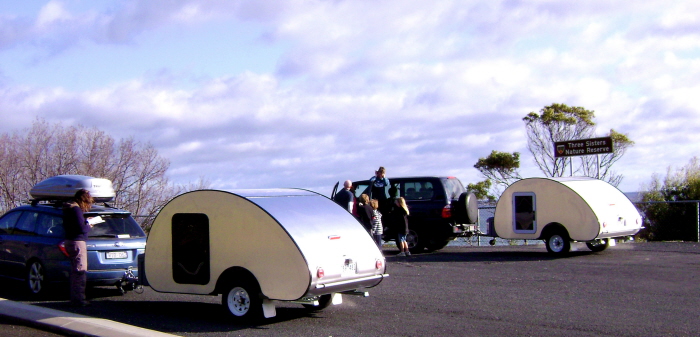
Test run around Tasmania
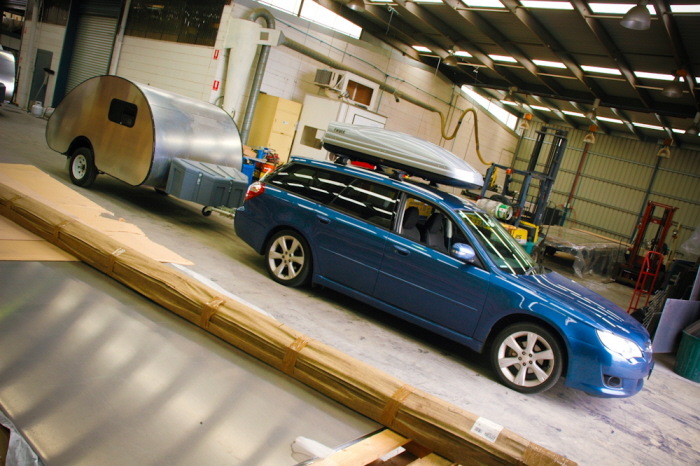
Prototype ready for first run
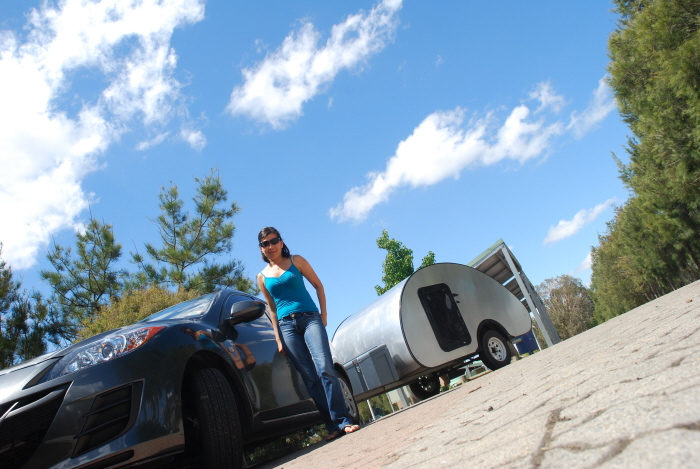
On the road to Kiama
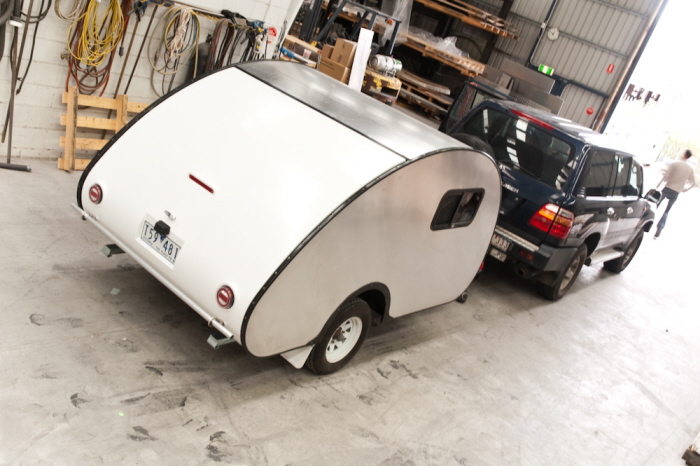
Glass tailgate fits snugly
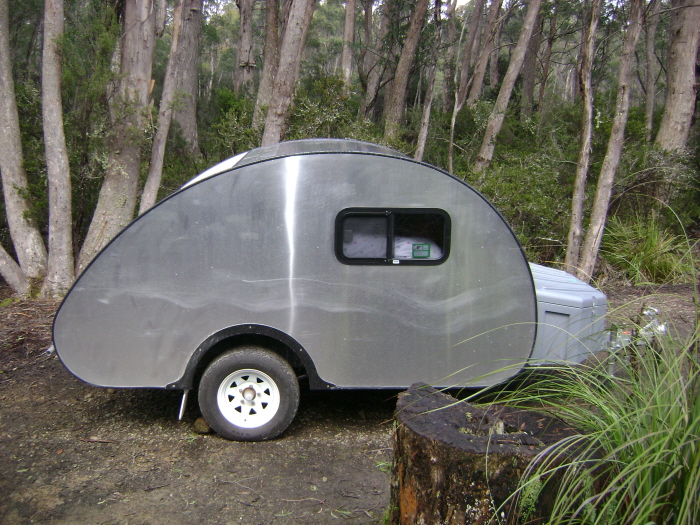
Tasmanian forest
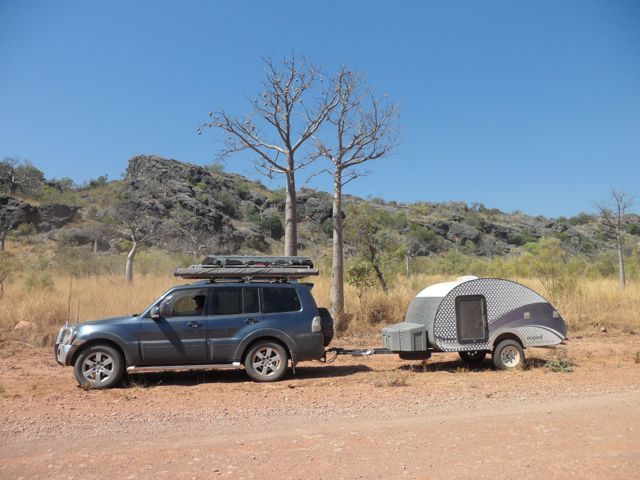
