
Foam model before painting. The statue was taken outside my facility for a photo shoot and for a media event. It did get featured on the local news - for about 30 secs between the Turkey Trot and the Green Jello Diving competition stories.
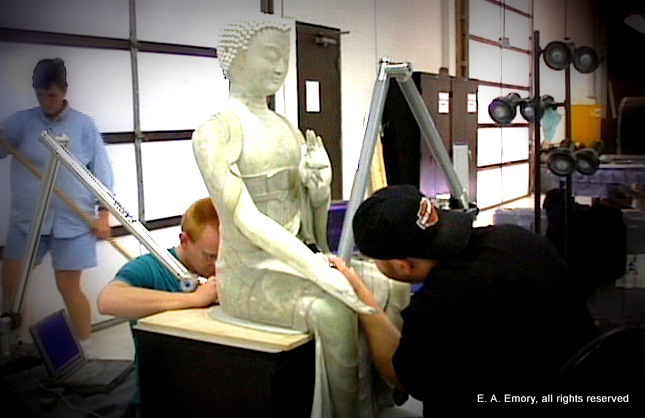
Digitizing the artists clay model.

Digitized model. Note the features that had to be added in CAD and the number of sections that had to be closed to create water tight 3D model.
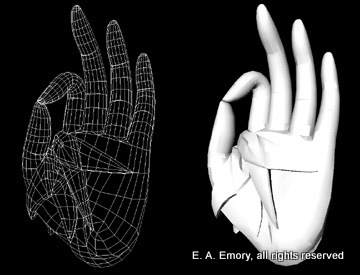
Wireframe and rendered version of statue's hand.
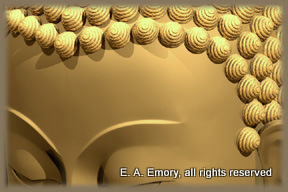
Closeup of hair curls. The hair curl was modeled separately in CAD and then exported as an STL file. This file was used to create a pattern for soft tooling. The hair curls were molded using an expandable fast cure foam.
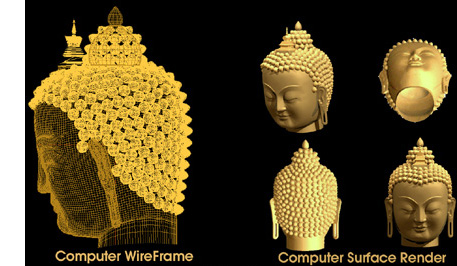
3D rendering of the finished head after merge of digitized data with CAD modeled features.
gLike