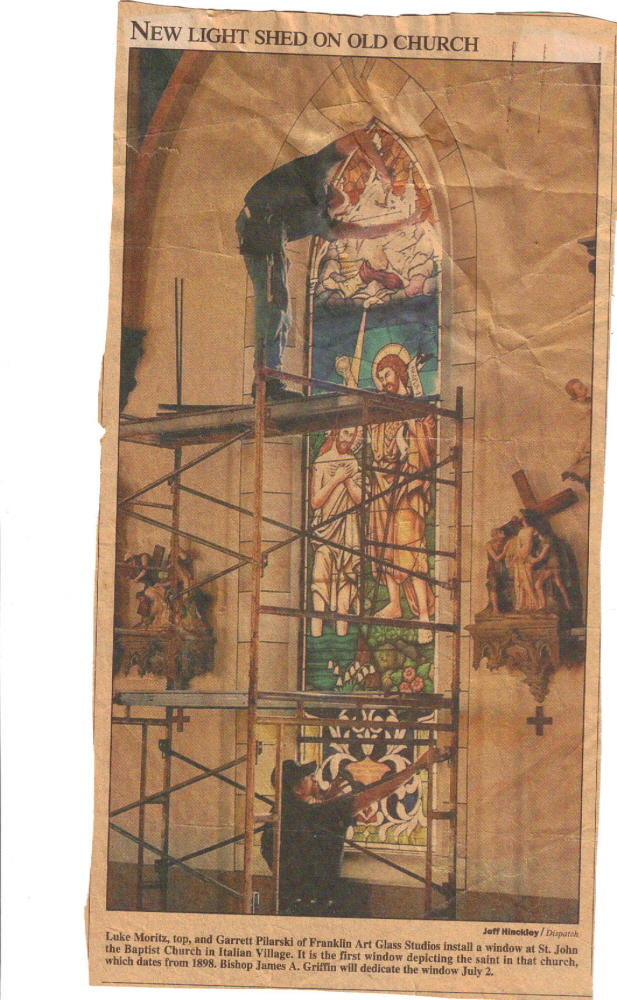
A window I installed with my field partner Garrett Pilarski (who is now custom Glass Manager) while with Franklin Art Glass for St. John the Baptist.
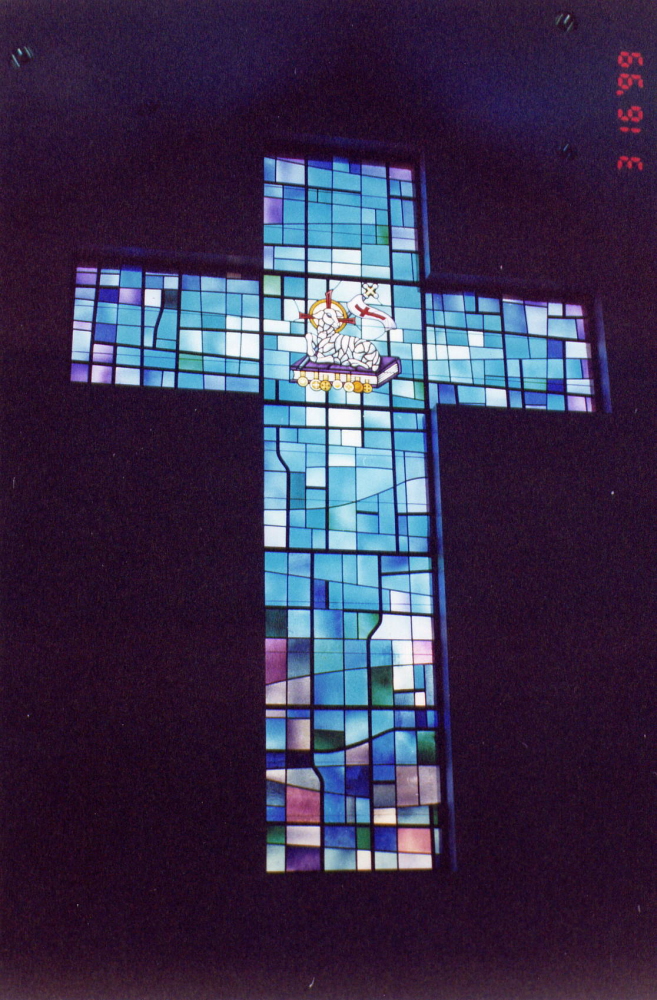
A window Garrett and I installed at Holy Family in Stubenville. We utilized a stack of rolling scaffold to complete the intsallation. http://holyfamilyofsteubenville.4lpi.com/
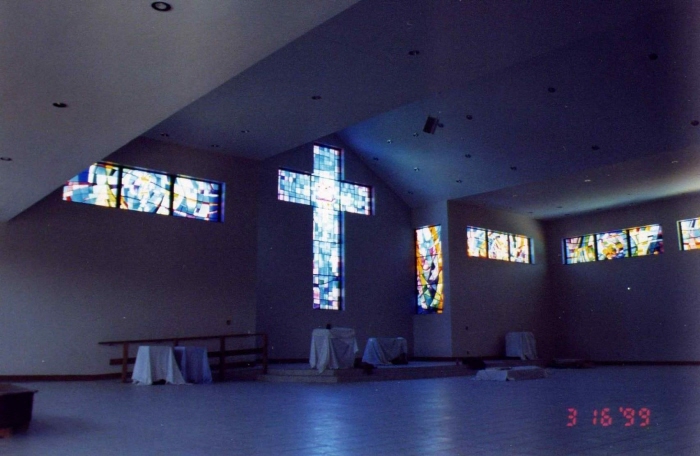
Windows Garrett and I installed at Holy Family in Stubenville. We utilized a stack of rolling scaffold to complete the intsallation. http://holyfamilyofsteubenville.4lpi.com/
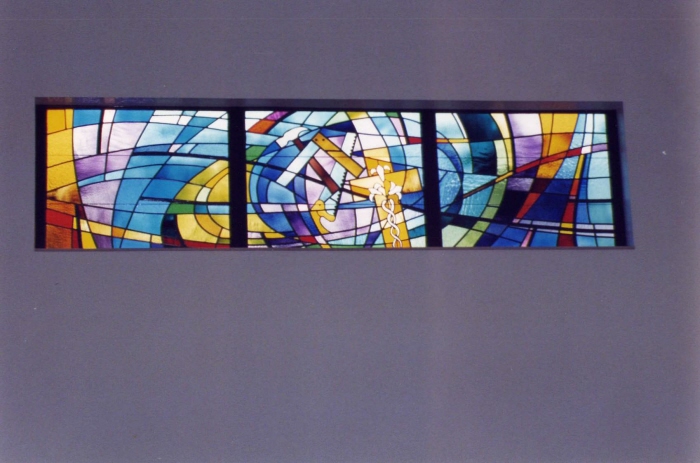
Windows Garrett and I installed at Holy Family in Stubenville. We utilized a stack of rolling scaffold to complete the intsallation. http://holyfamilyofsteubenville.4lpi.com/
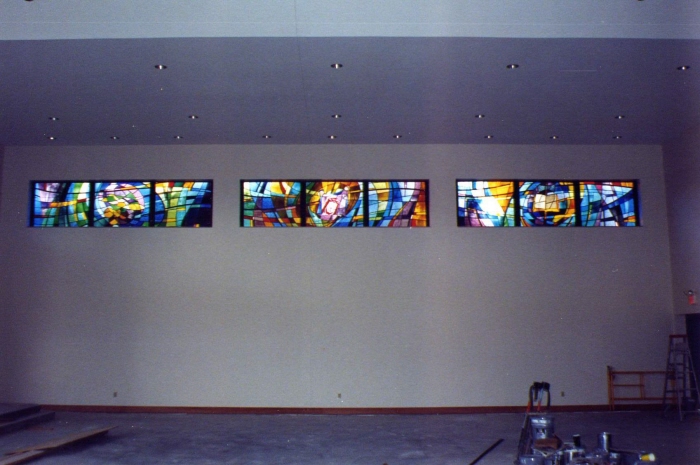
A window Garrett and I installed at Holy Family in Stubenville. We utilized a stack of rolling scaffold to complete the intsallation. http://holyfamilyofsteubenville.4lpi.com/
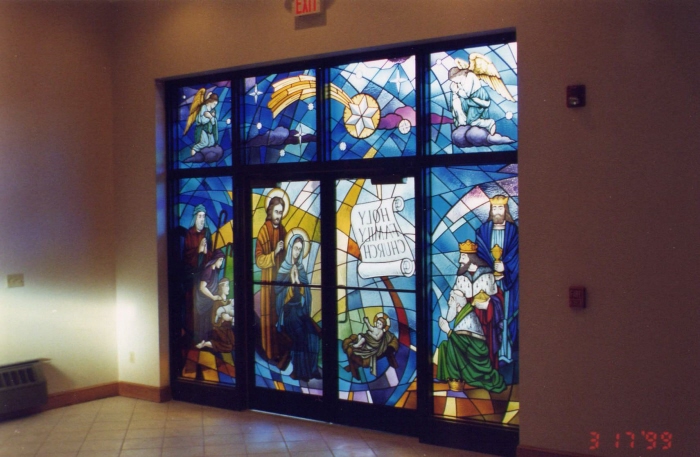
An entry Garrett and I installed at Holy Family in Stubenville. These panels clearly visible on their website, here: http://holyfamilyofsteubenville.4lpi.com/
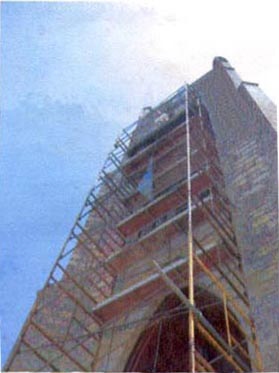
Here I am pulling up glass for the protective glazing at St. Thomas Aquinas, in Zanesville, Ohio. The top of this window is about sixty feet from the surface of 5th. street. This was a tricky build of scaffold! Garrett had me out of my comfort zone on this one. It was constructed on a wooden platform we built over the front steps.
