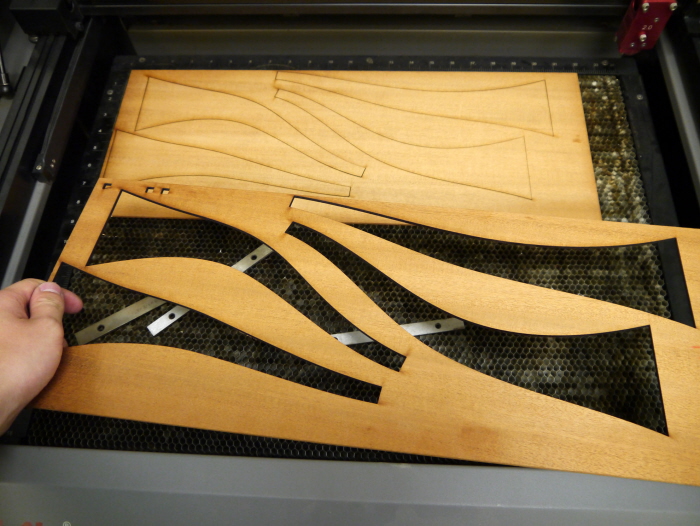
Laser cut mahogany veneers, paying close attention to grain orientation.
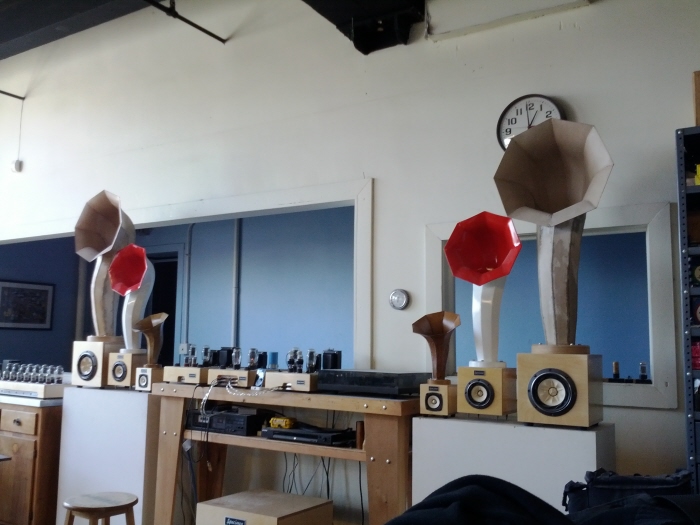
All the horns and amps you see are hand built and designed here in Chicago!
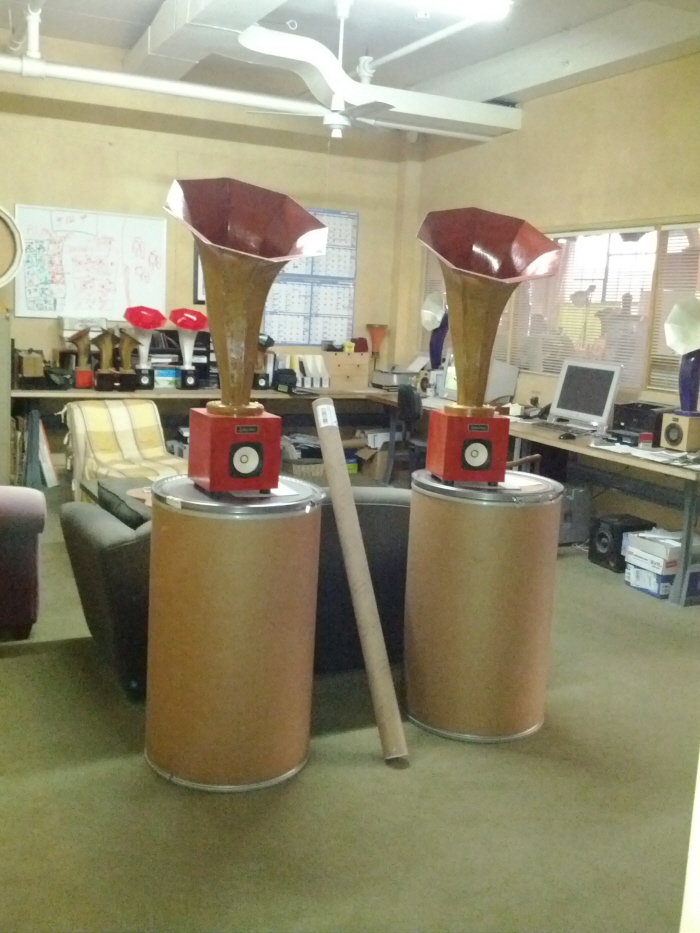
