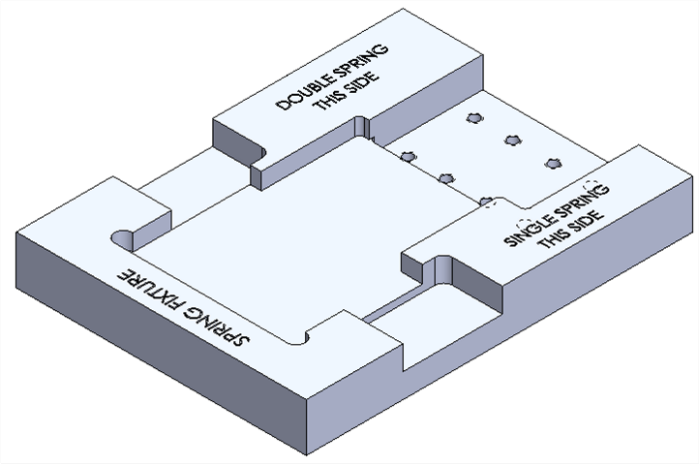
The base plate model can be used for both the single and double spring installation fixtures. This reduces the number of part numbers and CNC codes that Datacard needs to maintain.
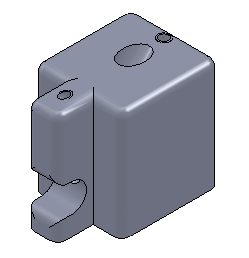
This is the single spring installation head.
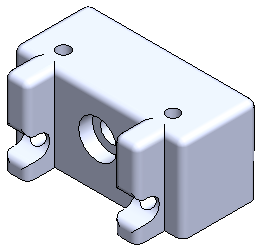
This is the double spring installation head.
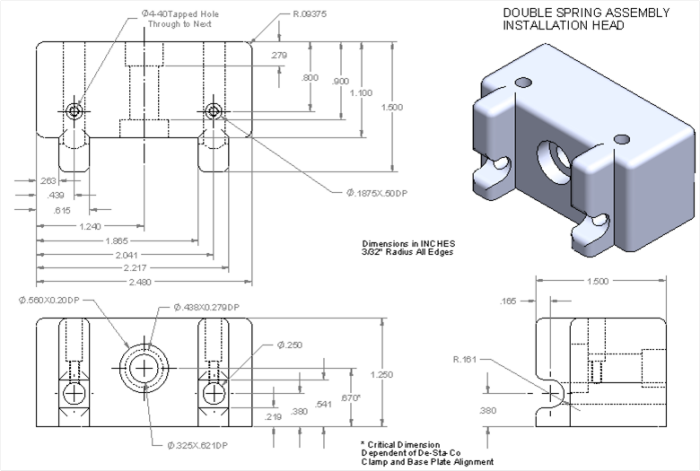
Machining drawings were used to communicate design requirements to the machining staff. I learned how to appropriately use datums for easy reference and how to manage dimensioning tolerances.
gLike