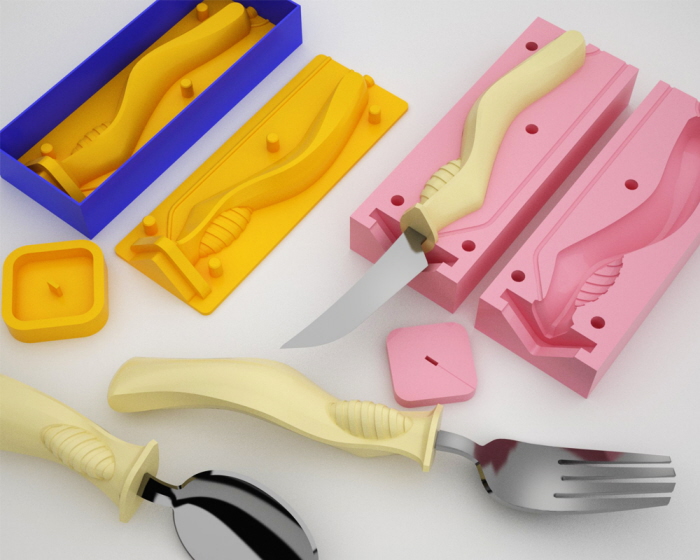
3D printed “positive” for mold creation (yellow parts), RTV mold (pink parts) and final products.
Won 1st place in - Creating Tomorrow's Products 2013, a competition held by the Reut institute focusing on creating products