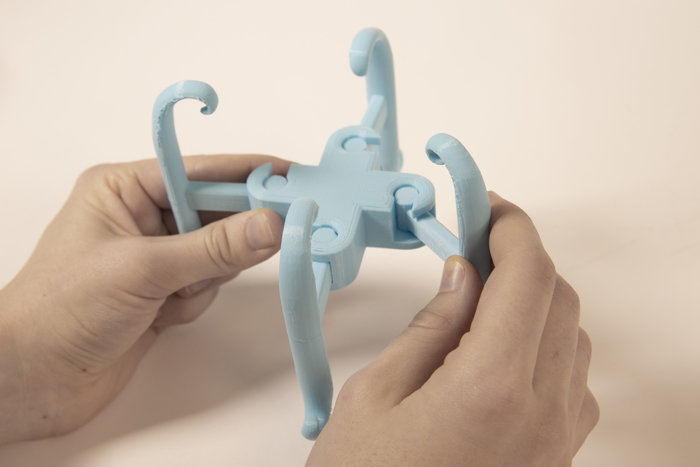
I designed the egg stand in AutoCAD so that its pieces would be able to come apart and go back together using a slide clasp mechanism.
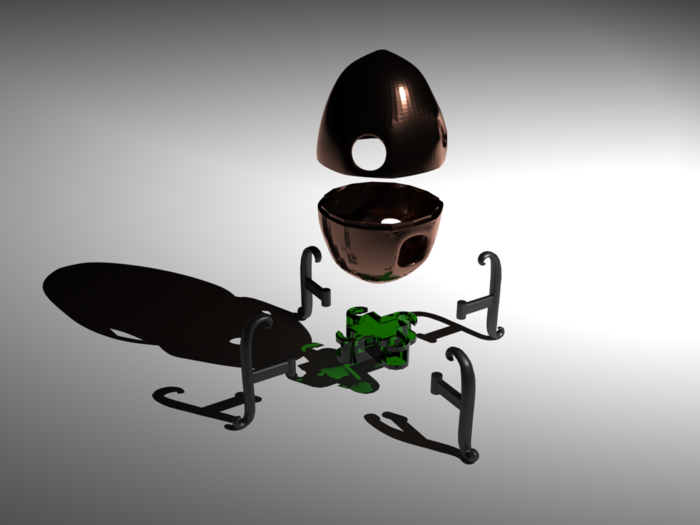
Using 3ds Max, I rendered the egg and its stand in an exploded view. I set the egg material to copper, the stand's legs to steel, and the stand 'hub' to green glass to experiment with materials and lighting effects.
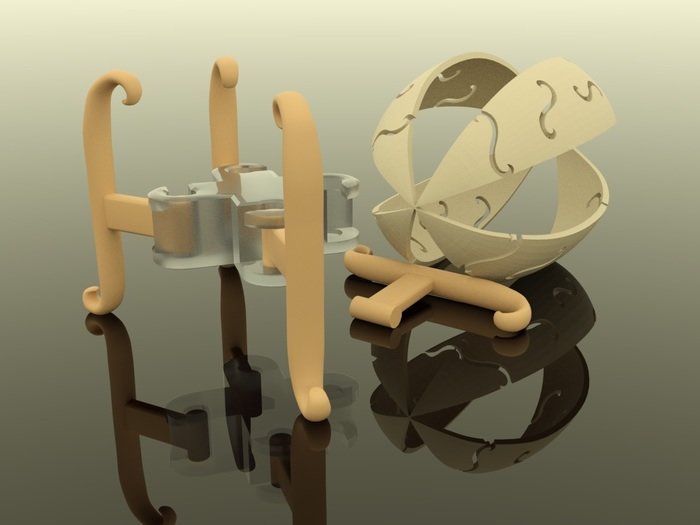
I remodeled the egg in AutoCAD to find a design that fit more cohesively with the design of the stand. In this 3ds Max render, I focused on how the egg might fall in a real-life setting, and attempted to show the mechanics of the stand. I set the egg as a tan plastic, the stand legs as a golden plastic, and the stand hub as frosted glass.
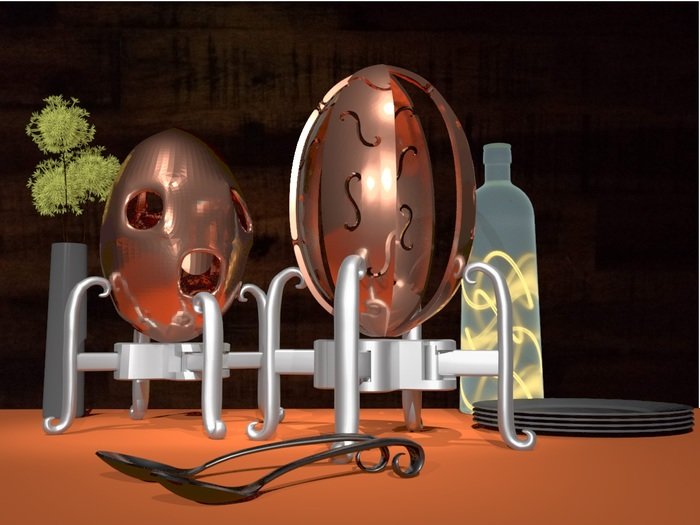
The final assignment was to put the original egg and the egg remodel in a realistic setting alongside other objects. The focus here was on varying light sources in an interior setting.
gLike