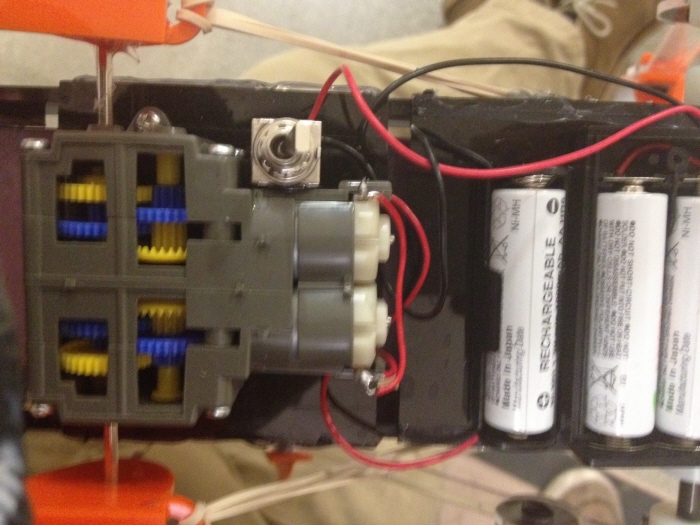
Top view of Tamiya motor, transmission, switch, and power source
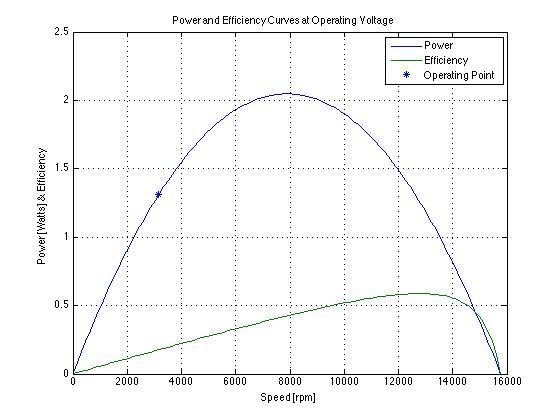
Matlab created estimate of Tamiya motor's power output and efficiency, given our operating requirements. Adequately mimics the power (metabolic) consumption of an actual duck.
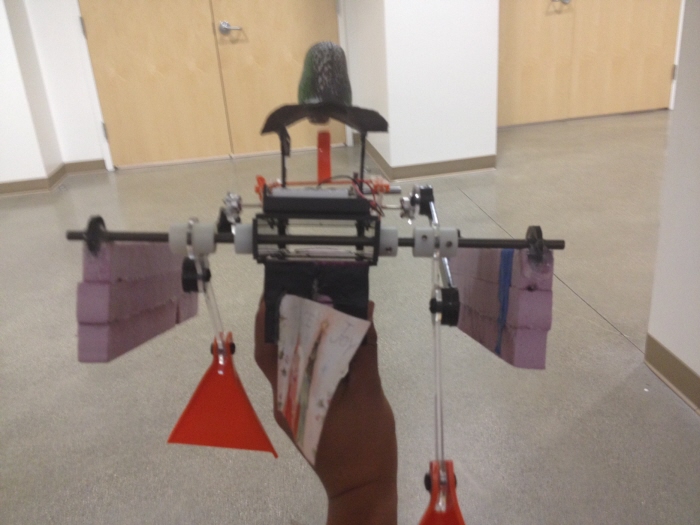
Back view, displaying trim rudder
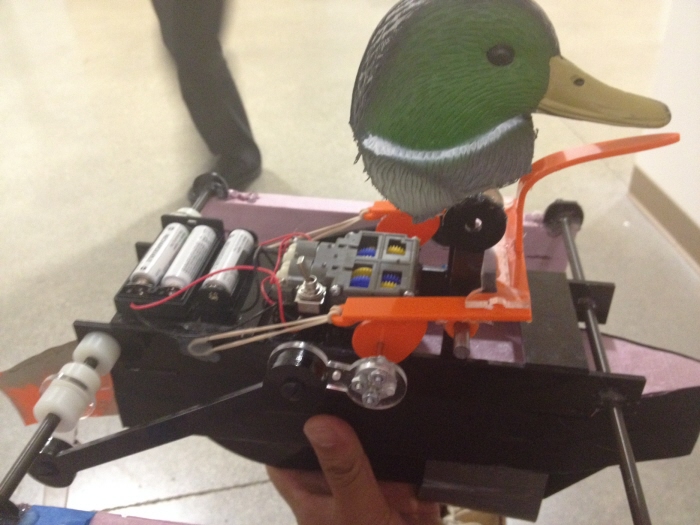
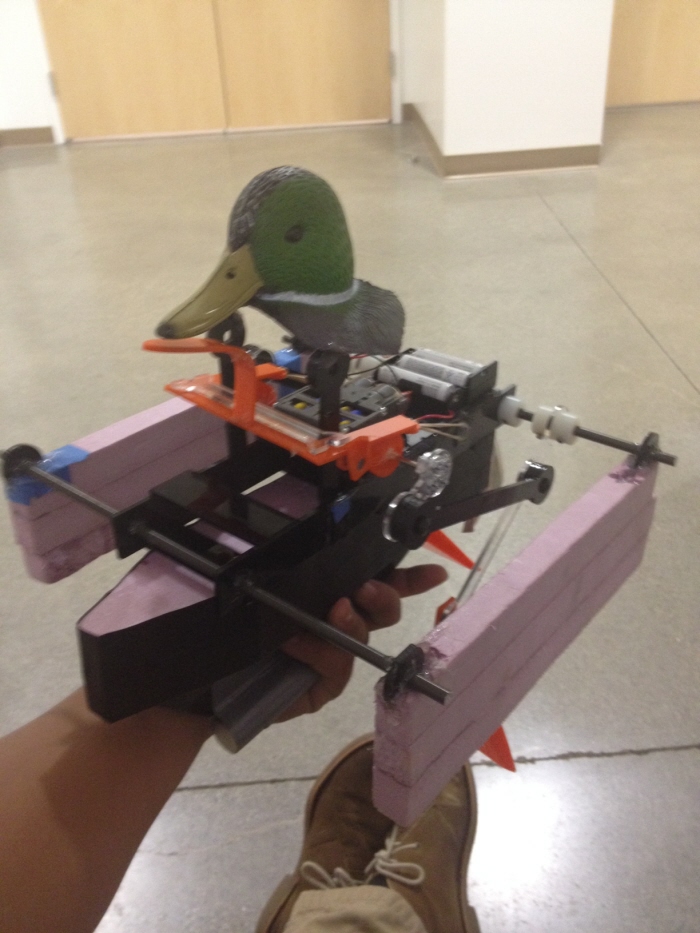
gLike