
Here is the final product
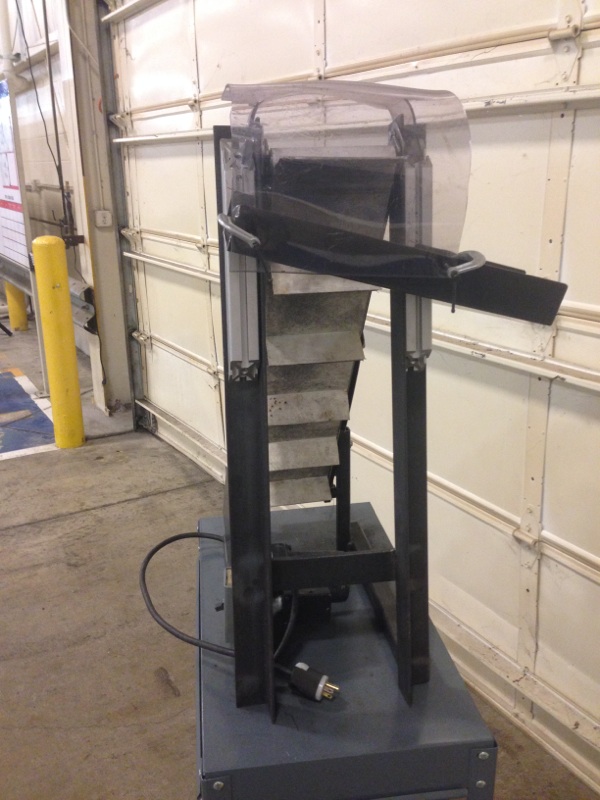
Another picture of the final product
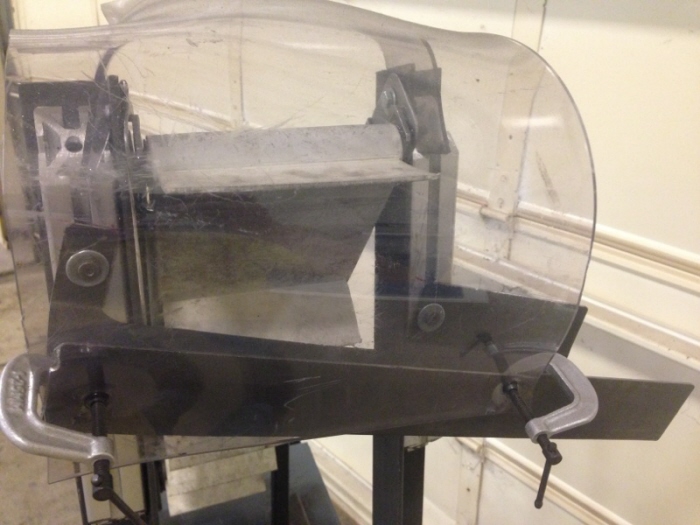
The final part chute design

Final motor mounting
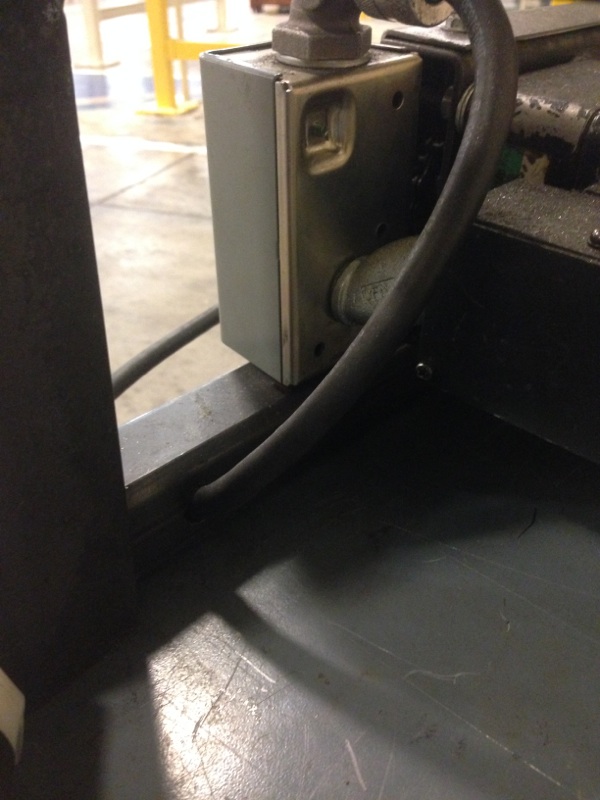
Final wiring
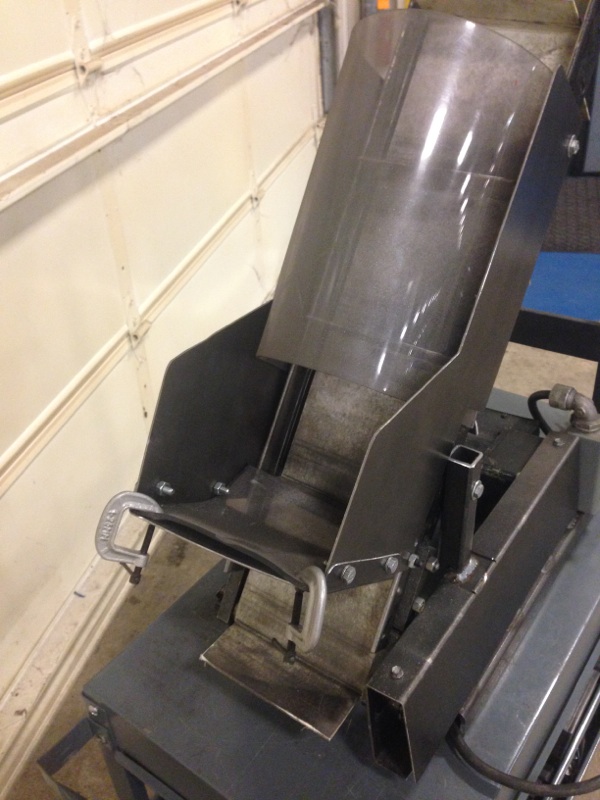
The final side guards/part catch
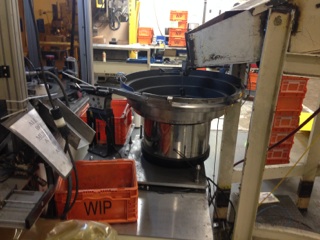
This is the machine before the conveyor. The task was to design a conveyor system to take parts from the location of the orange tote to the bowl feeder.
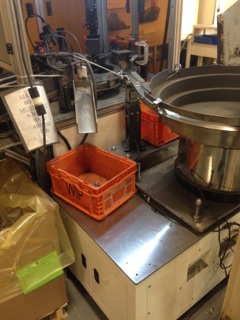
The orange tote was used to catch parts that were not inspected by the vision system in the machine. These were parts that the vision system did not "see" so they were not passed as good parts or rejected as bad parts. The operator would have to frequently come and check this tote, and dump the parts back into the bowl feeder, or as I like to call it- "recycling" the parts.
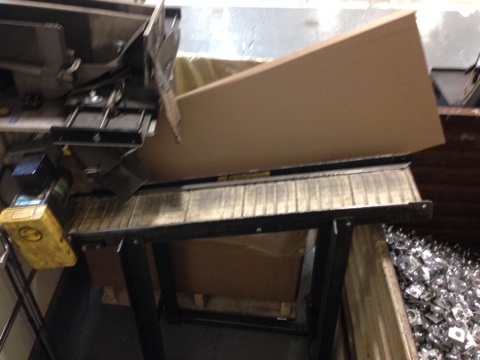
This is the conveyor that was recycled itself, and turned into the recycling conveyor. Before it was redesigned, it was an old, beaten up conveyor that was just used to carry parts from the reject chute to a big dump tub nearby. Its original function was not essential, but it made it more convenient for the forklift driver, so that they did not have to tuck it up close to the machine.