Working out shipping containers
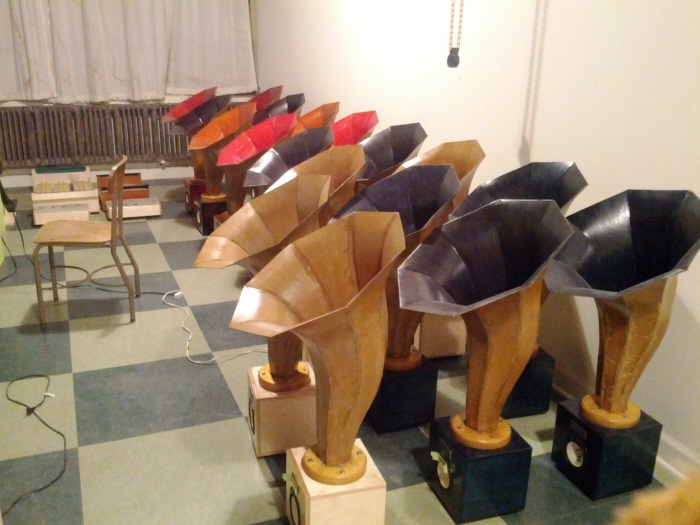
Before we sold off most of the speakerhorns built for the Museum of Contemporary Art show that Ian titled "Sonic Arboretum," there are a few remaining
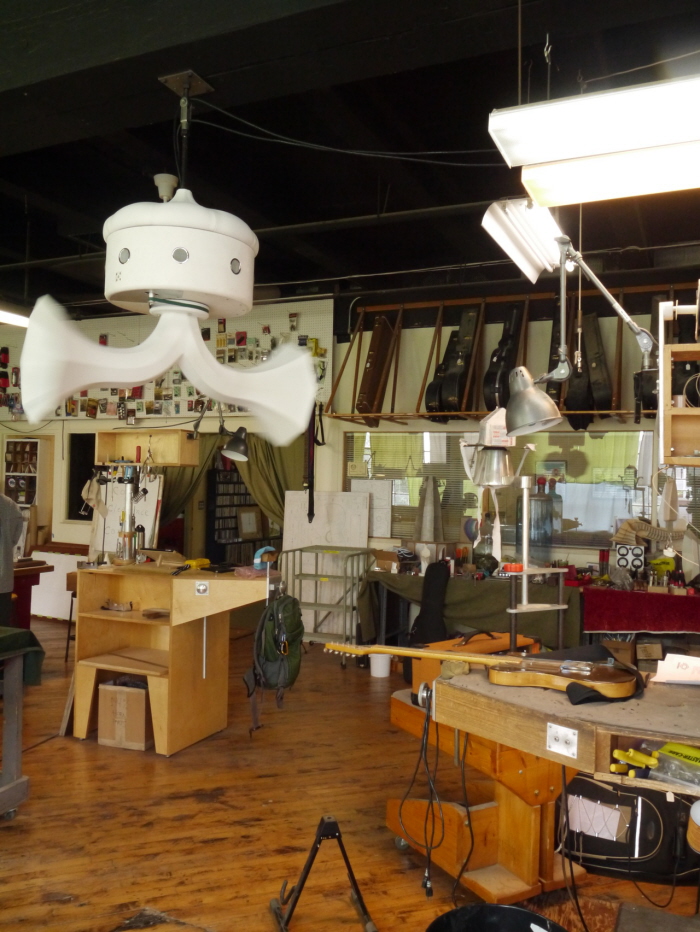
Custom project
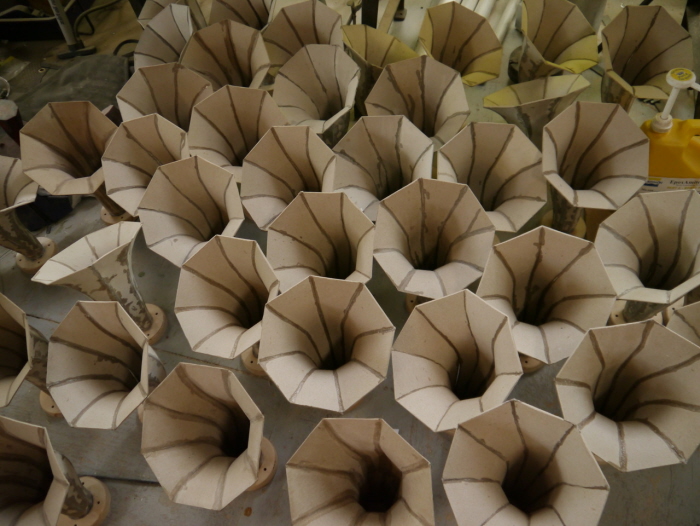
