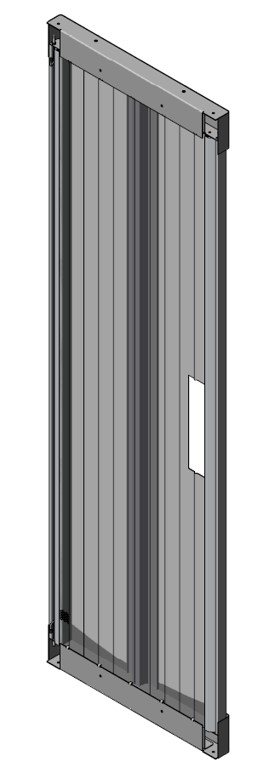
1st concept in early design stage - This concept requires no secondary machining to the side supports (aluminum extrusions), eliminating significant cycle time and cost.
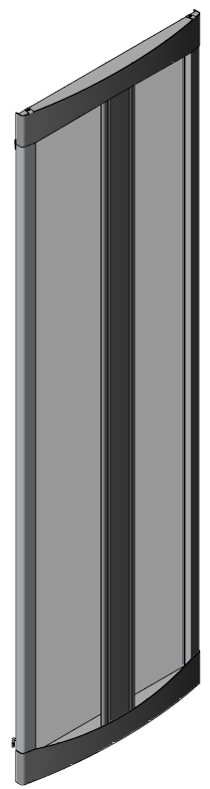
Front view of 1st Concept
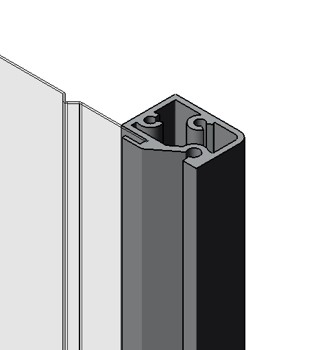
Close-up of 1st concept - shows the cross-section of the extruded aluminum side supports. By including a slot in the extrusion design, the perforated sheet can be sandwiched by the slot rather than by rivets via machined holes (existing design). This is a second design feature that eliminates secondary machining with no additional costs.
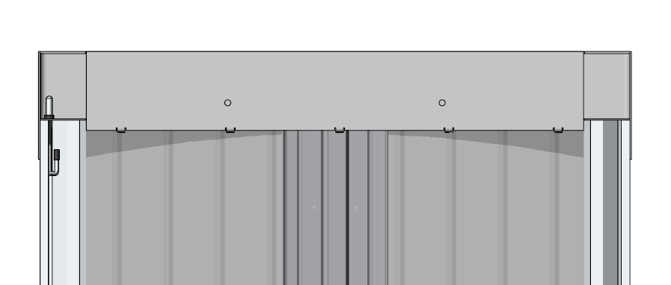
Pocket Close-up - My hinge design significantly simplified the attaching and detaching of the doors by using a spring-loaded hinge pin. On top of this, the new hinges cost 28% less than the original hinges.
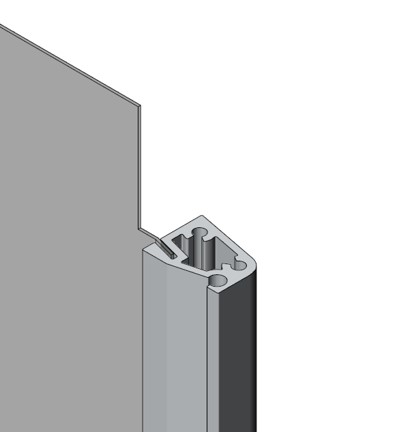
Close-up of 2nd concept - shows the cross-section of the extruded aluminum side supports. In this design, the perforated sheet is actually bent during assembly to tighten it against the front fascia. This prevented any vibration upon closing resulting in a higher quality feel.
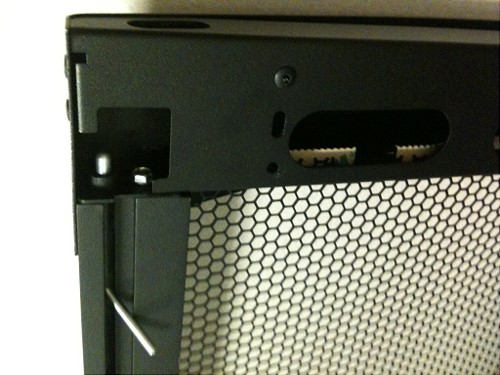
Prototype Design - The first prototype design was very successful with only a few minor changes needed to prevent unwanted airflow. I am proud to say the door is now in production on CPI TeraFrame cabinets.
gLike