Field testing Mk2 in Western Australia. Mk2 has glass fibre sides and top, also a roof hatch and improved insulation built in to the ceiling.
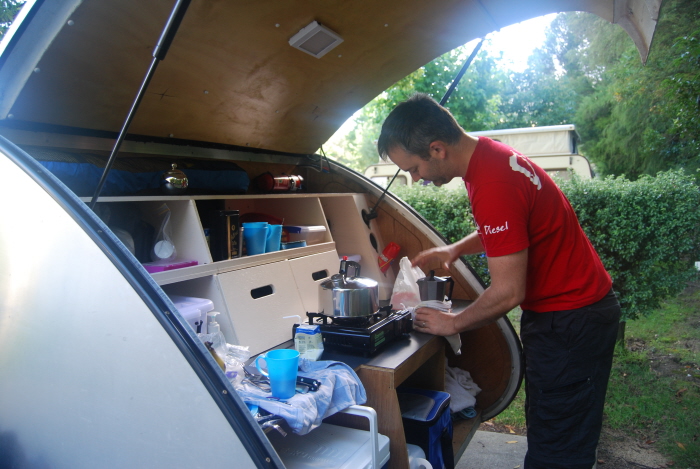
making coffee somewhere on the East coast
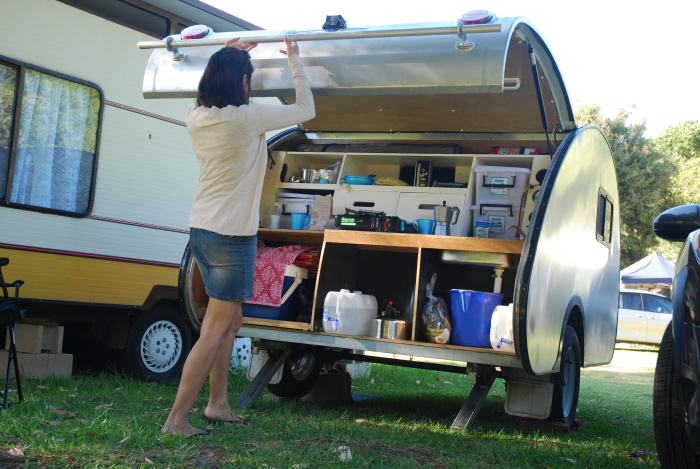
Stabilisers help even on such a small trailer
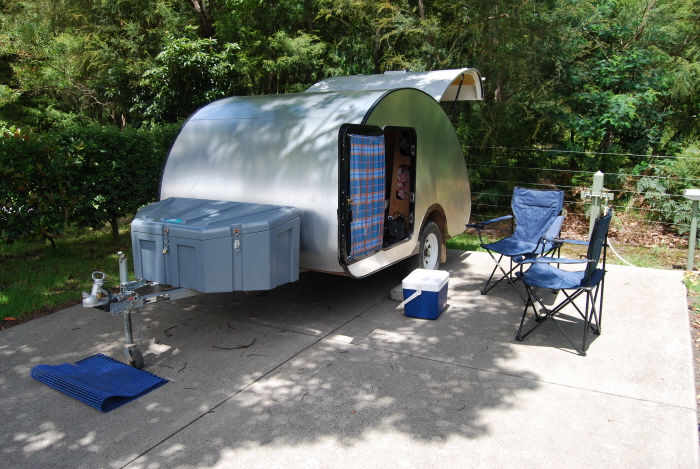
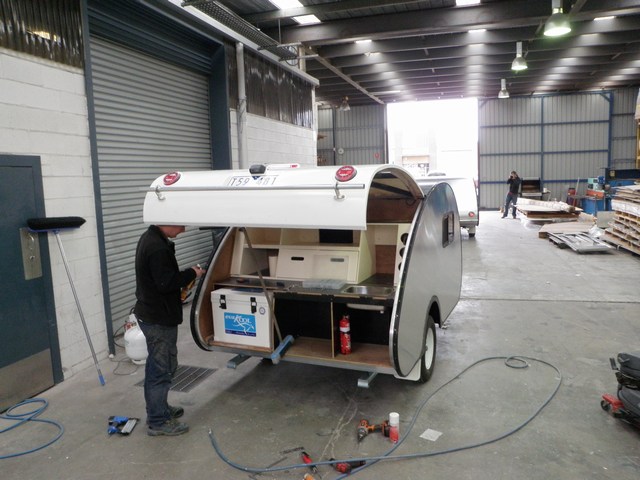