Hornlings being prepped for their natural finishes using the same nitrocellulose lacquer we use on our stringed instruments
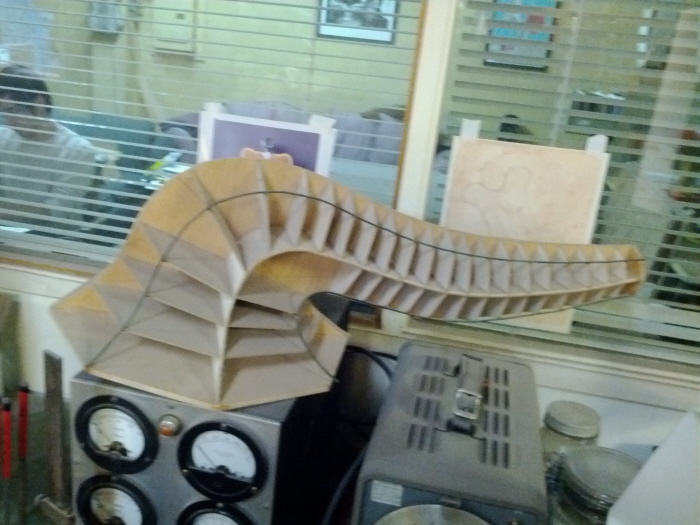
Building models is essential for figuring out geometry
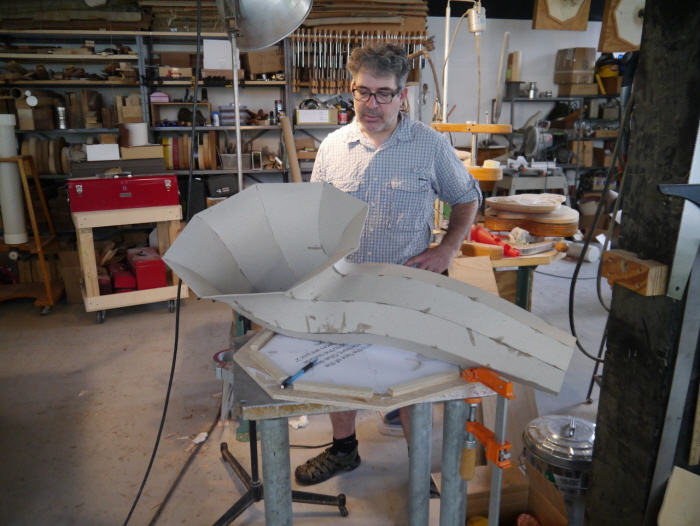
