Talent Showcase: Clark McCune of Zebco
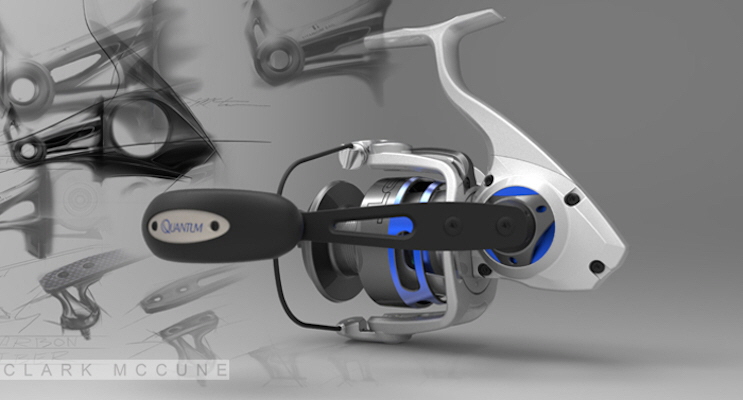
Clark McCune is an industrial designer from Tulsa, OK who has been working in the sporting goods, consumer electronics and outdoor hard goods categories for over a decade. His impressive designs pay homage to tradition and heritage while taking bold, innovative steps forward at the same time. Clark was also happy to answer my questions about what inspires his designs and how he came to work for Zebco Brands, leading designs for major accounts like Cabela's, Academy, Dick's Sporting Goods, Oakley, and more.
Looking back on your childhood, there was evidence you were headed toward a life in design, wasn't there?
Clark McCune: I read and reread the Adventures of Tom Swift series that made me want to invent and build. Growing up I designed and made a lot of my own toys out of broomsticks and scrap boards including a fort out of railroad ties in our pasture. I remember the iterations of a bow I made trying to figure out what type of tree had the best branches for tension and the many rafts that fell apart on our lake until I managed one that floated... sort of.
I loved to draw wildlife during my weekend job in high school at the city's landfill where I charged people for dumping. Besides discarded dishwashers and brush, there were flocks of geese and other waterfowl. One of those drawings placed second in the Junior Federal Duck Stamp competition. That is when I met professional artist Neal Anderson who was a great inspiration for me as a kid.
What was it that drew you away from graphic design and towards industrial design and model making?
CM: The entire process of industrial design appealed to me. A thought, or idea becoming tangible for other people to use and enjoy. Until learning about industrial design, I thought my most valuable object at the time, my bike, was the handy work of an engineer who crunched numbers and the "Giant" logo was created by a graphic designer who drew pictures. It opened up a new world.
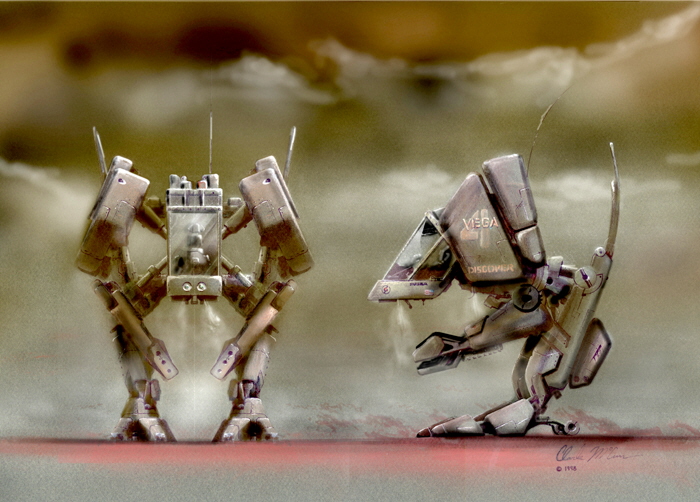
How did you get your first job at Thomson Consumer Electronics?
CM: The Director of Design Development, Mike Squillace, interviewed me while I was at The Art Institute of Seattle. I showed him a portfolio full of consumer electronic designs and models. One model was a 6 ft. replica of the Titanic I created from scratch and many, many hours of research. I never asked him why he hired me, but maybe it was my enthusiasm for craft and obsessing over details. I'm a little OCD.
What do you think of how 3D printing has evolved in recent years?
CM: It amazes me how mainstream it has become in the last five, or six years. I started using 3D printers over a decade ago in a corporate environment where not many could afford a 100K+ machine. A middle school in Tulsa now has a 3D printer. It feels like there is a surge to tinker again along with this mixture of craft and maker technology. We are in really exciting times.
How have you set up your portfolio/online presence to get noticed professionally?
CM: I basically start by putting projects online that were the most enjoyable. Probably my greatest strength is the different types of materials I work with (aluminum, nylon, titanium, carbon fiber, etc) in different outdoor categories, so I try to show this. I have a little bit of everything, but focus on the outdoor category where my passion for nature and technology kind of meet.
