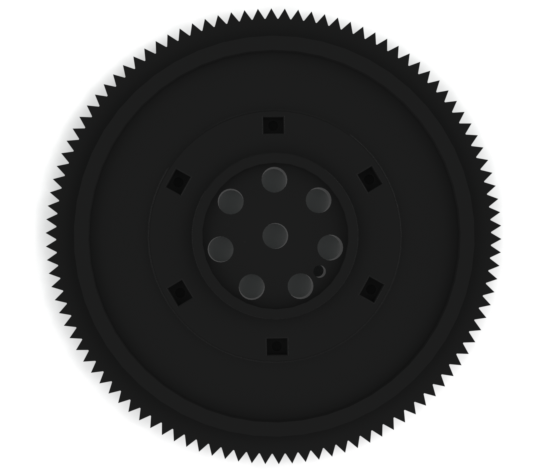
After looking at the stock Mitsubishi flywheel, we made a rendering in solidworks. The wheel weighed about 18 pounds, and after calculating the weight for the solidworks rendering, we were within 1% of the stock weight. We felt like this would be close enough to accurately simulate how forces would react with the wheel, when using finite element analysis "FEA".
The flywheel is used in a car to store kinetic energy as potential. This application causes a smoother ride, so the engine isn't felt as much. We chose the car we did because it is a popular choice for people taking it from stock, to racing it on a track. This 18lb flywheel seemed to be standard for average cars. Luxury cars tend to use a heavier flywheel in order for a smoother ride. Most are made out of cast iron due to the high density.
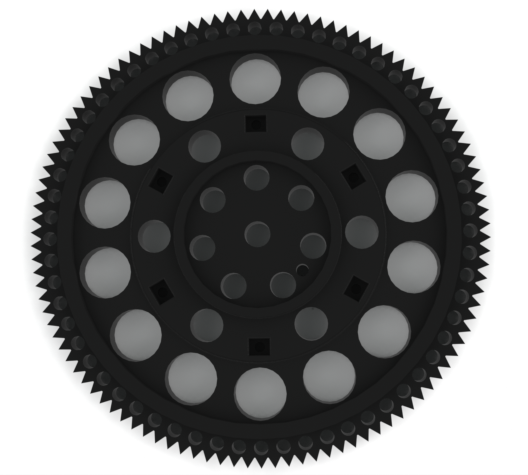
This solidworks rendering is what I nicknamed the "Swiss-Cheese Flywheel." We took out as much space as we could in the form of circles to reduce the weight. We chose circles instead of other objects to minimize the stress concentrations. The results were not as we hoped, there was minimal weight loss, only around six pounds. Our goal was to have a wheel around six pounds, and this one came in at about twelve. Not to mention the FEA for this flywheel had a factor of safety well below one.
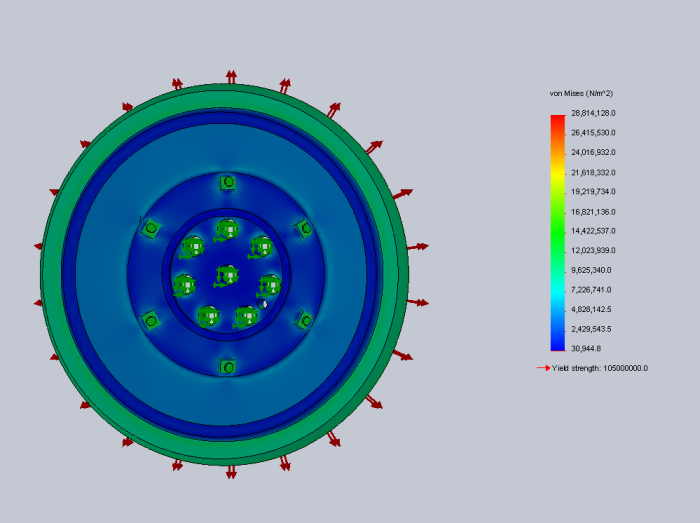
This is a rendering from solidworks showing the FEA on the flywheel. After some calculations, we confirmed that the factor of safety for the wheel was about 3.6. Due to the six large holes, and the one smaller hole, there is a minor stress concentration that was not considered via hand calculations, but the FEA determined that it would not be a major consideration.
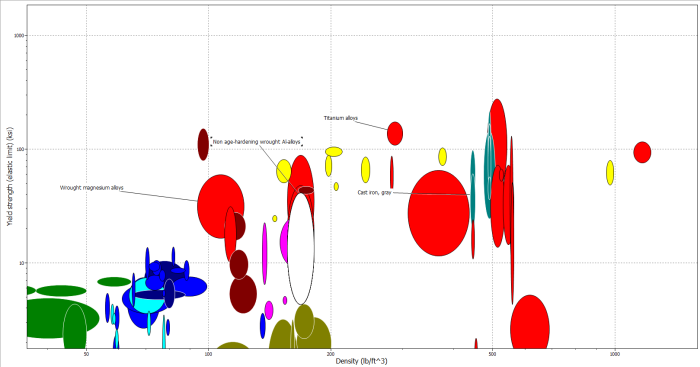
This chart shows what materials we were looking for. This is a strength vs density chart, we were left with looking at aluminum and magnesium for material choices. We decided to use aluminum, since magnesium burns up over about 500 degrees. The aluminum wheel worked as shown in the previous picture.
gLike