First prototype of Mk1 ready to go. Note the fridge on the left, which slides out.
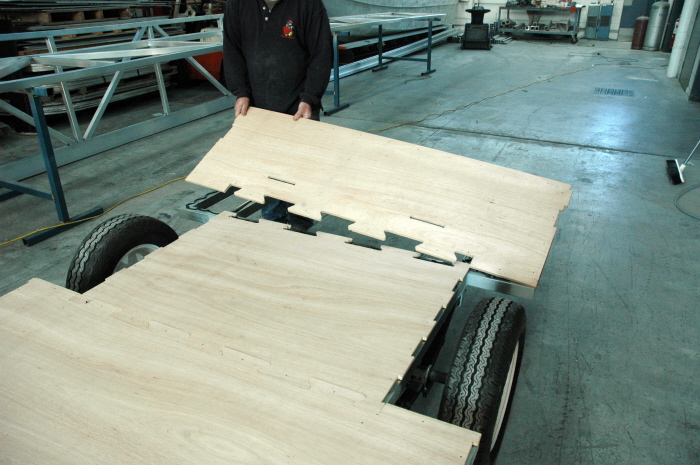
Fitting the floor to the chassis
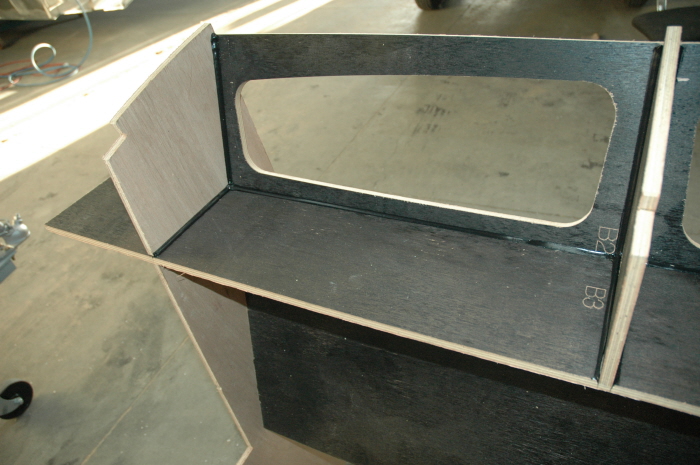
Internal storage, note marking which shows the order of assembly
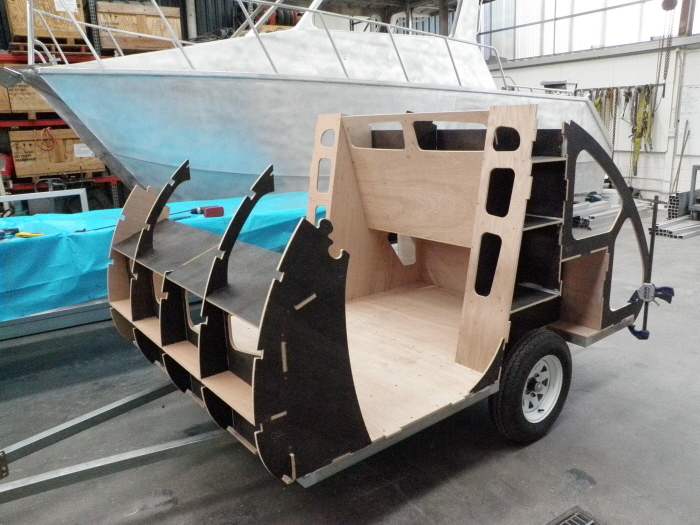
Skeleton comes together. Full build takes about 16-20 person hours. Immensely strong slot and tab joints.