One of our larger horns commissioned by a very exciting Chicago restaurant
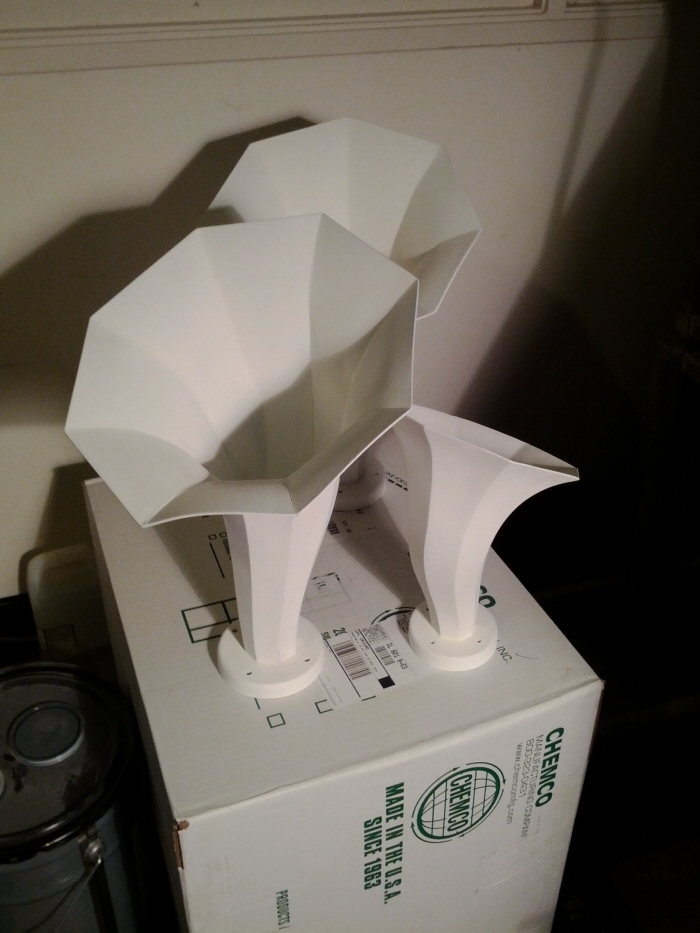
First coats
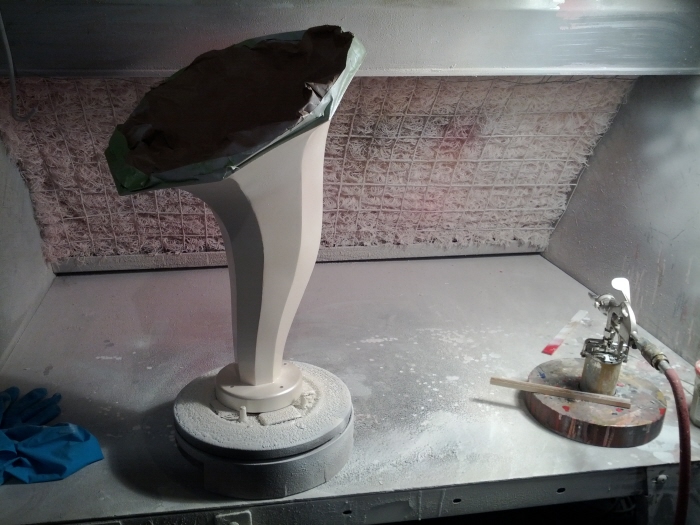
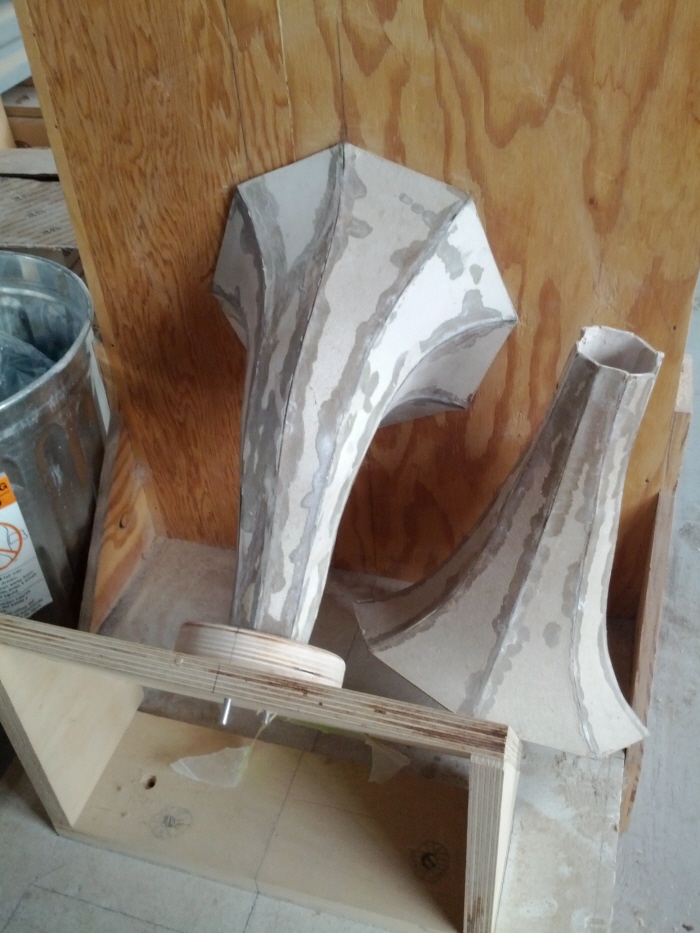
Jig for setting the correct angle and height of each horn. Each horn comes out perfect.
