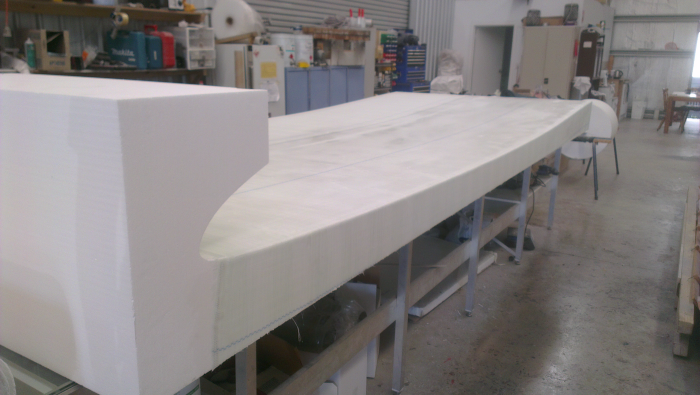
Once the design of the main body shape was settled, a profile was sent to a foam supplier to be shaped using a CNC.
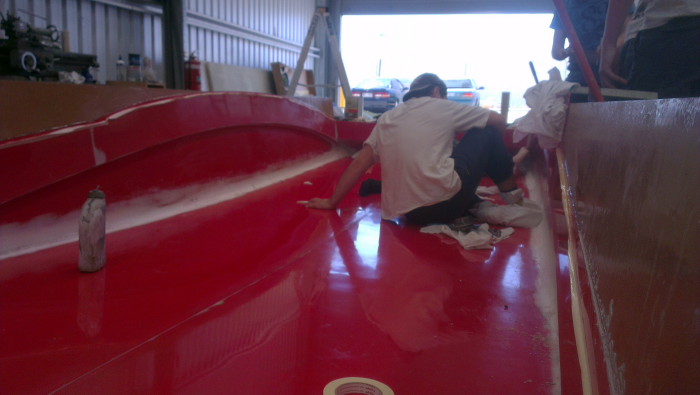
The surface of the mould and the sides were then prepared for a carbon fiber infusion process.
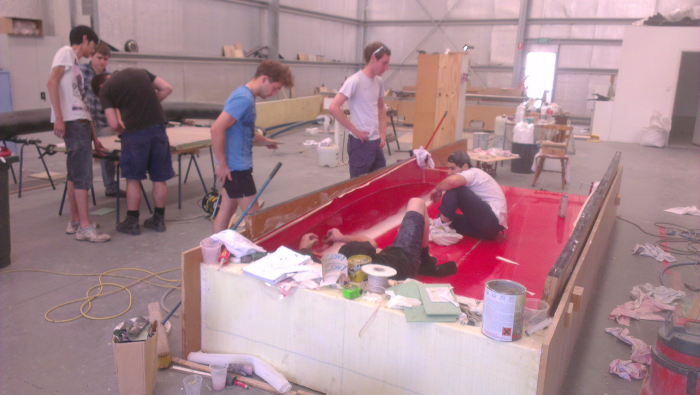
Applying a release wax to the surface of the mould.
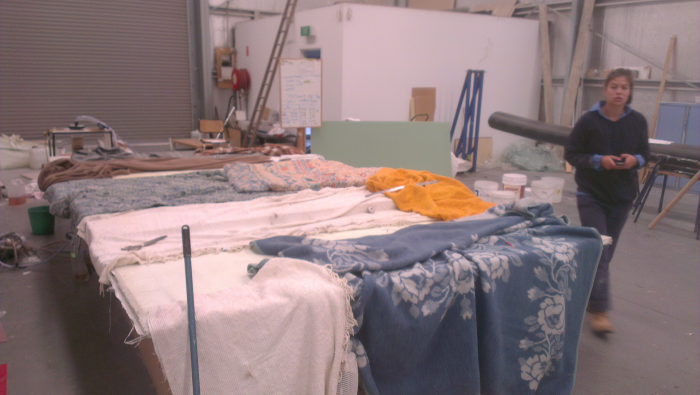
The carbon fiber was layered into the mould, then baked to encourage drying.
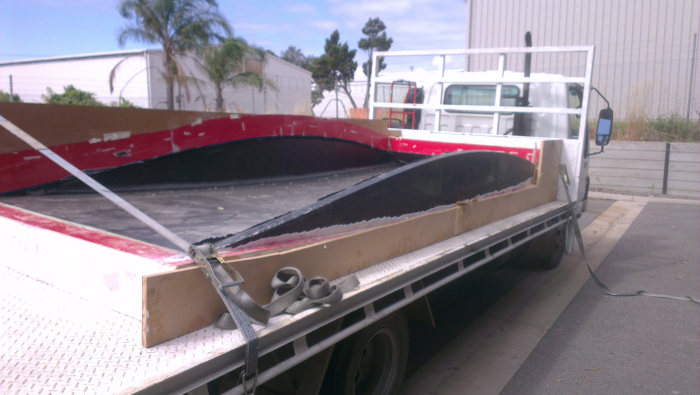
The main body shape after the baking process.