*On a side note about the reject dump tub, the recycling conveyor essentially eliminated it from the process. As said before, the intention was just to recycle the missed parts, but production later decided that they could just close off the air valve to the reject chute so that the bad parts would be pushed onto the conveyor. This meant that the bad parts would be recycled into the bowl and passed through the machine and checked multiple times. This was a huge process improvement, considering that the reject dump tubs would just be dumped back into the machine another shift.
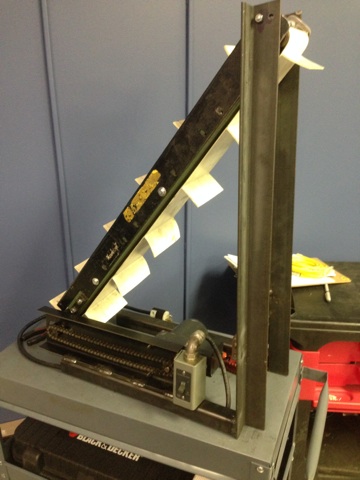
The conveyor frame and mount were heavily modified. The parts could now be carried up a steep angle, so that the end of the conveyor was above the top of the bowl feeder. The frame had to be shortened and the lips on the top side walls had to be shaved down to fit a new belt with cleats.
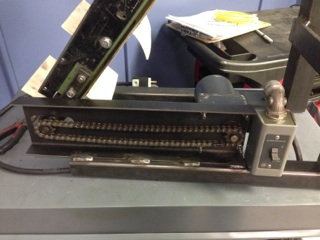
A custom motor mount was created so that the motor was out of the way of the chutes on the machine. The chain then had to lengthened.
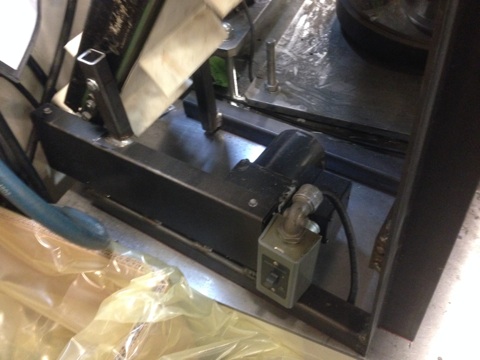
A chain cover was then created to protect the chain and the operator.
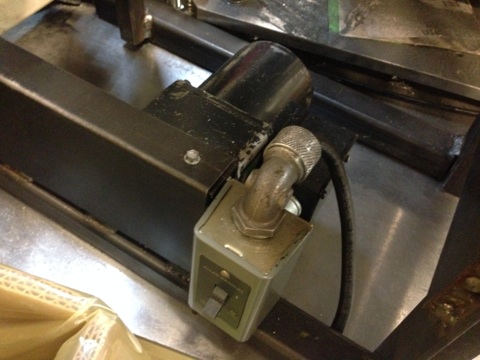
The conveyor was rewired, and a new switch was connected to make it easy to access. The cable was then led through the hollow square tubing so that it was out of the way.
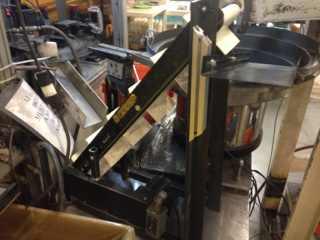
A part chute was then mounted to the conveyor. Some pieces of 80/20 aluminum track were used to fasten the conveyor, so that the angle was adjustable.