This is a shot of the platform we constructed which supported our scaffolding while spanning one of the three groups of steps on 5th St.
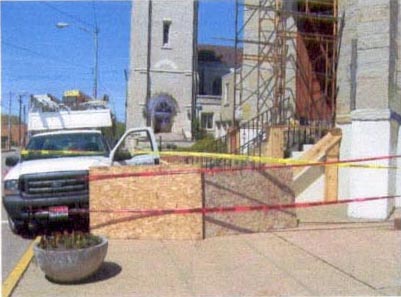
Our safety barricade of the sidewalk around our work area.
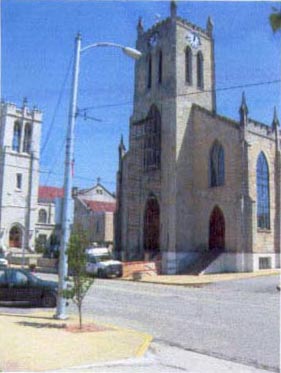
A view of our stack from across the street.
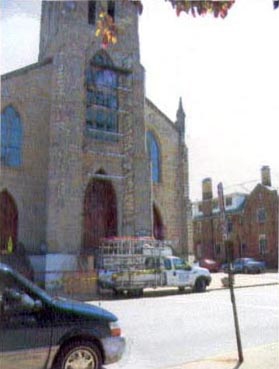
A view of our stack from across the street.
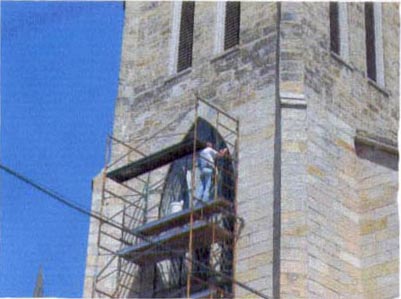
Here I am installing glass high above 5th St.
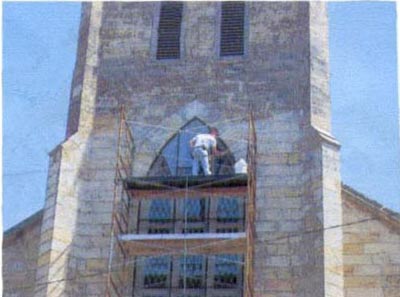
Here I am installing glass high above 5th St.
We did a repair/scrape/paint on all of these before installing the protective glazing. We made templates of the opening and Garrett fabricated all of the frames for us to assemble and install in the field. This is the North side.
The tower window after completion. This is the West side.
We did a repair/scrape/paint on all of these before installing the protective glazing. We made templates of the opening and Garrett fabricated all of the frames for us to assemble and install in the field. This is the South side.
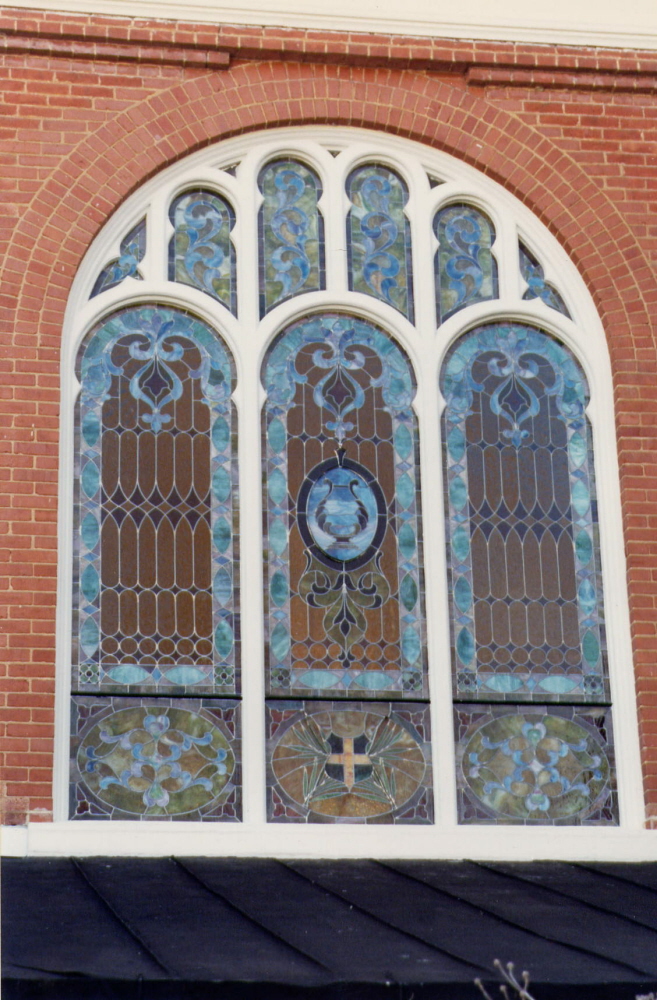
A project outside of Boalsburg, Pa., near State College, when I was with Whitney Stained Glass. His shop restored all of the frames and stained glass in the church. He collaborated with Art Femenella on this project. We used a two-part epoxy resin during the wood restoration portion of the work. I did a lot of scraping and painting on this job, as well as window take-apart, cementing, and soldering on vertical exterior support fins made from thin strips of brass. The fins are a bit hard to see here as the goal was to bend them around design elements so as not to detract from the beauty of the glass.
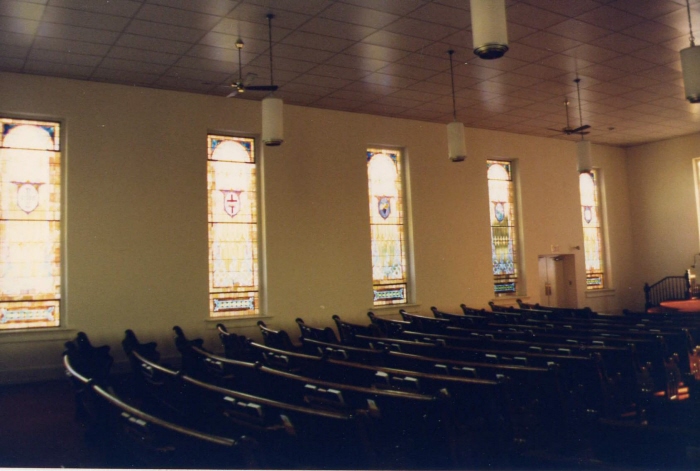
Interior shot after installation was completed. A little overexposed but was using a 35mm SLR camera. Digital makes getting the exposures right SO much easier!