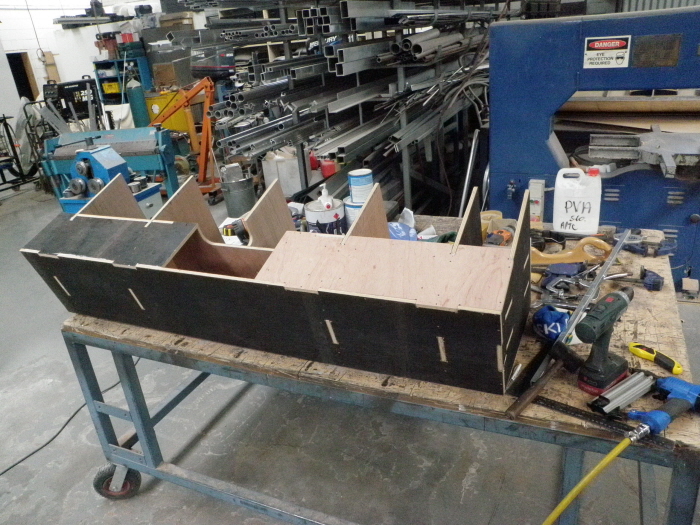
Kitchen module under construction. This can be replaced with a different module (eg. something optimised for hunting or fishing)
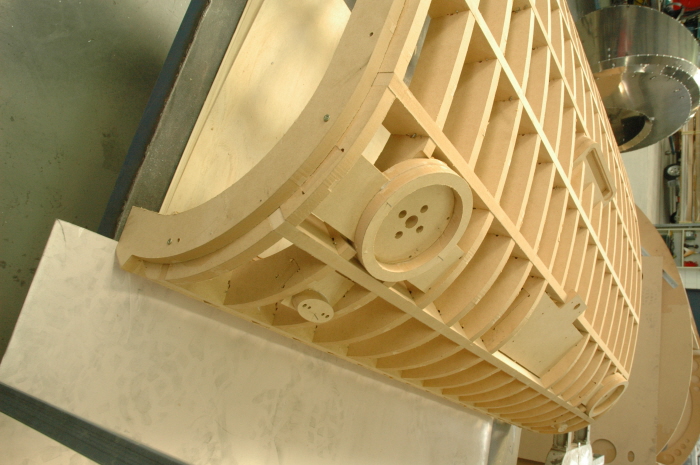
skeleton for the tailgate plug
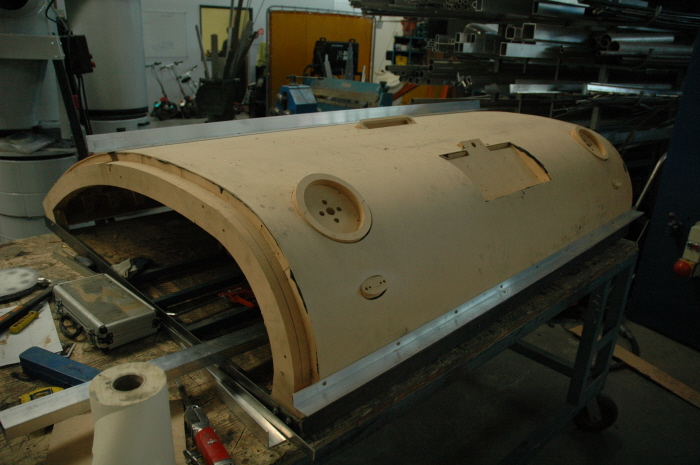
MDF skin fitted
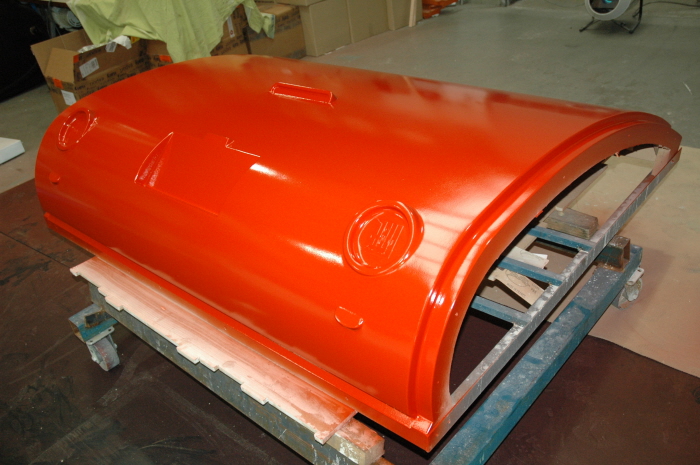