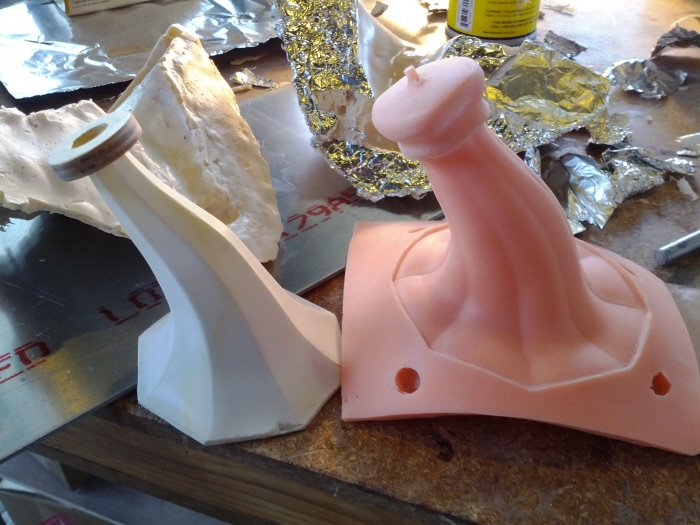
Our smallest horn only measures a few inches tall
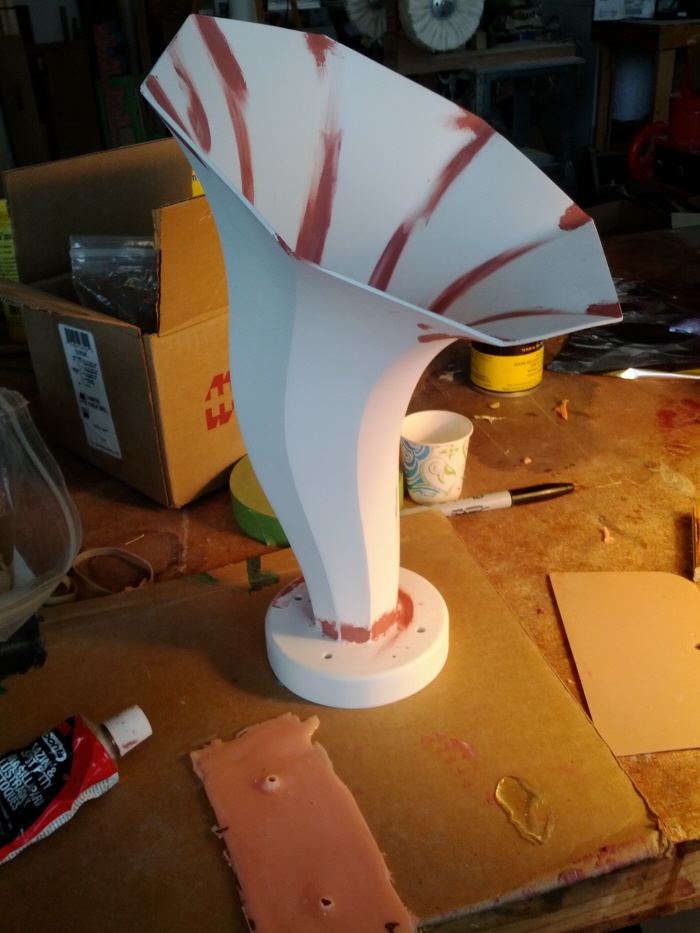