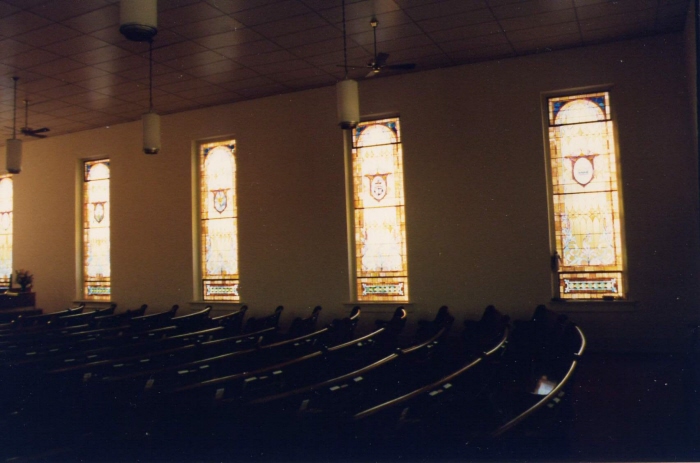
Interior shot after installation was completed. A little overexposed but was using a 35mm SLR camera. Digital makes getting the exposures right SO much easier!
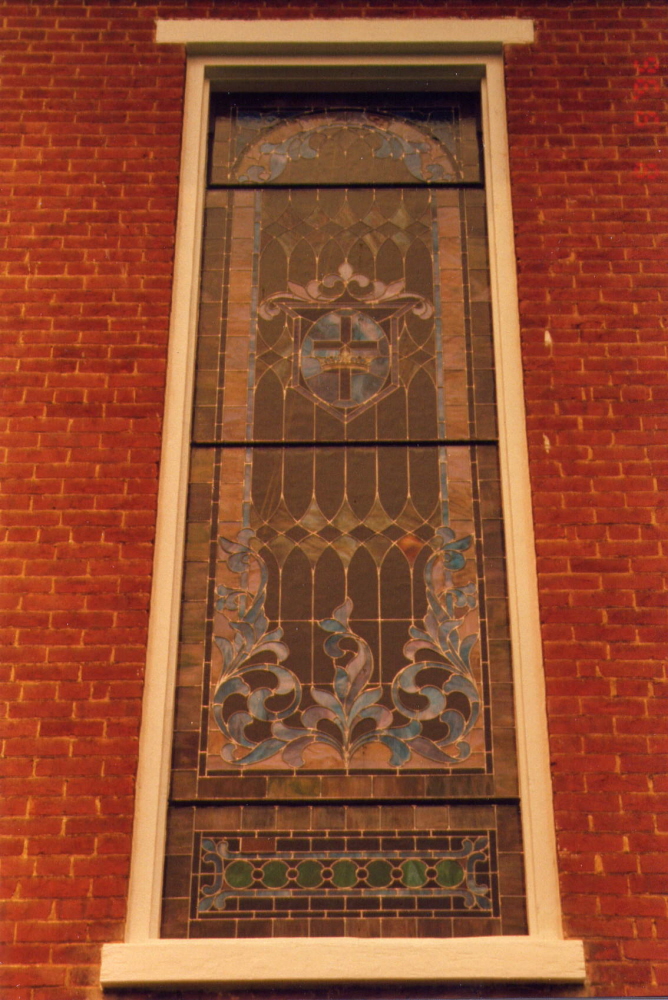
An exterior shot with a top vent and two t-bars after restoration.
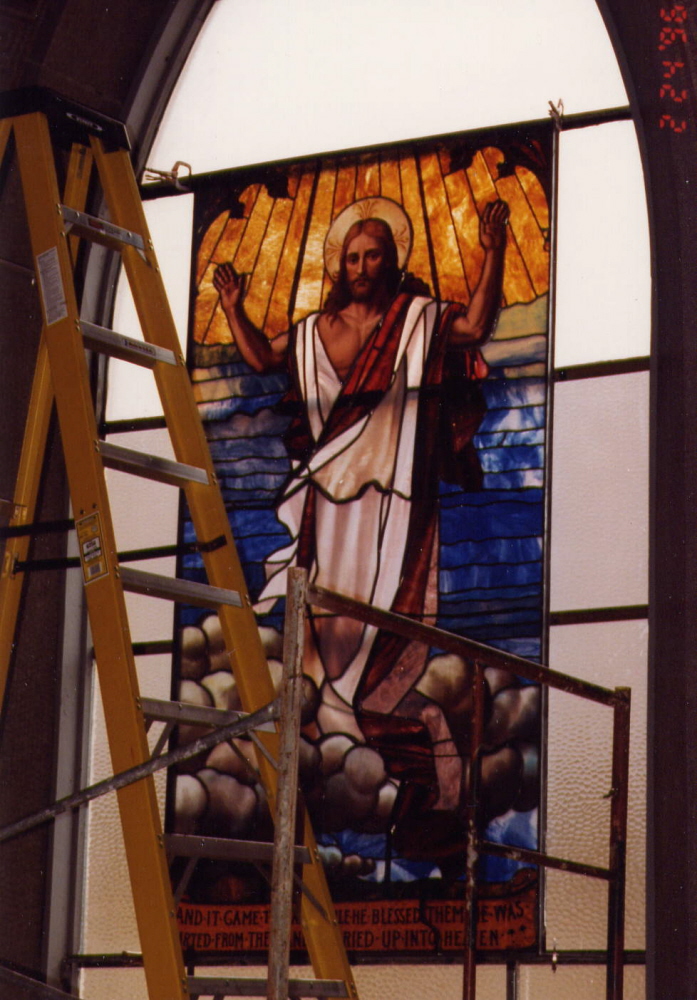
A panel I releaded in about ten hours while with Windows of Heaven. This is St. Mary's Episcopal, somewhere along Rt. 50, East of Fayetteville, Ohio. This was my first exposure to drapery glass and diffuser panels. The broken diffusers were replaced with aquatex. I could plainly see that it had different light transmission characteristics and I was a little concerned with this (at the t-bar about rib height).
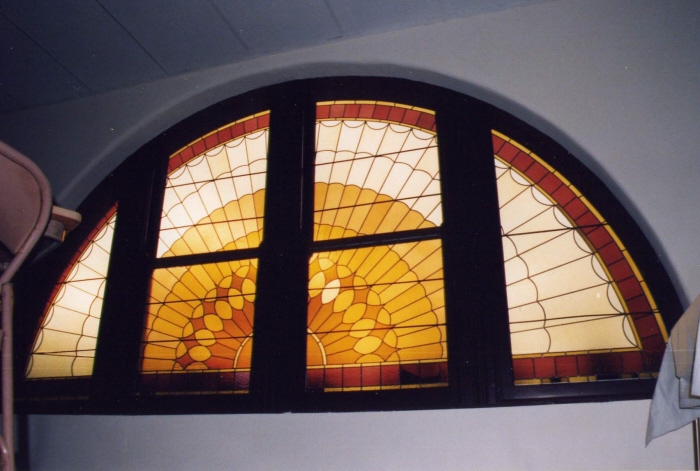
Some panels I restored for Emmanuelle Baptist in Cincinnati, Ohio while I was with Windows of Heaven. One poor color-match, there...
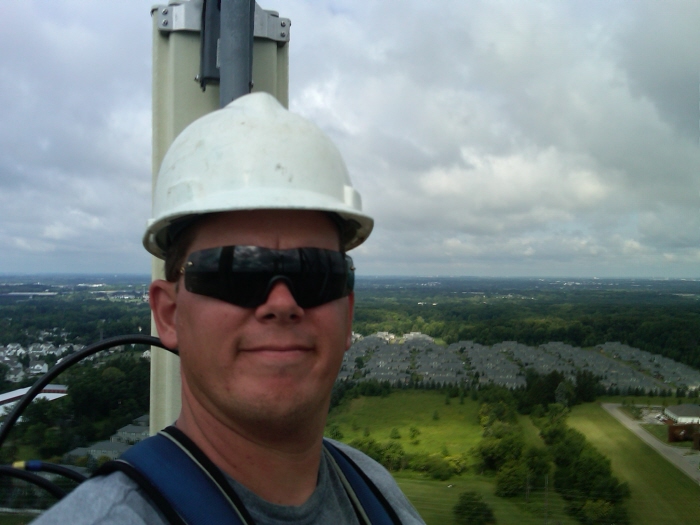
A goofy shot of me on top of 104.9 "The River" 's FM broadcast tower near Sunbury. This was while with Quality Antenna. It was my first time climbing a tower. This shot was take at about 270' from the ground. We were there to rig a temporary FM bay and them move the large , permanent FM array up another one hundred feet or so to a section of tower which had been added to the top. I helped in manuvering the FM bay around the crow's nest and with using a capstan hoist to move the temporary bay up and down from the ground.