Gel coat for plug is now complete
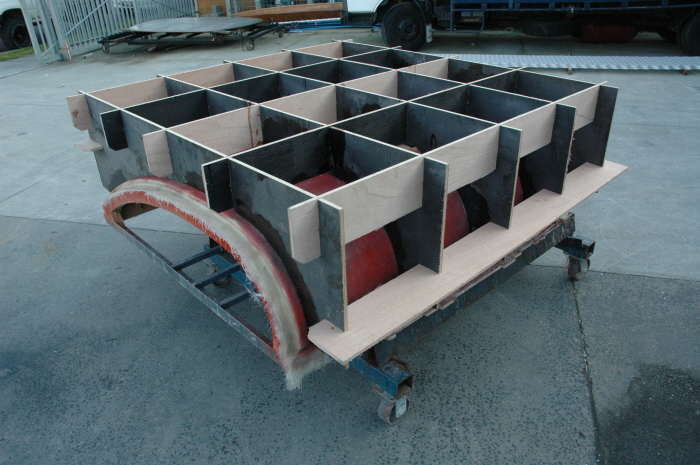
Tailgate glass fibre mould upside down
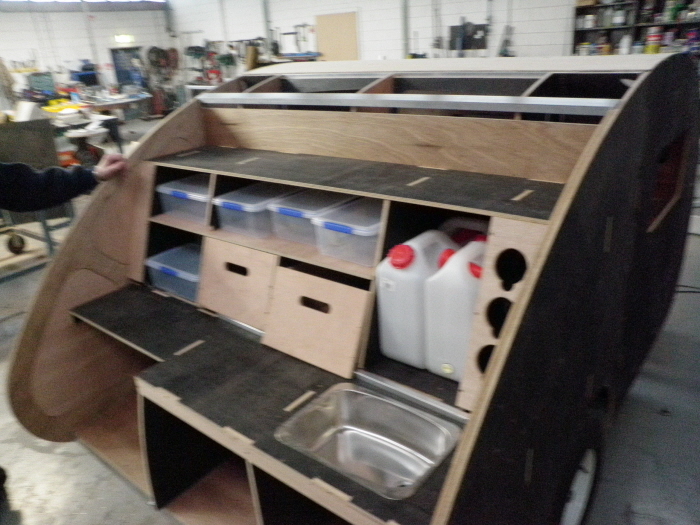
Kitchen module (its removable). Note the all important wine rack. The drawers have a rail to prevent them shaking out.
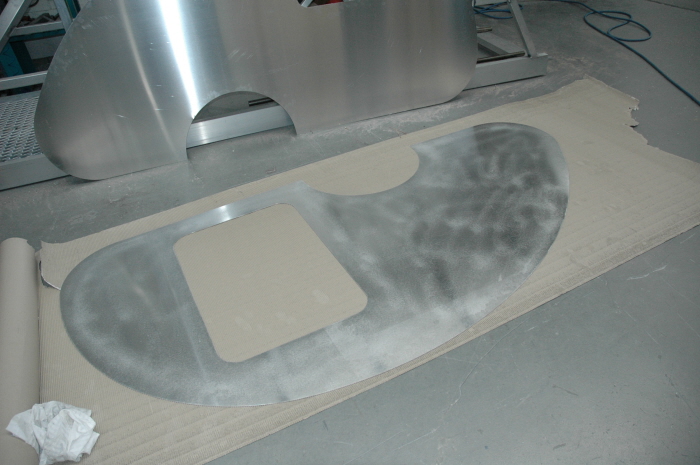
Mark 1 has aluminium side plates.