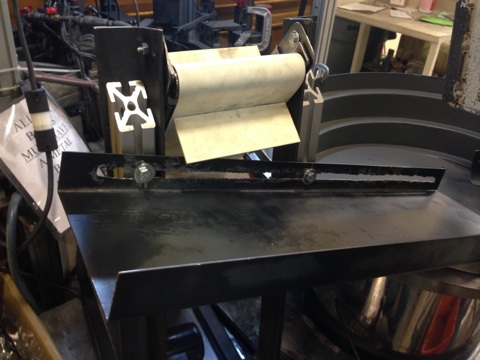
The first part chute design worked, but it was not aesthetically pleasing. I definitely had a hard time milling the notch along the side, but I learned something from it!
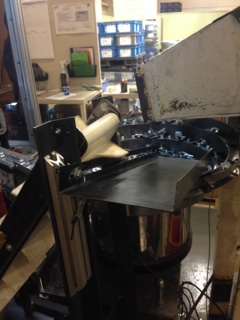
Aside from being ugly, the part chute had another problem. The cleats would constantly rub against the metal, which would cause major ware to the conveyor belt.
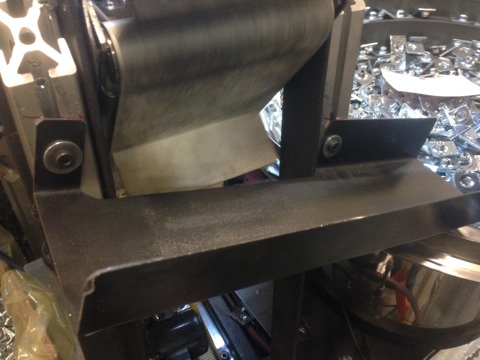
This was the solution: the redesigned part chute looked a lot better, and it does not come in contact with the cleats. It is also a lot smaller, which works just as well and is much lighter.
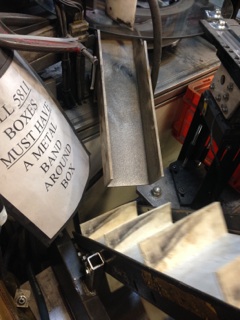
There was another problem... most of the parts would come off the chute and bounce off the conveyor. Rather than recycling parts, it lost a lot of parts.
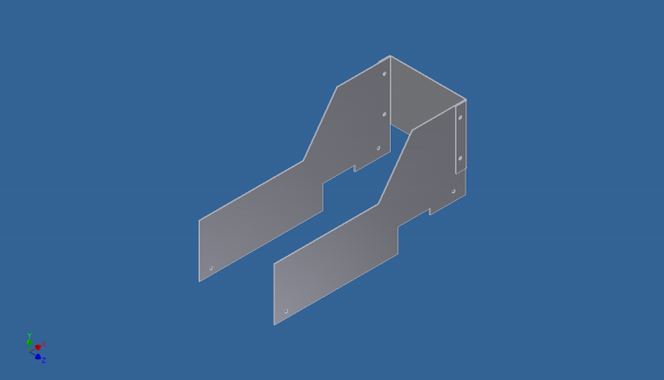
Using Autodesk Inventor, I designed some sheet metal side guards that would act as a part catch. This image actually shows an assembly of three different sheet metal parts.
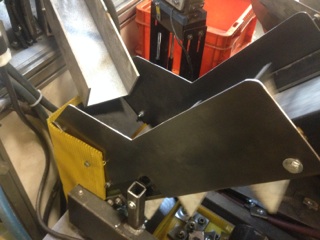
The side guards were fabricated, and they fit nicely on the conveyor.
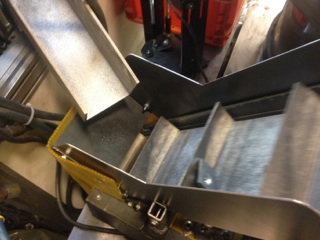
The side guards definitely helped, but parts were still getting lost. Many would bounce just right so that they would fall down the small gap between the cleat and the guard at the back. The goal was not to lose any parts, so something had to be fixed.