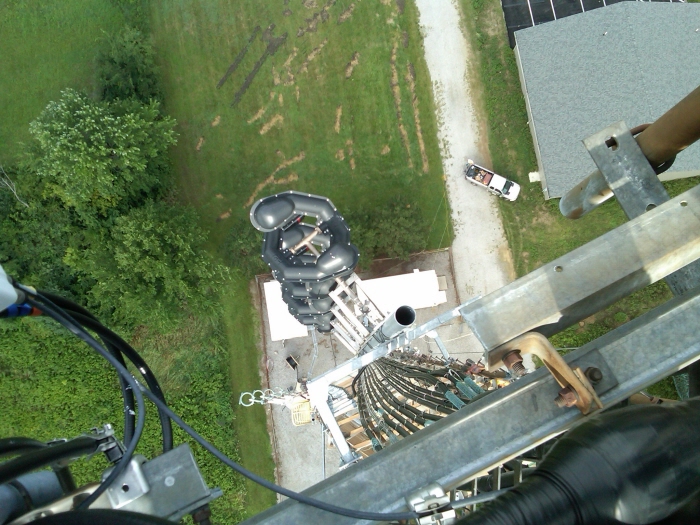
This is a view over the side of the crow's nest and the permanent FM bay we were about to move. Notice the company truck in the upper right portion of the shot, and the lines running to the capstan hoist.

This is a view over the side of the crow's nest and the permanent FM bay we were about to move. Notice the company truck in the upper right portion of the shot, and the lines running to the capstan hoist.
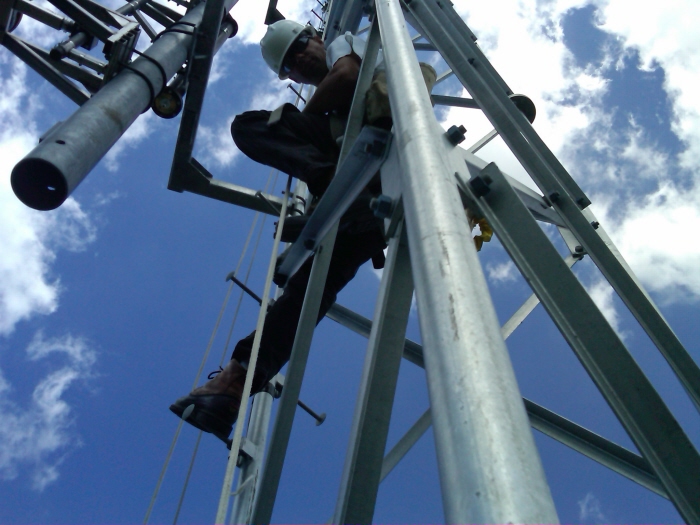
Here is a shot of "Mike" after securing the FM bay in it's new location.
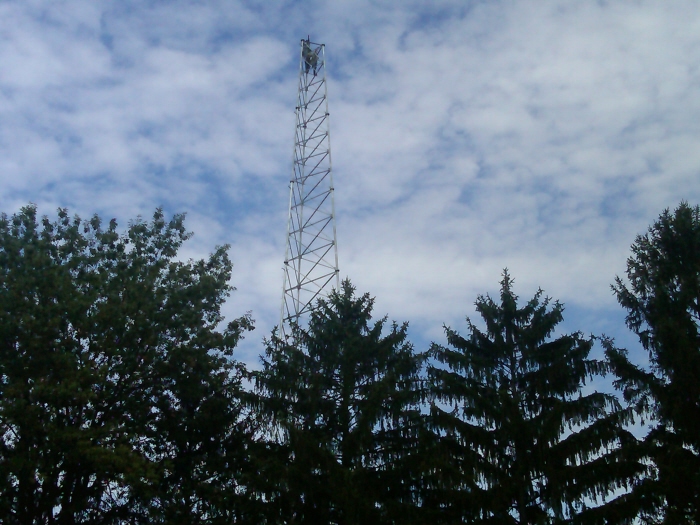
This is a shot of a remote meter-reading tower while waiting for the next section to be raised into position. This was for the Dayton Power and Light job while I was at Quality Antenna.
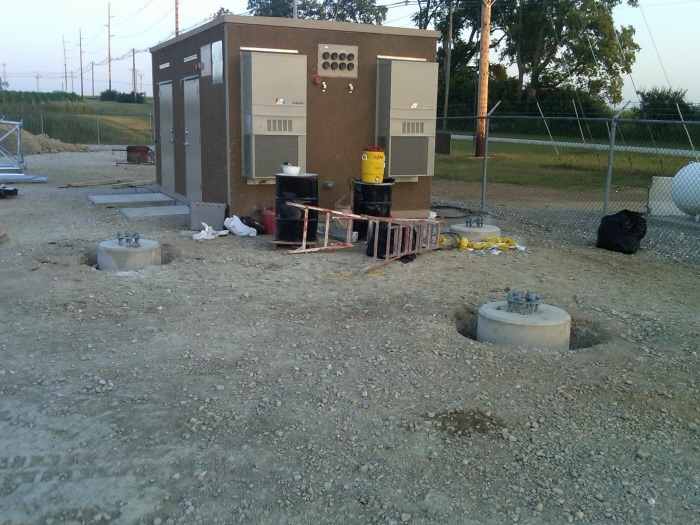
A shot of the "radio shack" on DP&L power substation property and the base of a tower to be built.
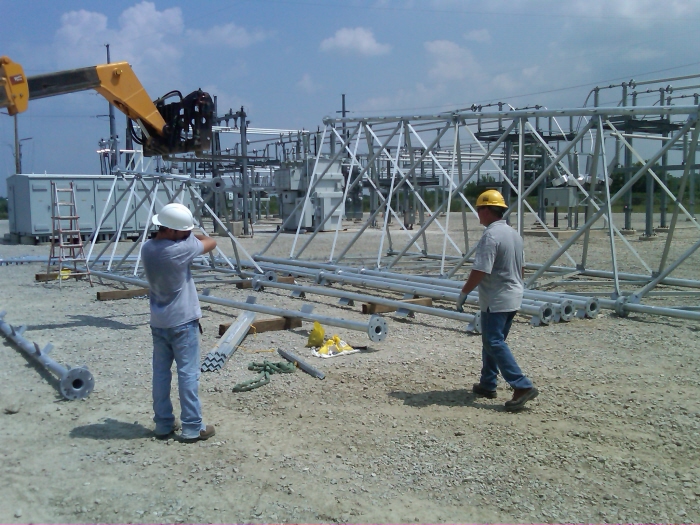
This is a shot of a couple of the guys during tower section assembly. This was a hot summer.
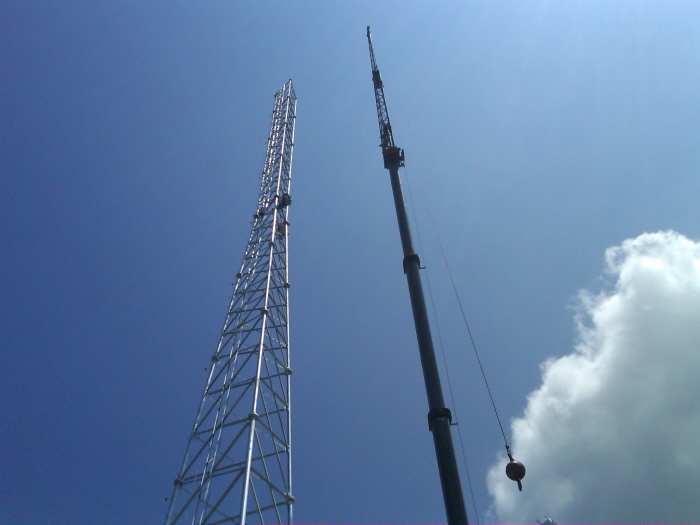
A shot of a tower section being tightened down after being lowered into place atop the transition.
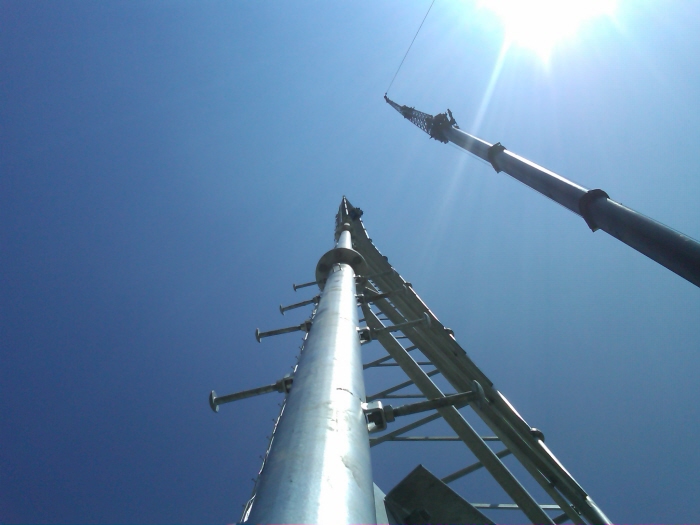
A shot of the transition between taper and straight sections of tower.