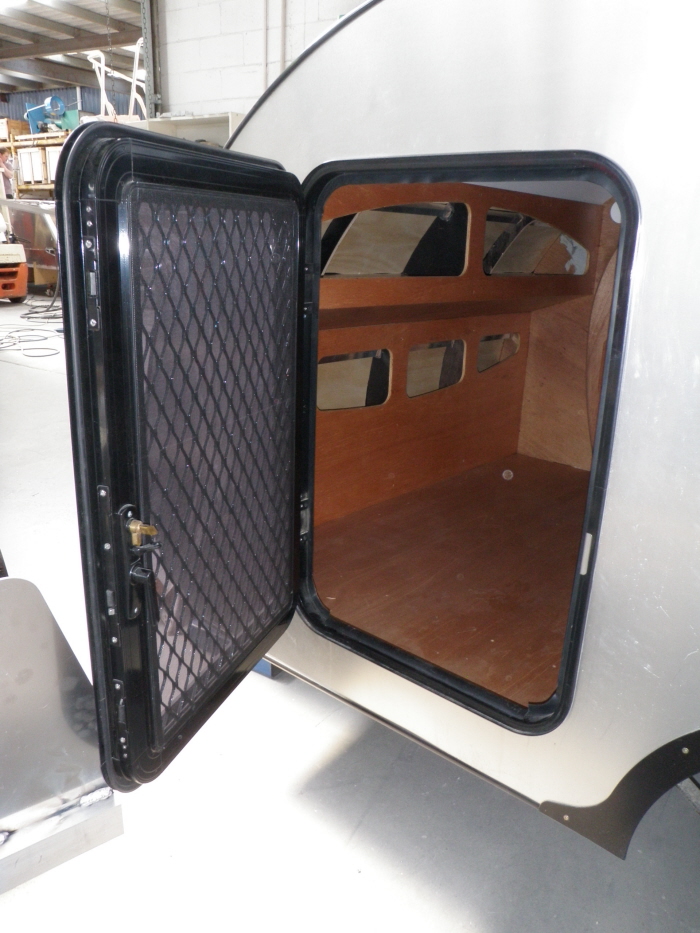
Completed internal
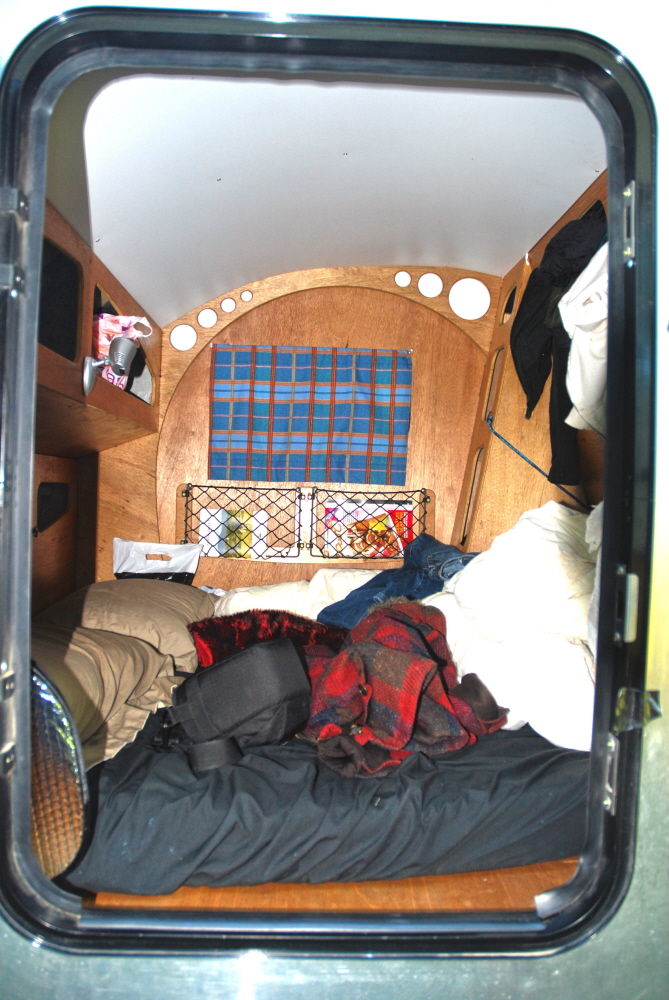
Inside view of prototype 1.