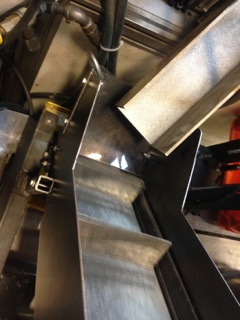
The solution was to add a plastic flap to catch the parts. The plastic was very flexible, so it would bend when it came in contact with a cleat. It would then drift back into position to close the gap. Using this material ensured that the conveyor belt would not suffer ware damage.
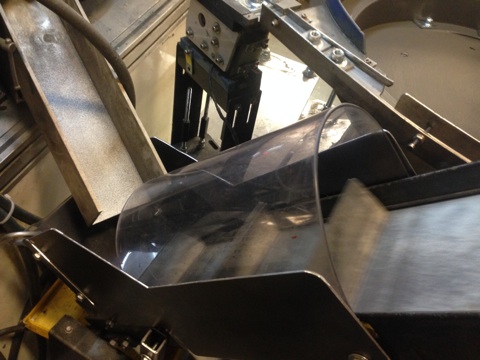
The plastic worked so well that it was added to other parts of the conveyor. Every once in a while, a part would get flipped up and over the side guards. This meant the parts would get lost or flung at an operator causing a safety hazard. This plastic was added to deflect that occasional part that wanted to jump over the side guards. It also looked pretty cool.
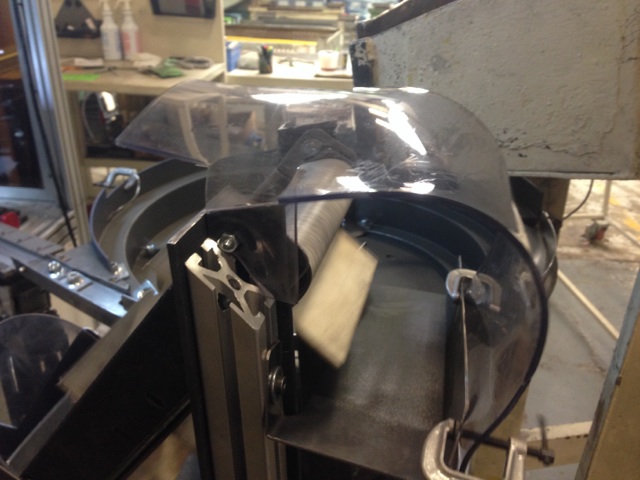
This was another area that created a potential safety hazard. Sometimes, if a part was aligned on the belt just right, the conveyor would get lodged onto the head of a bolt at the end of the conveyor. The part would then finally release and get launched from the conveyor. I know this could be a safety hazard from personal experience. One time when I was watching the conveyor run, a part was launched off the end of the conveyor and hit me right in the safety glasses. This plastic guard was frustrating to make, but it was definitely a necessity.
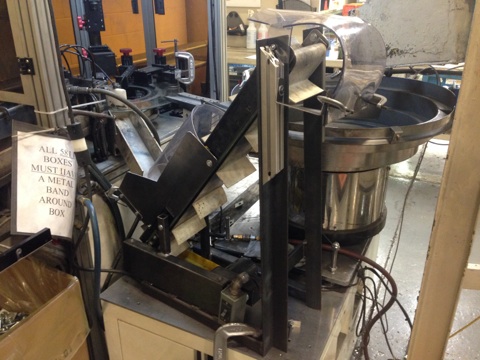
Here is the final product at work.
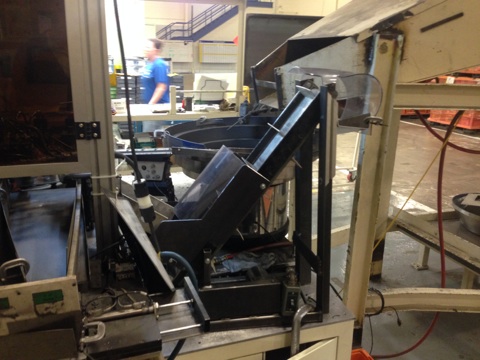
It was a fun project, I learned a lot, and I was happy to see that it helped.
gLike