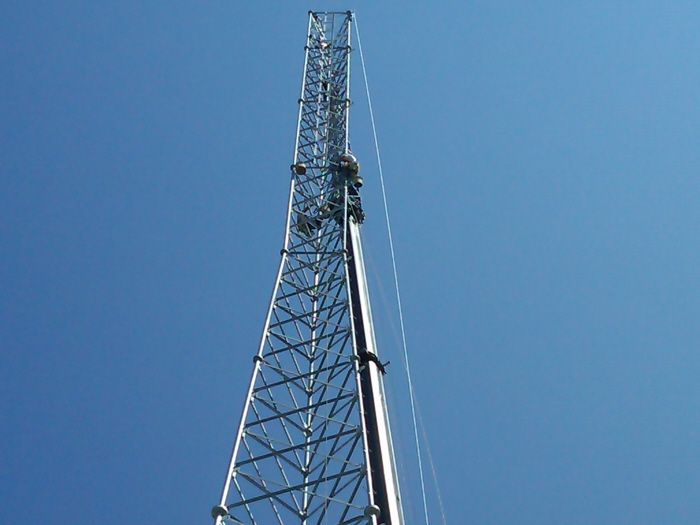
The wave-guide ladder going on.
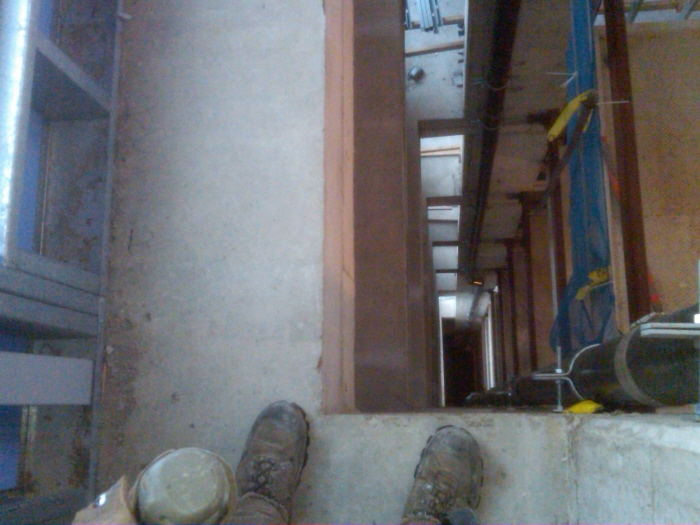
This is a shot of the 18 1/2" ledge adjacent to a stairwell shaft at the Hilton Hotel, downtown Columbus, Ohio. I worked on these ledges (this one is ten stories up)while installing back-pans (insulated panels which were installed in front of spandrel glass in "mechanical" areas) off and on for about three months while on the jobsite for Anderson Aluminum.
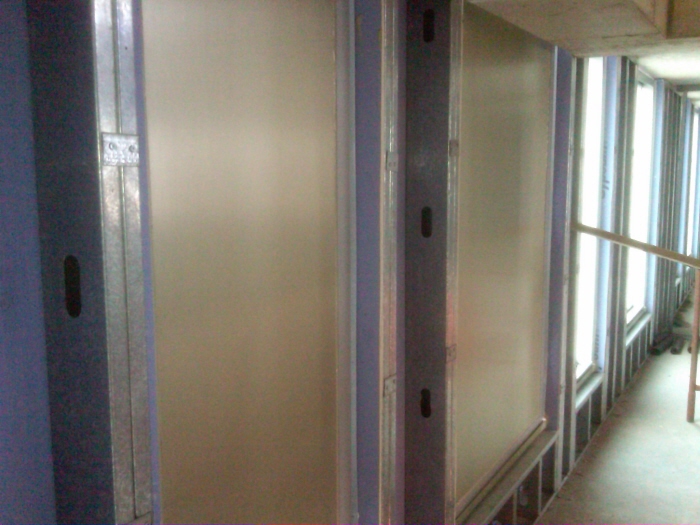
A shot of two backpans after I installed them. Note they go up and behind poured concrete. The tough ones were behind columns in the corners on the N.E. elevation.
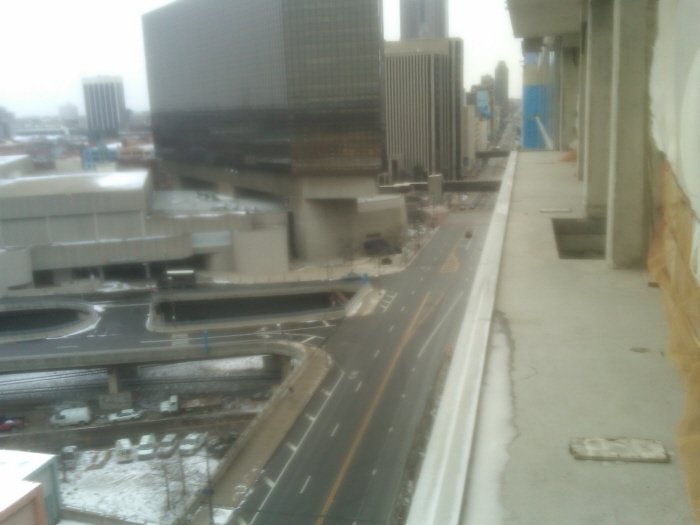
A picture of the ledge I was working on I think in January far above North High Street at the Hilton.
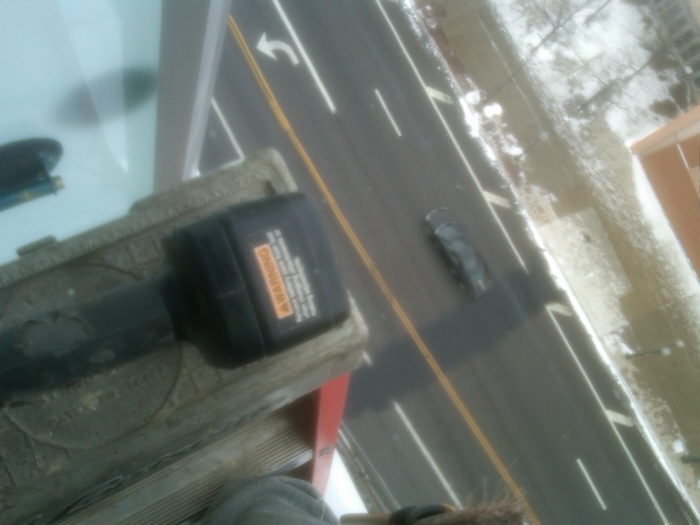
A view of North High Street, across from the Columbus Convention Center, from the top of my six foot stepladder. We were installing unitized glass in the corner.
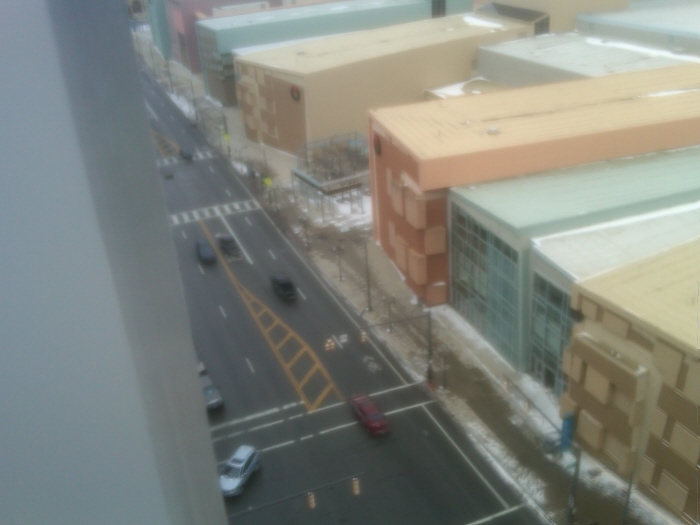
A view of North High Street, across from the Columbus Convention Center, from the top of my six foot stepladder. We were installing unitized glass in the corner.