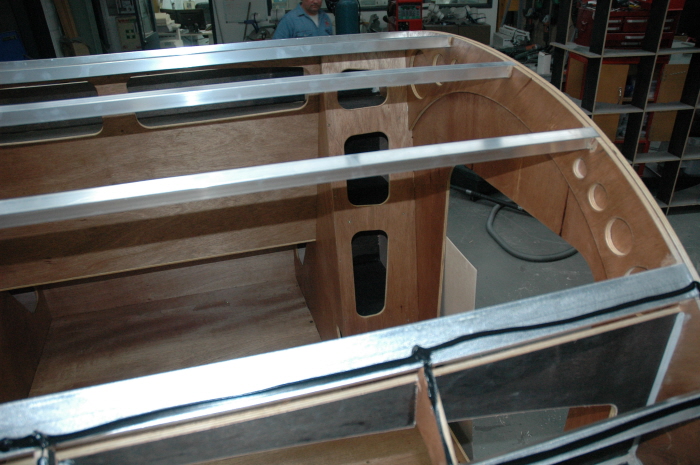
Lightweight aluminium spars hold the roof on. The ceiling is 3mm white MDF which jams into slots at front and back.
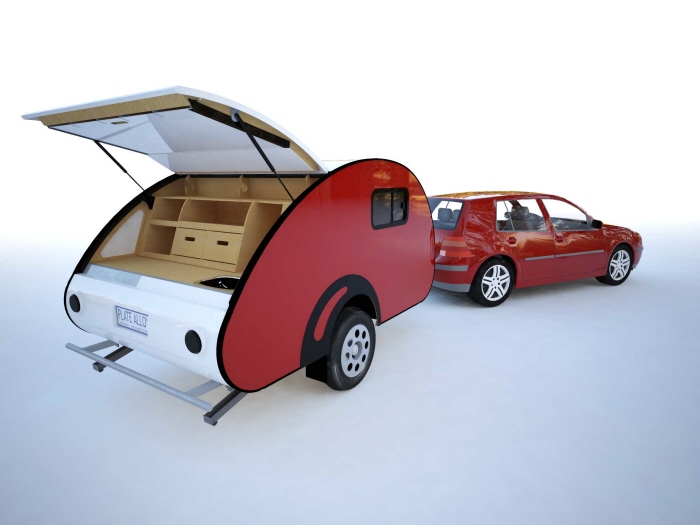
Complete 3D Rhino model of every part
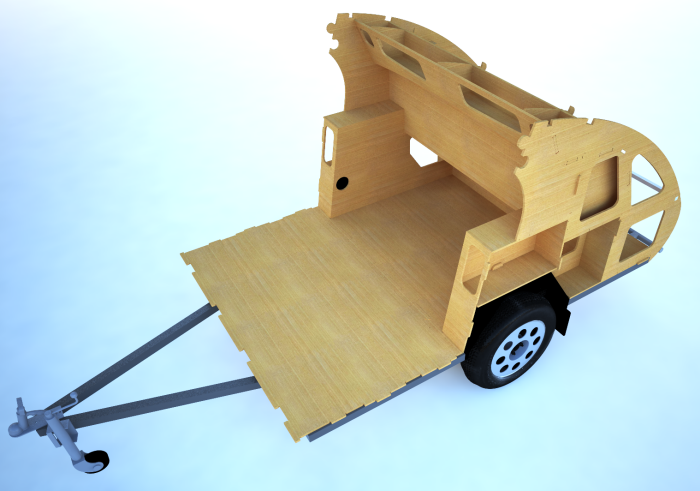
some construction detail is visible here
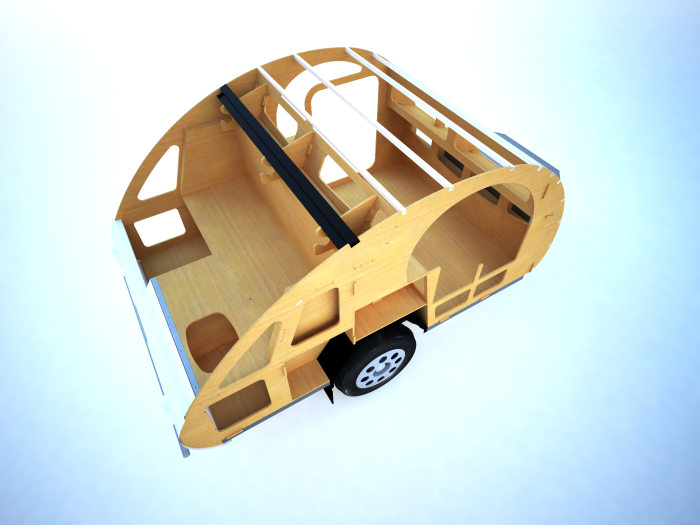
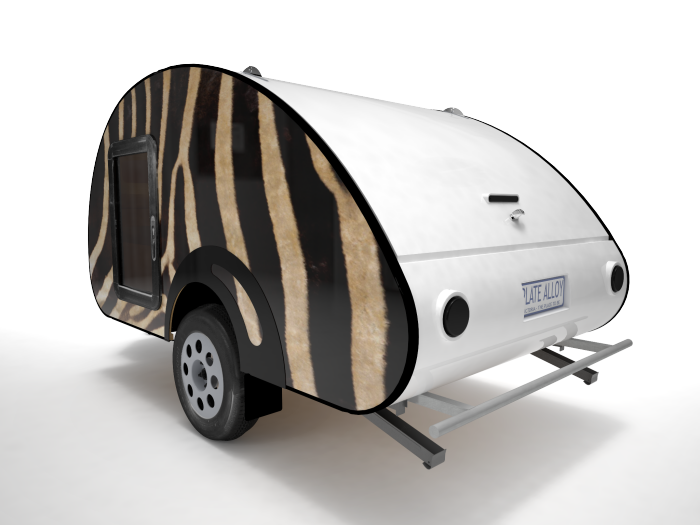