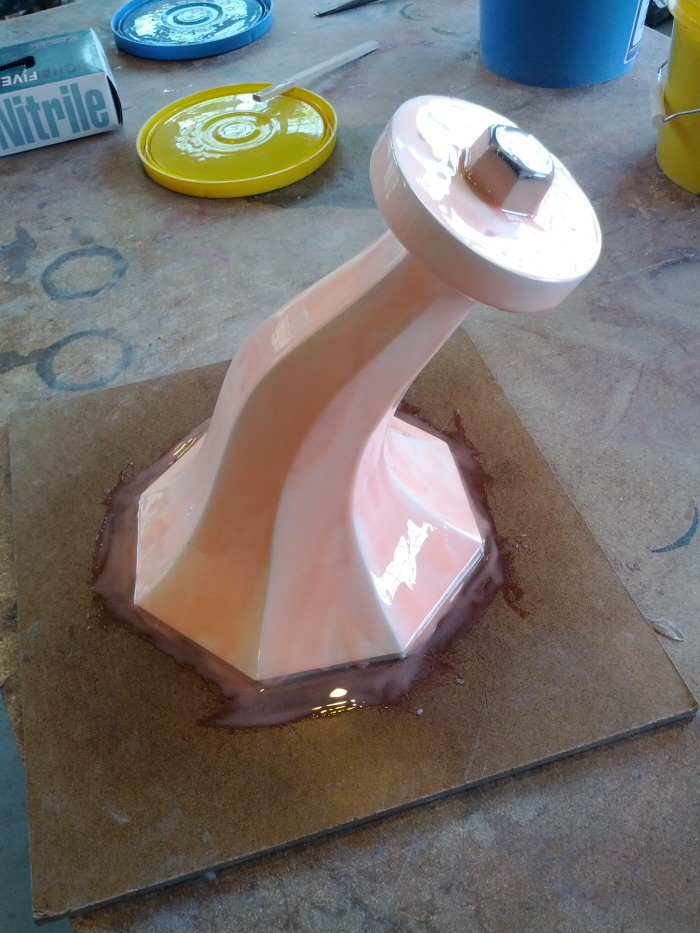
Thin layers
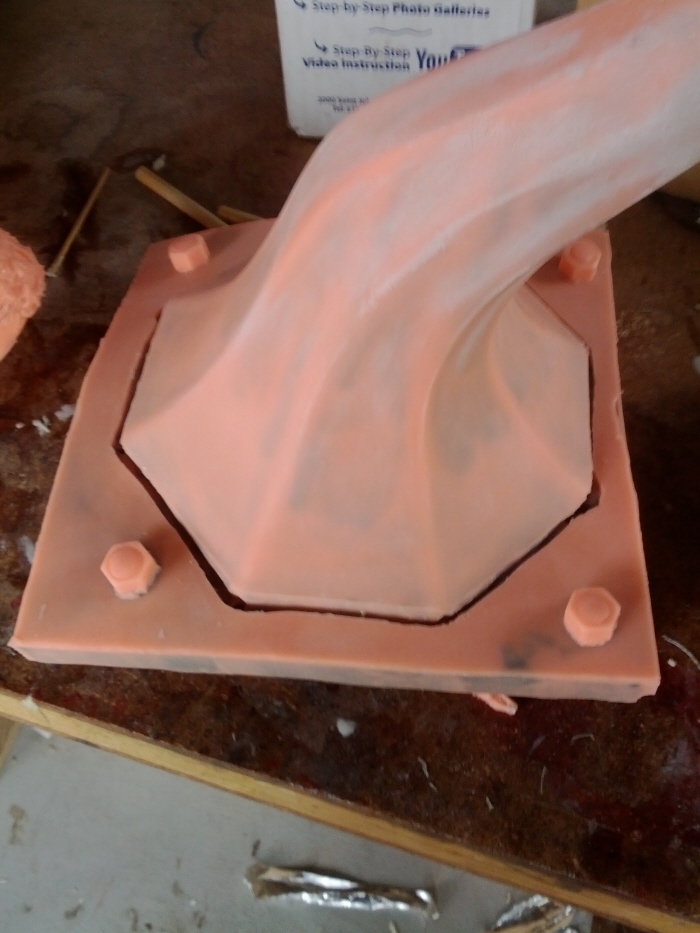
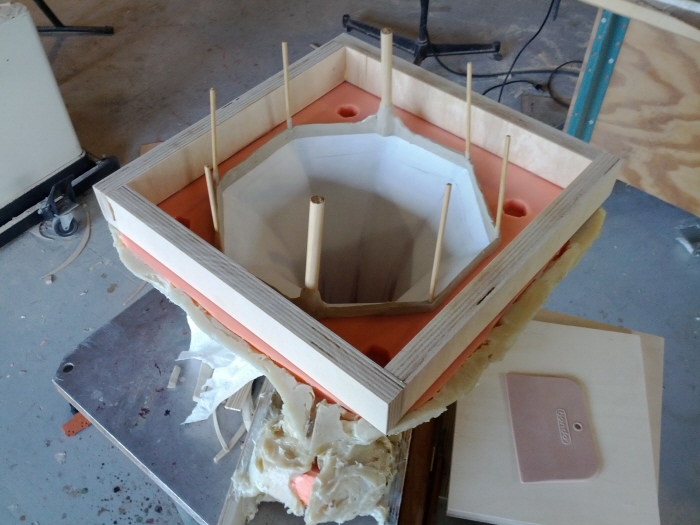
