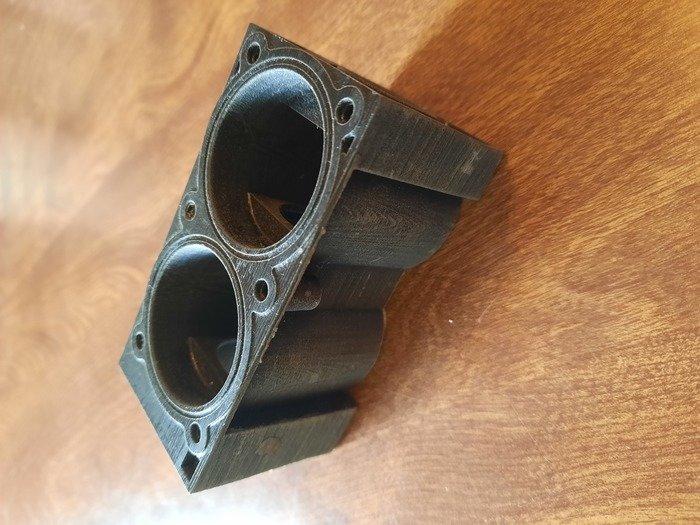
3D printed version of an early concept. Thin wall sections led me to perform a deflection study using Solidworks Simulation.
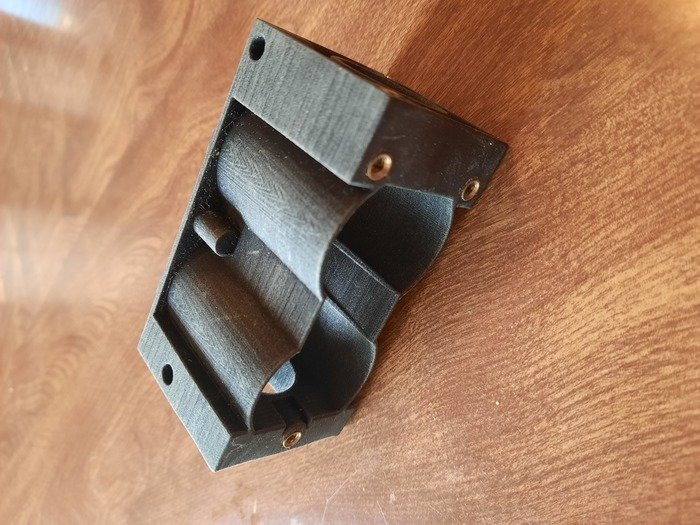
Bottom view of 3D printed prototype.
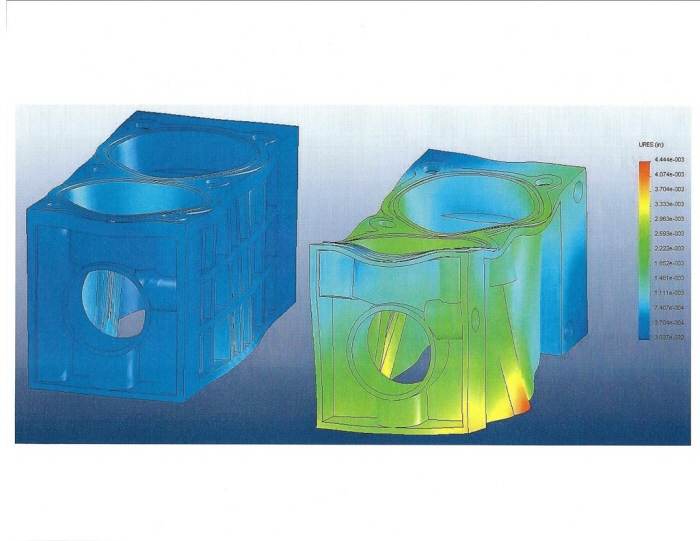
SolidWorks deflection study results.
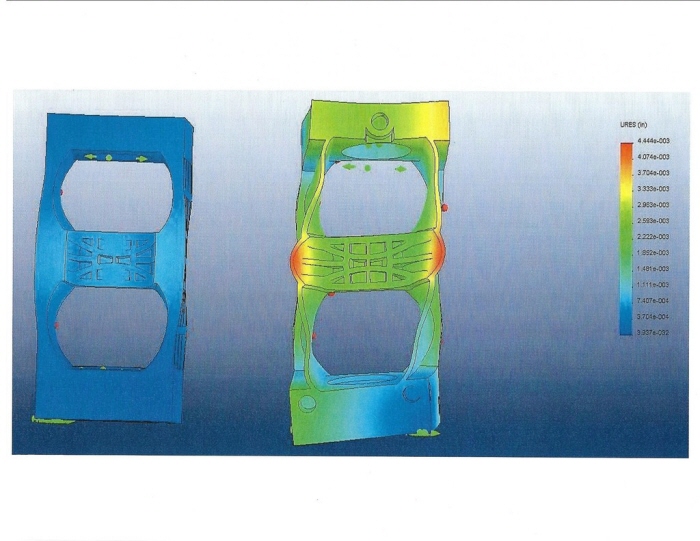
SolidWorks deflection study results.