Options exist for printing vinyl decals to personalise the sides. Zebra patterns shown.
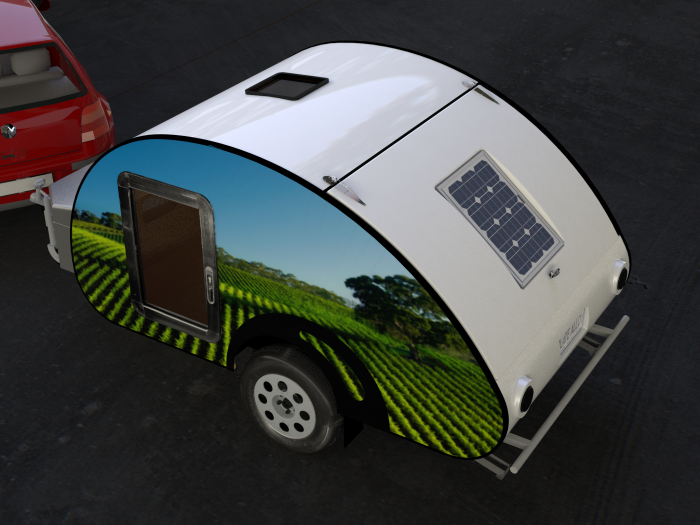
Mk4 would include a solar panel integrated into the tailgate.
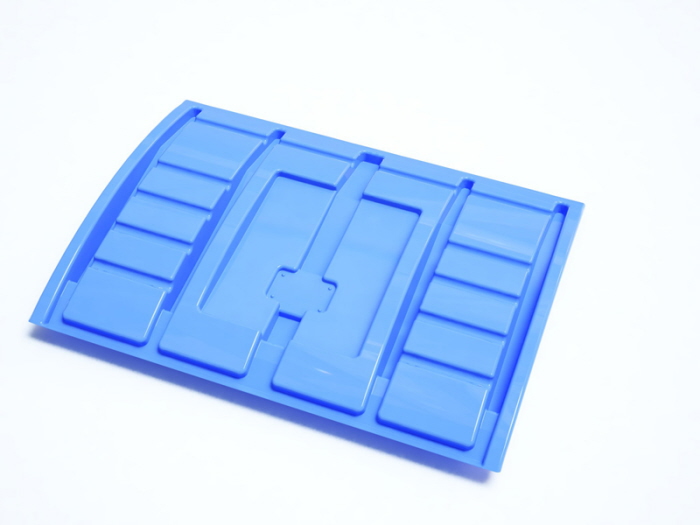
Design for future glass fibre tailgate lining. This integrates the tail lights, bar lock, hinge anchor points, solar panel mounting and stiffeners into a single part.
gLike