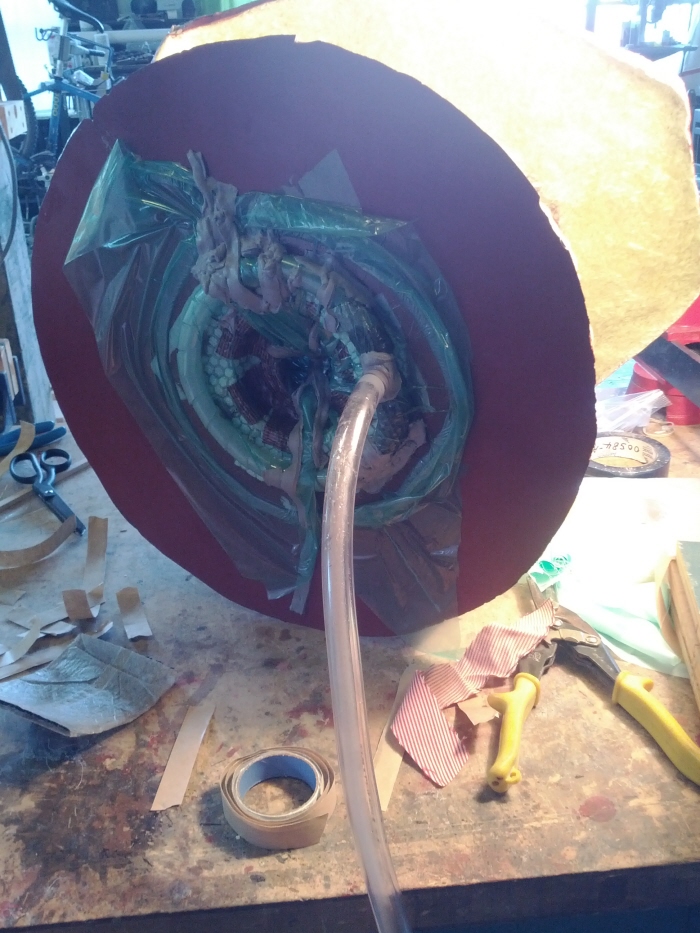
Vacuum infusion molding, only the biggest mold I built due to the flange, but otherwise such a better way to mold.