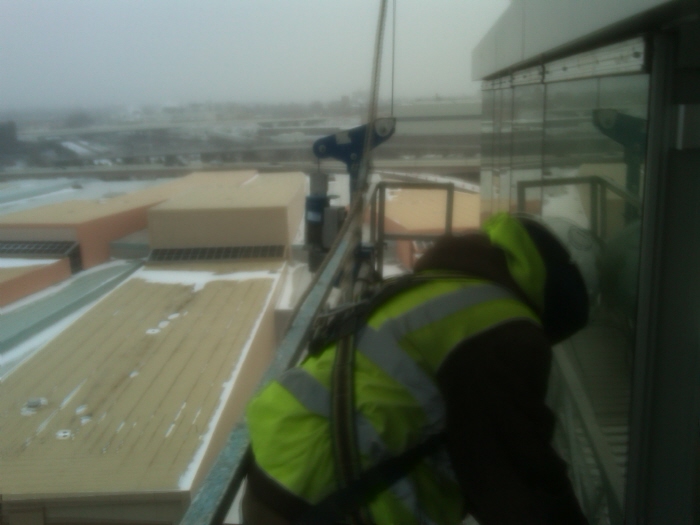
A view of the roof of the Columbus Convention center while working on a swing-stage.
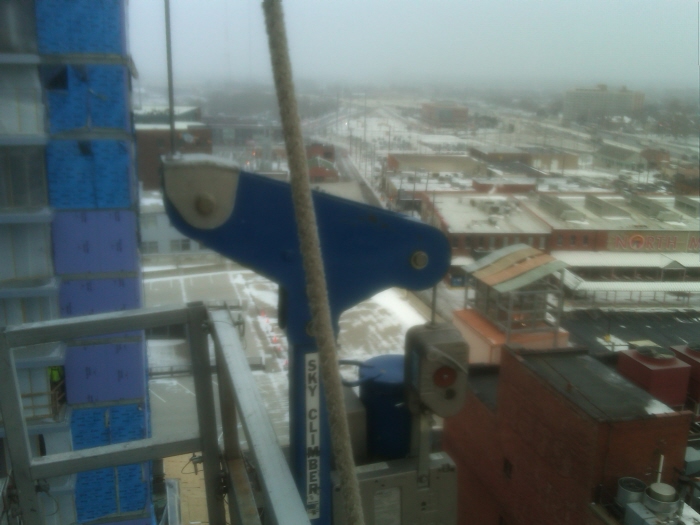
A view of Columbus facing due West from a swing-stage.
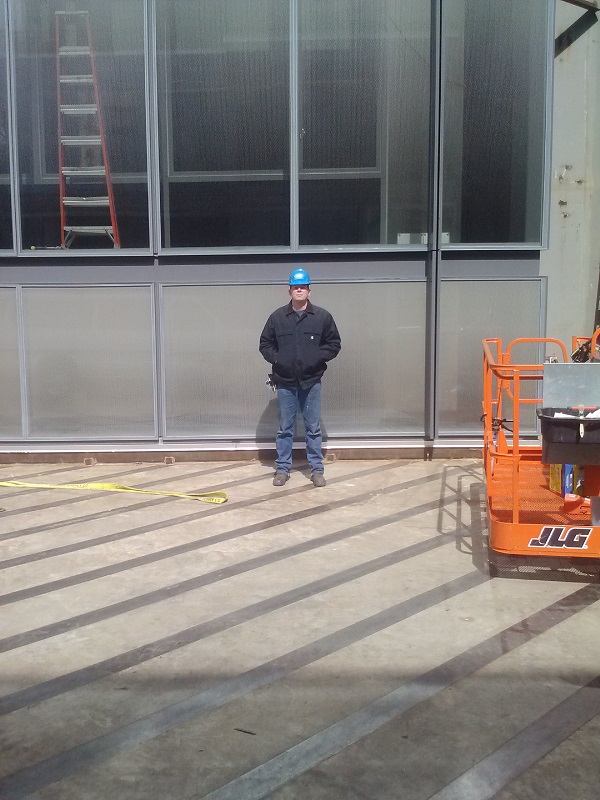
Here I am while working for NEC/PDS Micco as a Production Supervisor on site at Architectural Testing and facilitating the mock-up process for A.J. Celebreeze.
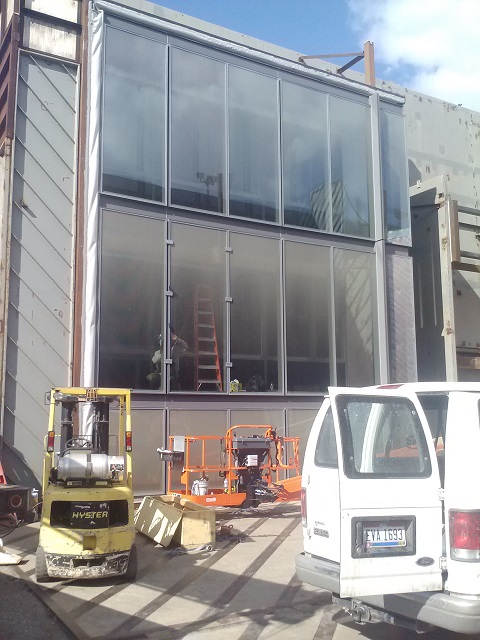
During mock-up process for A.J. Celebreeze showing typicals.
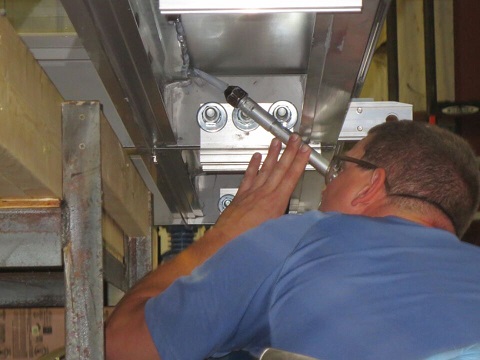
Shooting structural silicone in the C-channel area on a typical for A.J.C..
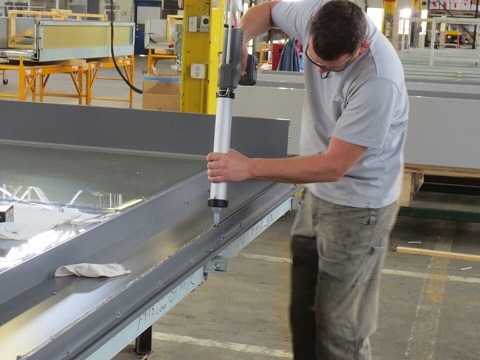
Shooting weather seals in the C-channel area on a typical for A.J.C..
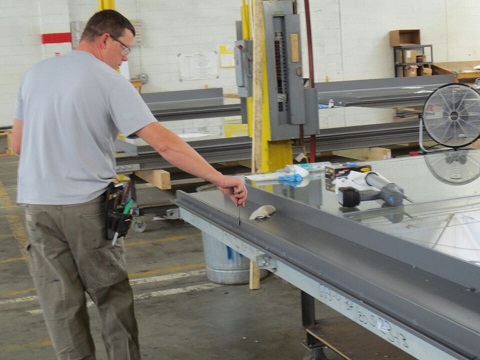
Tooling weather seals in the C-channel area on a typical for A.J.C..
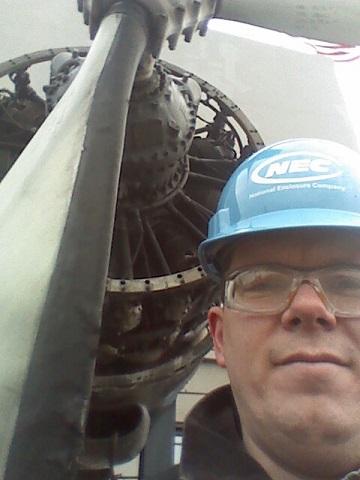
Standing in front of the "wind machine" for mock-up testing for A.J.C..
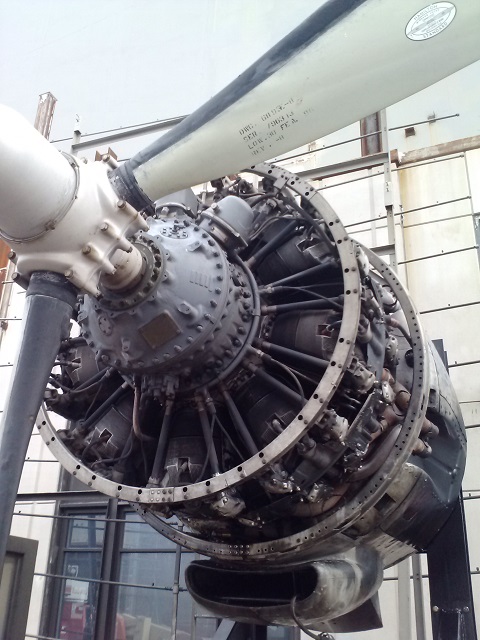
The "wind machine" for mock-up testing for A.J.C.. Note the "rain simulator" rig in the background.
