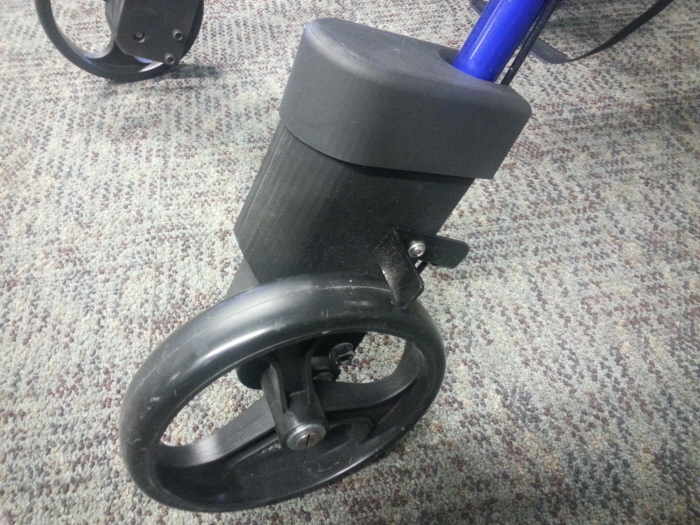
Clutch system housing. This and several other custom parts were fabricated through 3D printing.
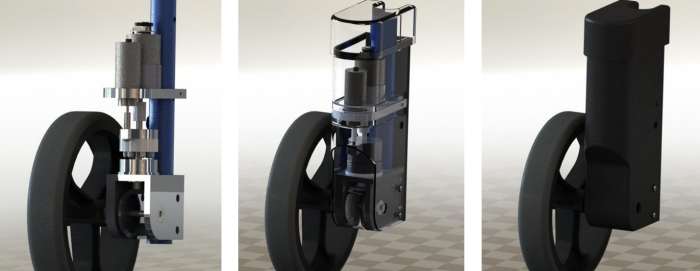
Render of clutch system without housing, with transparent housing, and with actual housing.
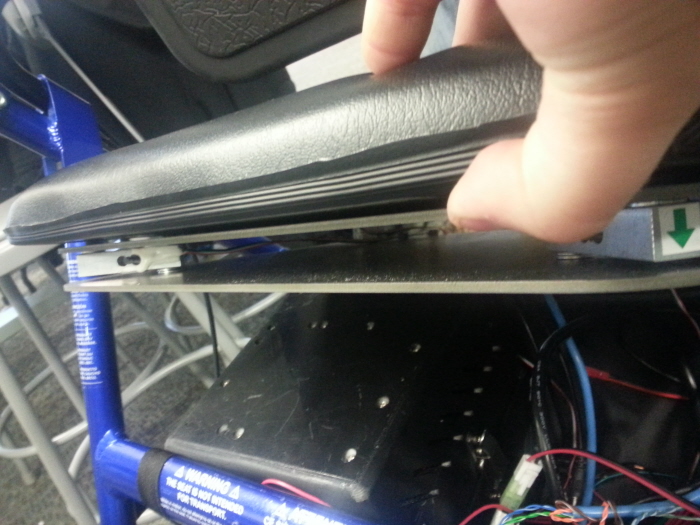
Seat with load cells in each corner. By monitoring the load distribution under the seat, we could measure the location of the user's center of gravity and how often in moves. Through this monitoring, a care taker could see if the user is becoming stagnant which increases their risk of developing pressure sores.