My Coroflot portfolio is far from perfect and even kind of rough by many standards. Any comments about how I could improve are welcome!
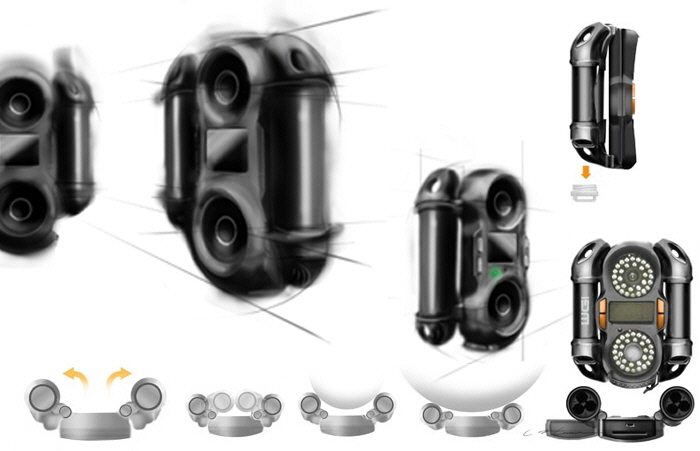
What advice can you offer up and coming designers seeking work in model making and fabrication?
CM: I think designers need a basic understanding of model making and fabrication to work through problems. Local community colleges and workshops have been a great resource for me picking up something I wasn't familiar with. One of my co-workers showed me how to lay up carbon fiber.
Being able to create a physical prototype is like a tool in your toolbox that helps you "think out loud". It's easy to get sucked into CAD and export a pretty rendering.
"I think there have been a lot of pretty pictures that sold bad ideas. Getting dirty is part of the fun."
What do you consider your most successful project/product to date?
CM: I would consider my most successful project the Zebco 33. This has been Zebco's trademark heritage product for the last 60 years. During the research I found out how many people recognized the "33" product and remembered it from their family fishing trip years ago. Many still had it in their garage from their youth and passed it down to their kids. The new design has not hit the shelves yet, but I know it is a better product in and out from the previous model. I'm happy to be part of a legacy product I know we improved and will be in someone's hand in maybe two generations... not in a landfill.
What product or project are you most personally proud of?
CM: There was a trail camera design I worked on a couple years ago that was my first consumer electronic project in a sport category I knew little about. I worked with a great global development team without ever meeting any of them face to face. The conditions were not the most ideal to work under, but hearing testimonials from very happy people using it in nature is a reward that is hard to describe. It was a successful launch and garnered an industry award.
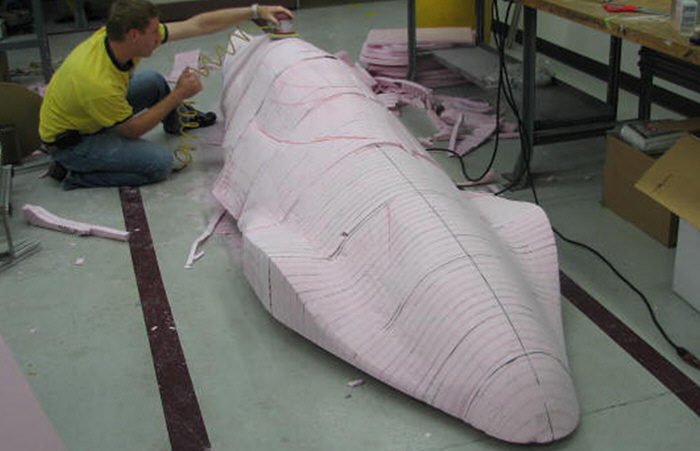
What is the strangest project you've ever worked on?
CM: I wouldn't classify it as "strange", but perhaps the most unique and enjoyable art project was stippling a salvaged 6 foot tall penguin for Myra Block Kaiser. Myra has been a great supporter of local art through a non-profit 108 Contemporary she helped start.
Do you have any routines or exercises that keep you inspired and energized to create?
CM: Jogging in the evenings really helps me burn off the stress of the day and get lost in thought. It really clears my head and allows ideas to flow more freely. That and my espresso machine I use every morning. I also love antique stores and visiting spaces where creativity is thriving, such as a cool tour of Smart Design in Barcelona, or Oakley's Bunker in California.
What has been the greatest challenge you've overcome in your career?
CM: Besides landing an interview with Coroflot?
My greatest challenge was getting a college education to launch my career. I was the first in my family to get a four-year degree. My parents supported me as much as they could, but it was mostly on me. After class I would work nights as a security guard, set up banquets at the Hilton, or sell charcoal portraits. I was in the best shape of my life biking through Seattle to my jobs after school!
Clark, thank you so much for sharing your story and sources of inspiration with everyone here at Coroflot. Check out the rest of Clark's idustrial design portfolio here and his profile too.