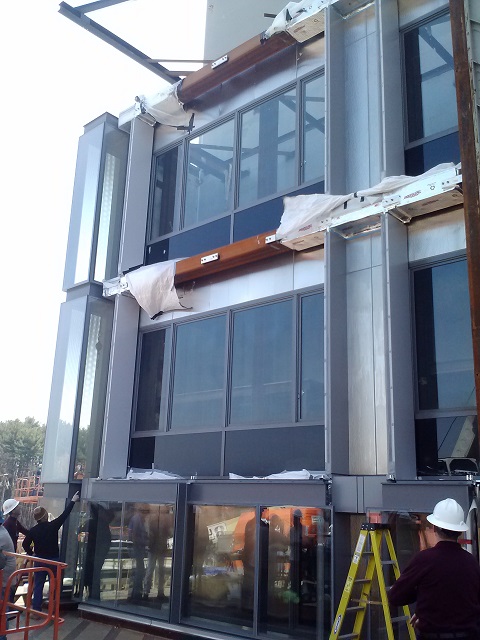
At A.J.C. mock-up. Showing hybrid corner units and inner protective glazing system (also by PDS Micco) with bare "haunches" before installation of "fly-by" units.
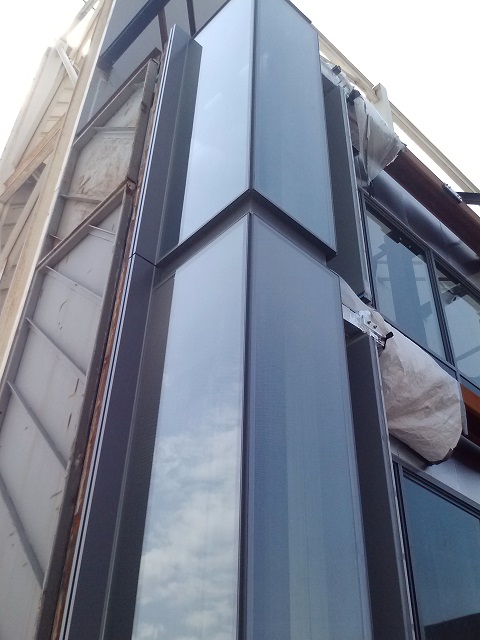
At A.J.C. mock-up. Showing hybrid corner units and inner protective glazing system (also by PDS Micco) with bare "haunches" before installation of "fly-by" units.
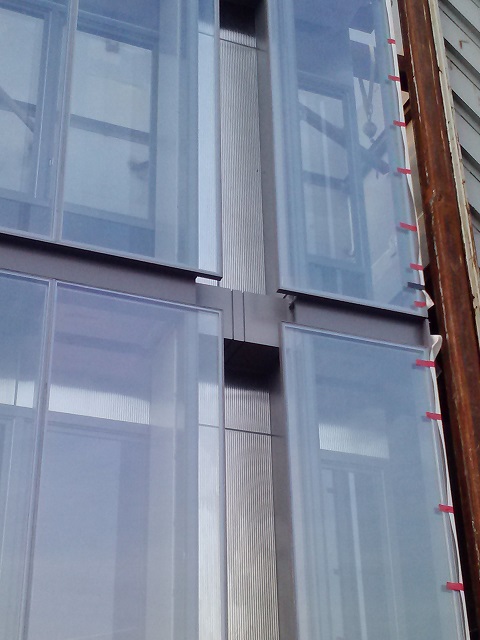
At A.J.C. mock-up. Showing "pilasters" (stainless steel u-shaped units in between glass) and after installation of "fly-by" units and haunch covers.
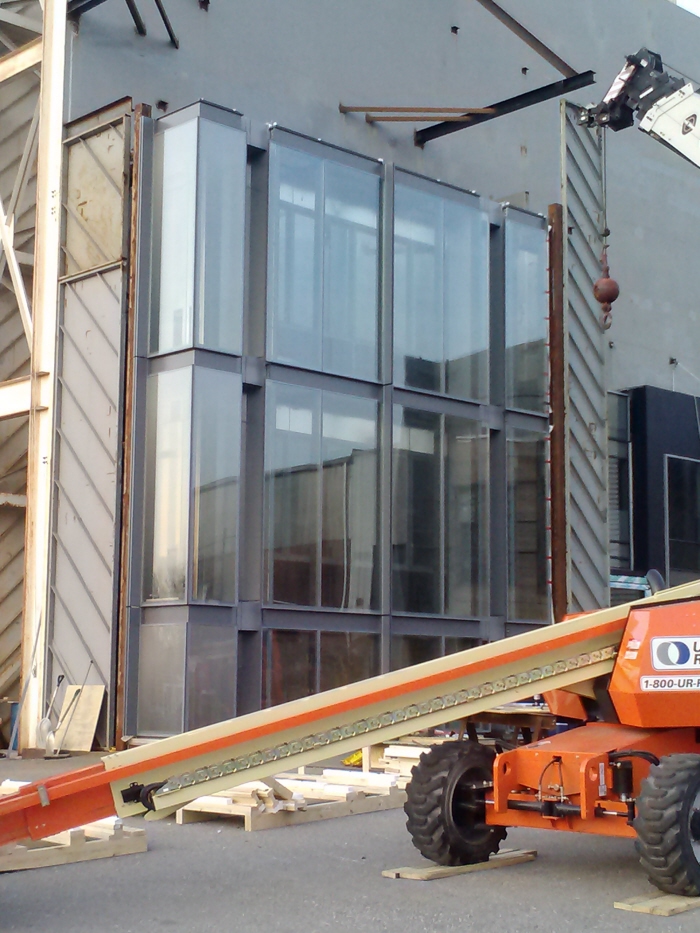
During mock-up process for A.J. Celebreeze showing hybrid corners, pilasters, haunch covers and fly-by's in place.
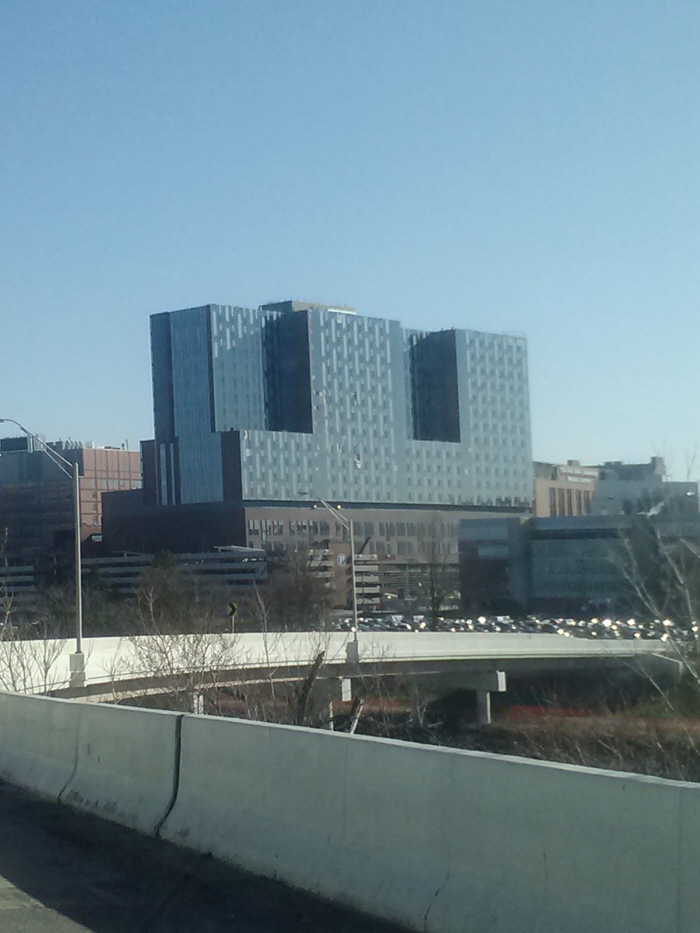
I was a Production Supervisor while at N.E.C. during the manufacture for these window and clad units. This is The Ohio State University James Cancer Hospital.