for handicapped people by using rapid manufacturing technologies.
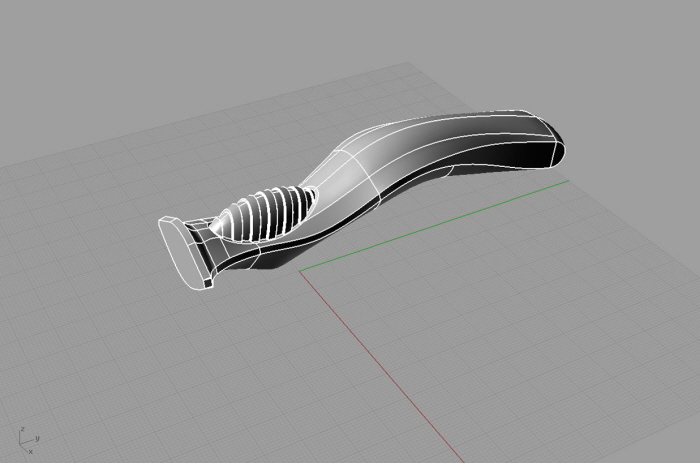
CAD model
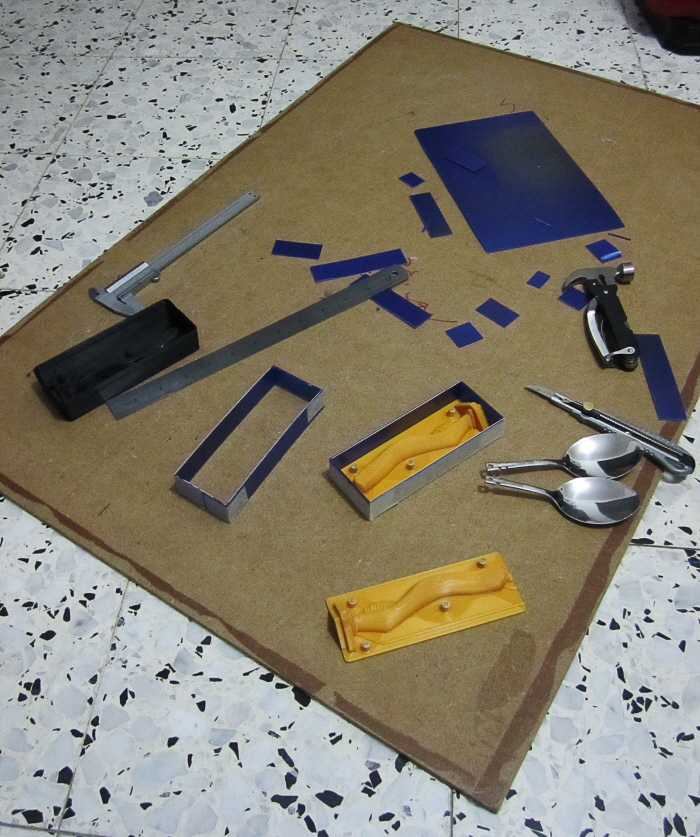
using 3D printed parts to make the molds for the RTV mold parts
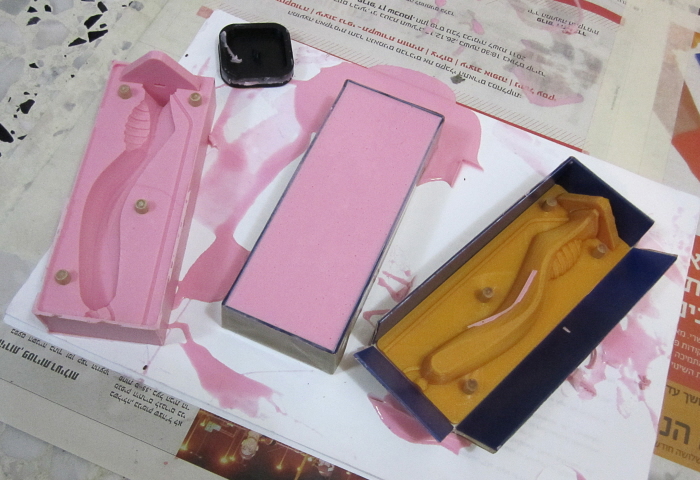