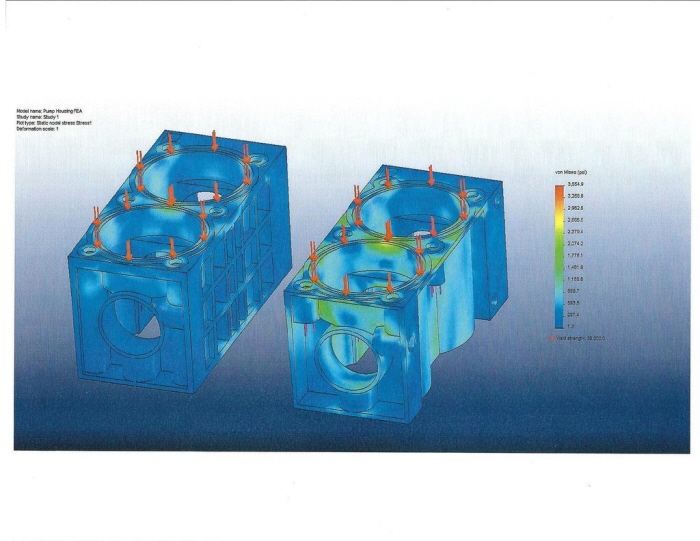
SolidWorks deflection study results.
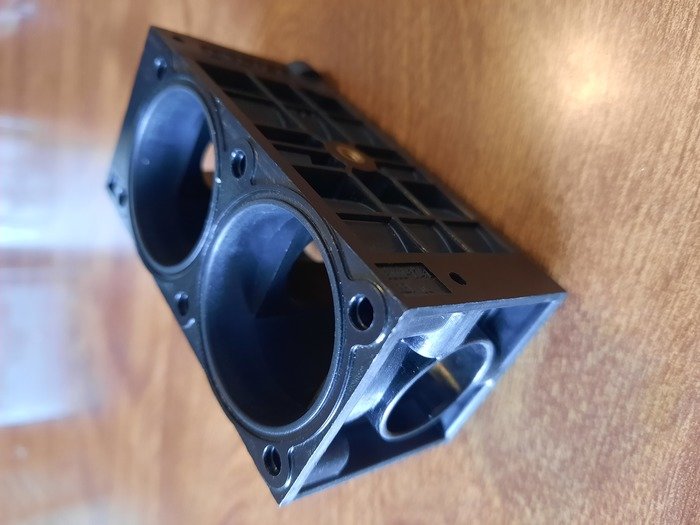
Deflection study led to design changes. Shown here is a first shot from the production mold.
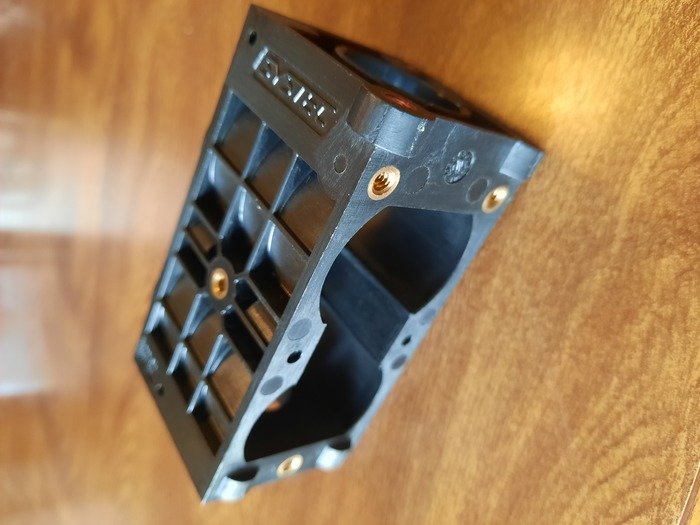
Bottom view of the first shot from the production mold.
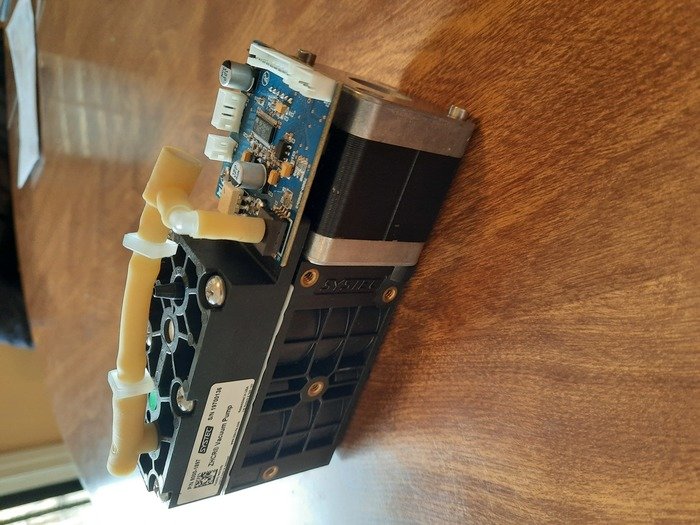
First production vacuum pump assembly ready for shipment.
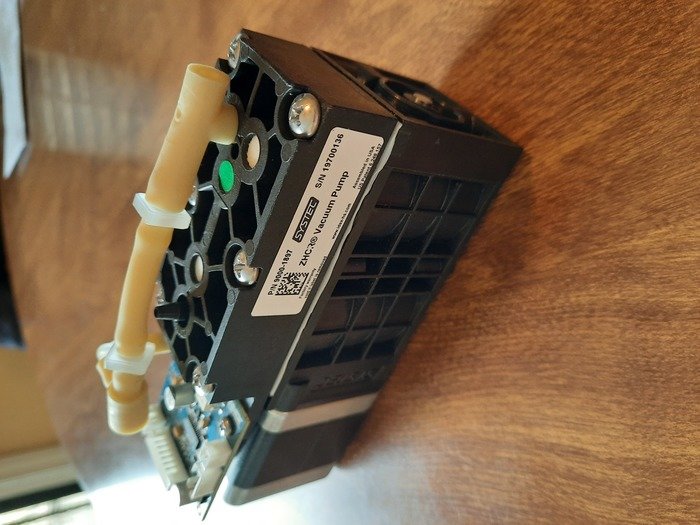
First production vacuum pump assembly ready for shipment.
gLike