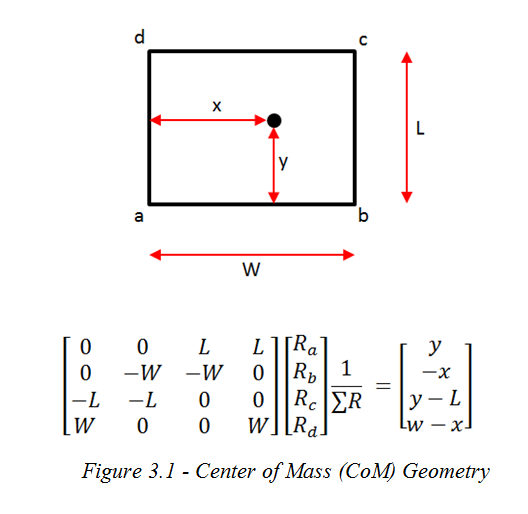
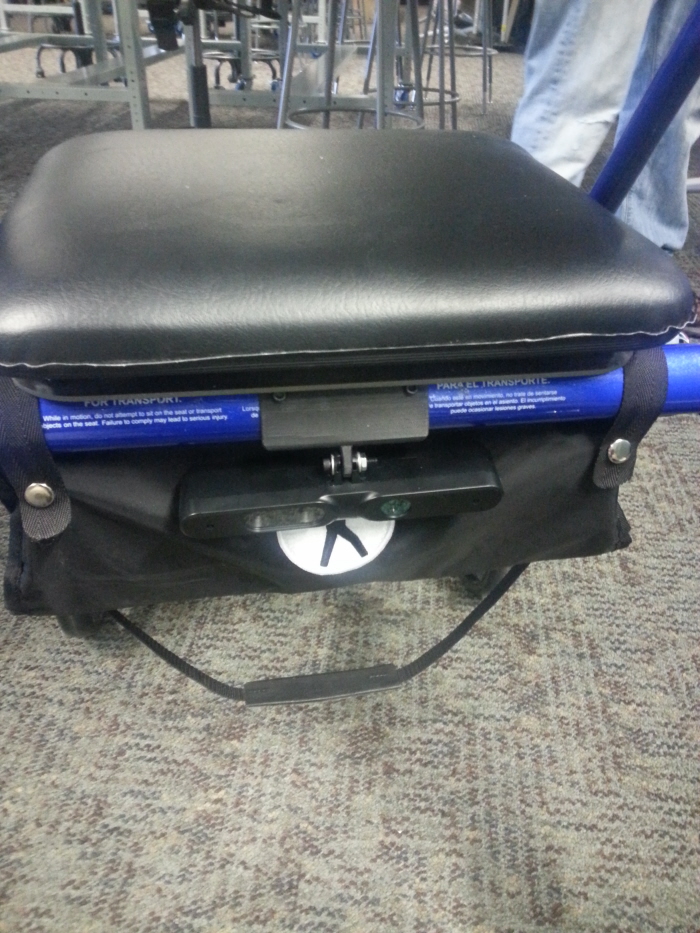
Seat and 3D camera. An Xtion depth sensing camera was custom mounted to the frame of the walker to be used with SLAM for path finding operations.
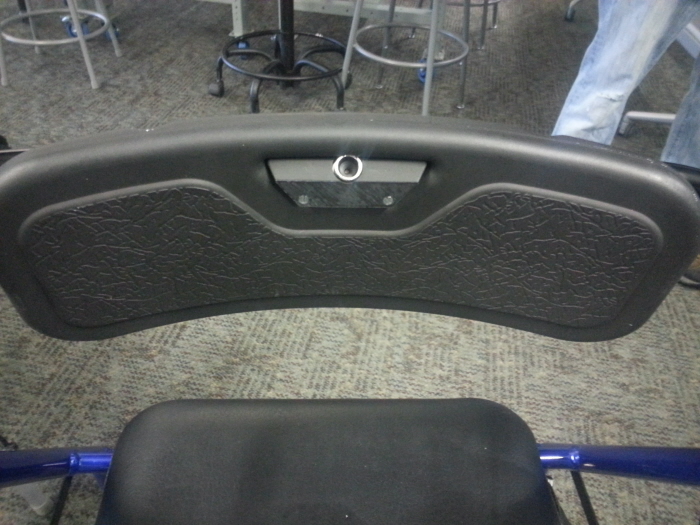
Web cam mounted in the chair back. This camera was positioned to monitor the user's face while they walk. A special algorithm calculated the user's pulse by looking for minute changes in the size of the user's face and neck. This method was chosen as the customer dictated that the patient must not wear any special monitoring devices.
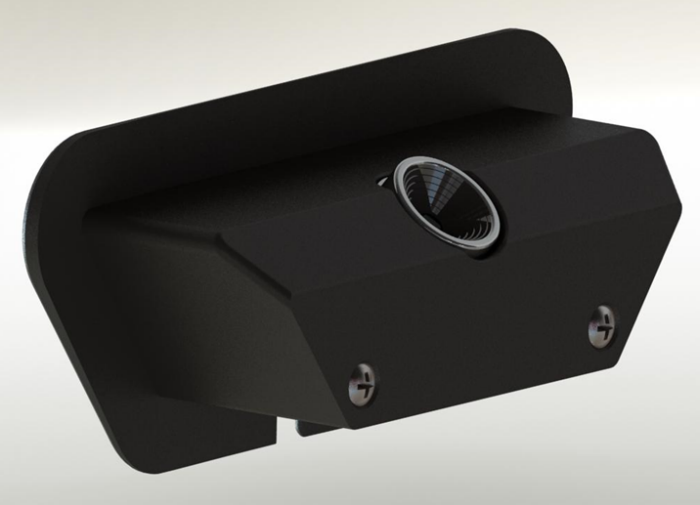
gLike