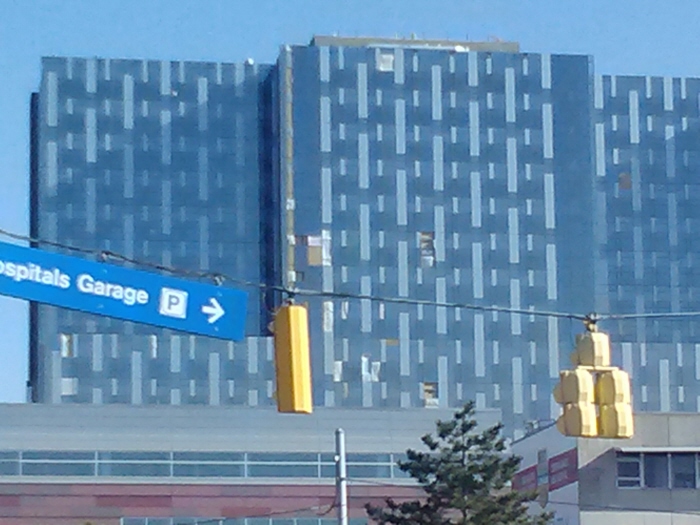
O.S.U. James Hospital detail. Punch-out yet to be completed.
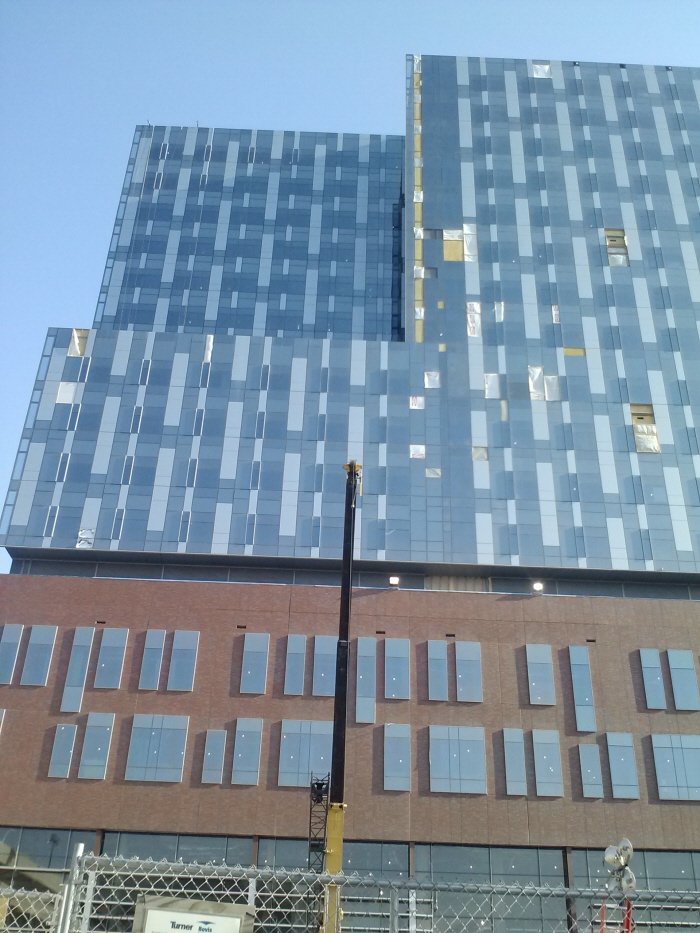
O.S.U. James Hospital detail. Punch-out yet to be completed.
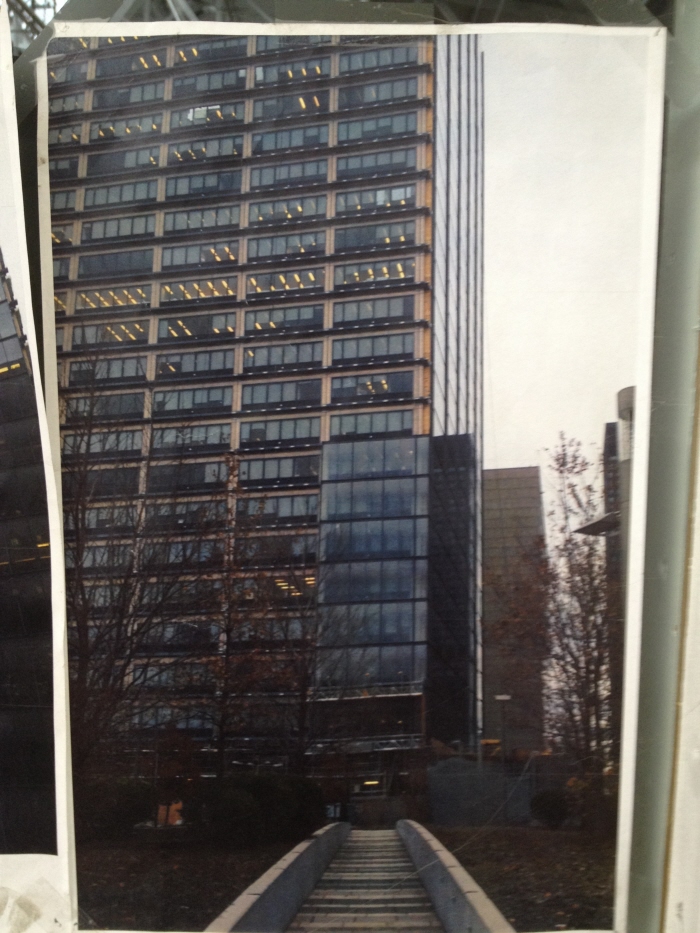
A.J. Celebreeze Federal Building Cleveland Ohio. I served as a Production Associate and Machine Maintenance Lead on the structural silicone pumping, mixing, and application equipment during this job. We had Federal inspectors in the plant daily monitoring adherance to the General Service Administration project guidelines. This is a unitized curtainwall system meaning that the glass frames are actually shipped to the job site with the glass units "glazed" in place. They are actually bonded to the frames with a two-part silicone which chemically cures effectively making one piece of the frame and glass components. This photo actually shows the inner glass façade which was installed before the old exterior glazing was removed. Two reasons: so the offices did not require relocation during the project but, combined with the outer layer of unitized glass, greatly increases the structures thermal characteristics. Some areas contained blast resistant units. Installation beginning bottom right.
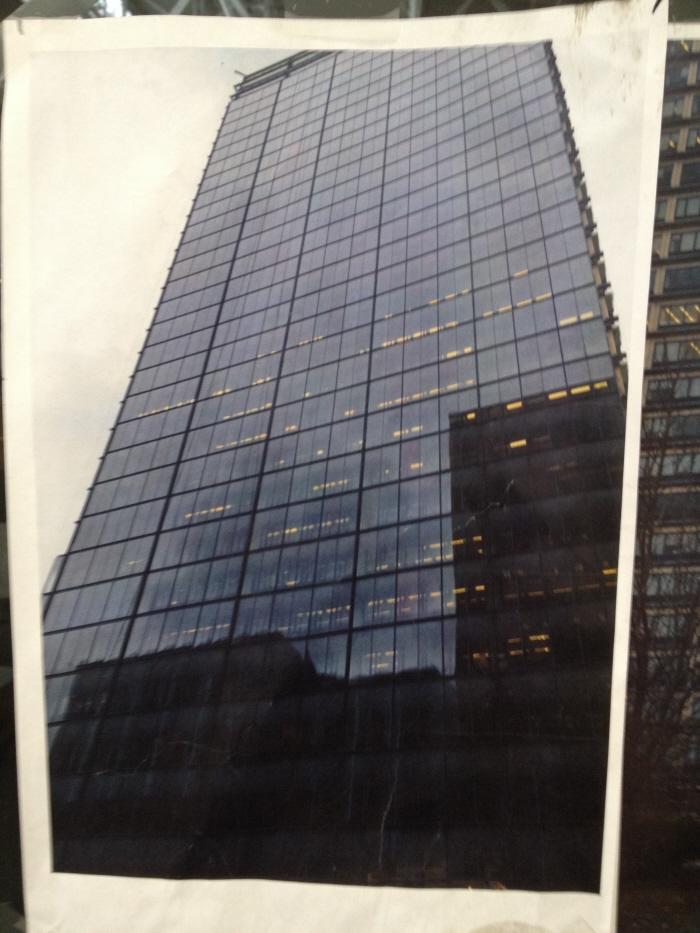
One completed side.
gLike