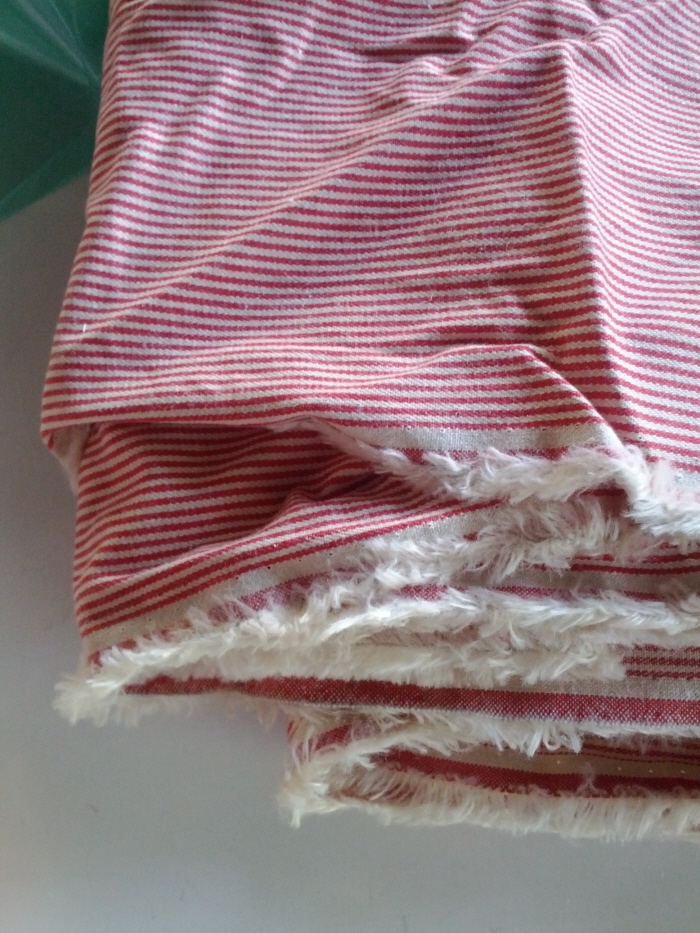
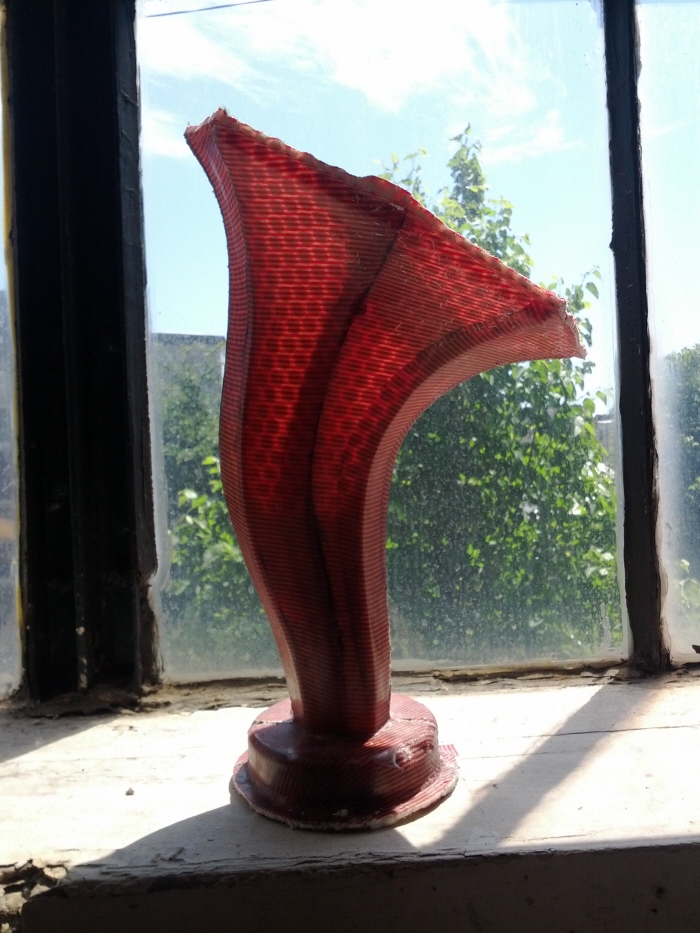
First vacuum infusion molded part
gLike