RTV mold is ready
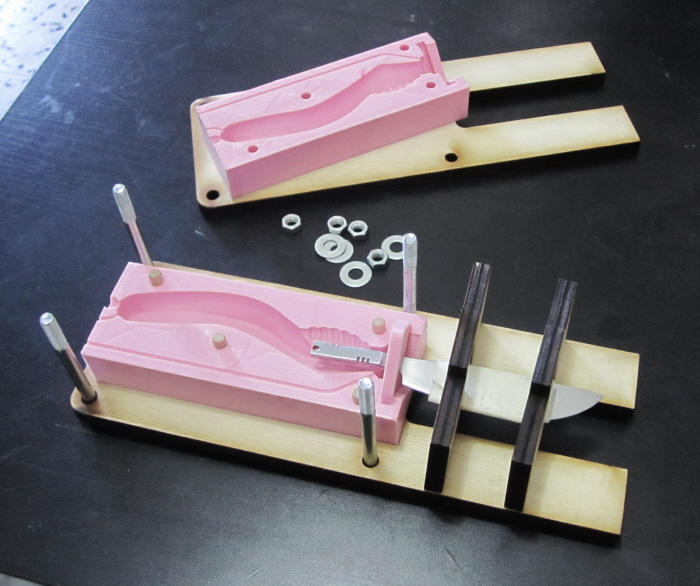
preparing to cast a knife
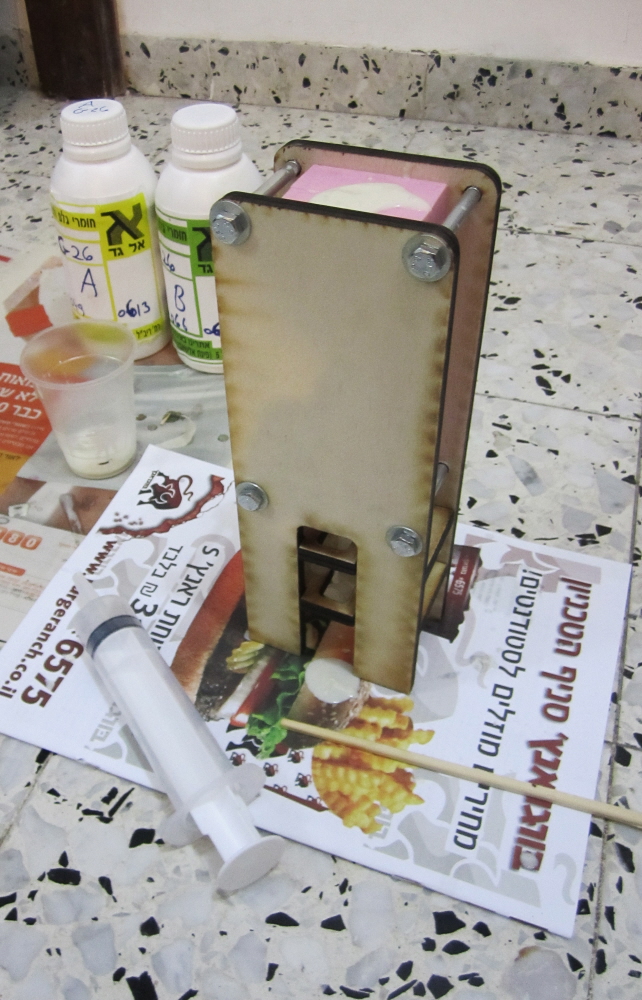
casting G-26
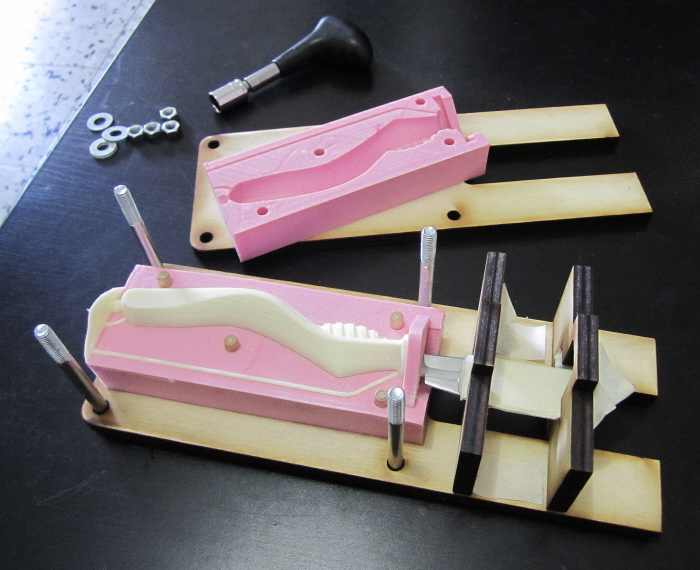
about 20 minutes after casting
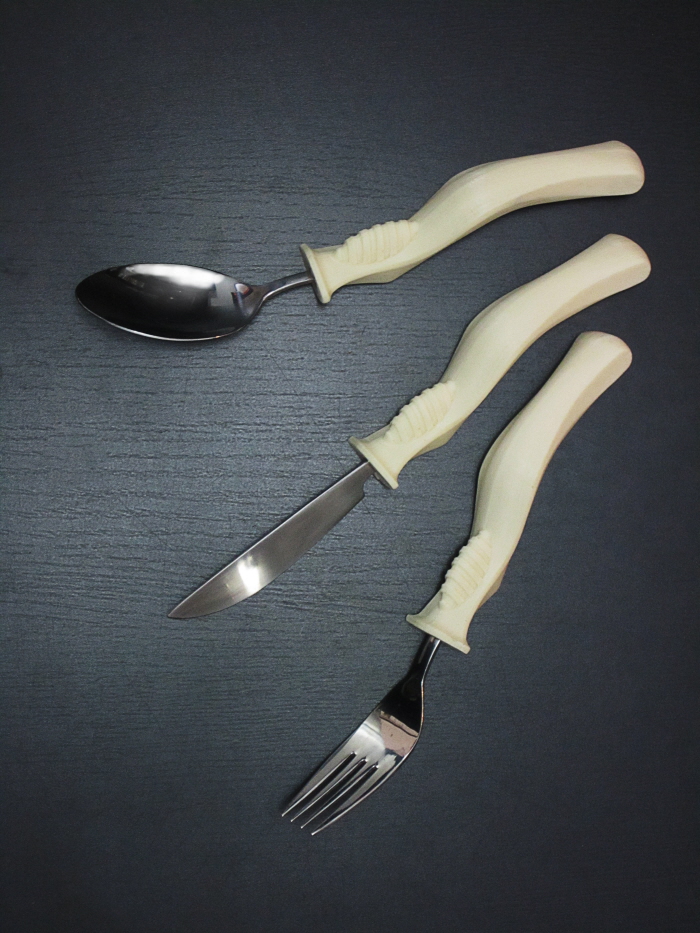
end result
gLike