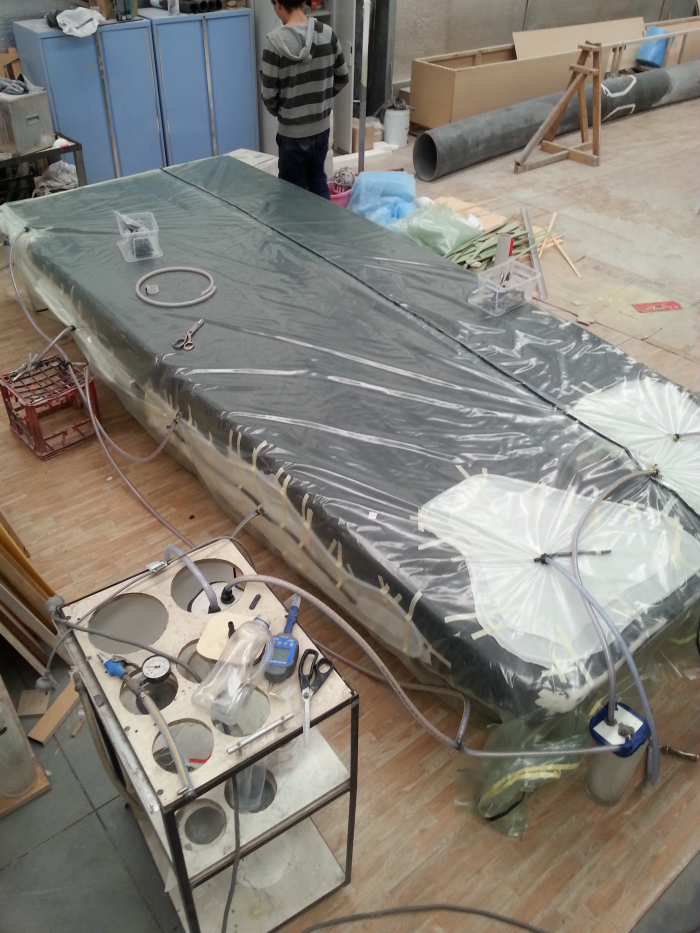
Reinforcing a few dry spots with extra resin using an infusion process.
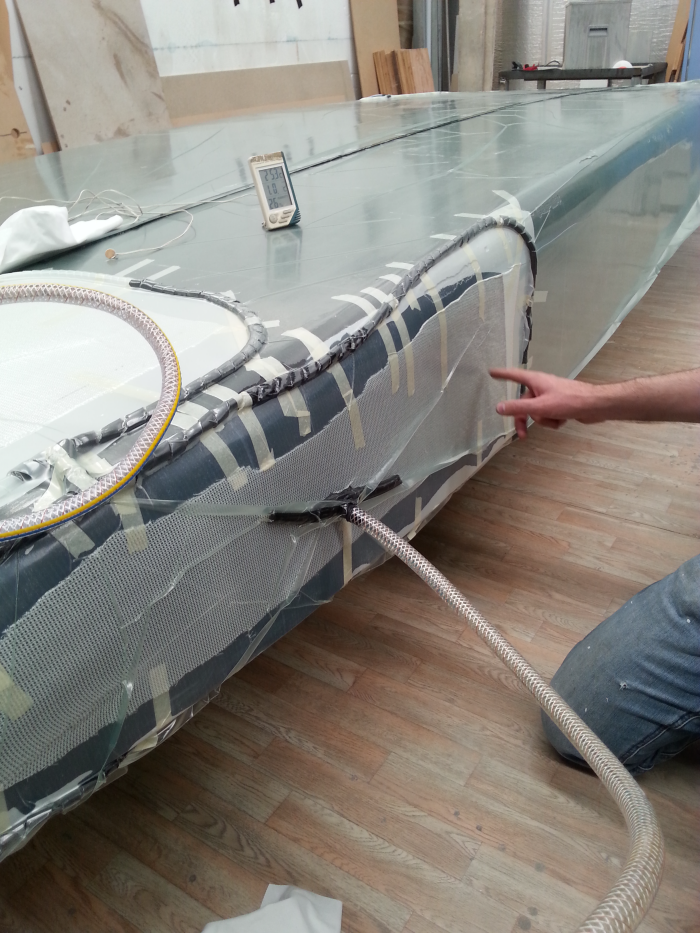
Reinforcing a few dry spots using an infusion process.

Preparing a smooth clean table surface to create a custom carbon fiber panel.
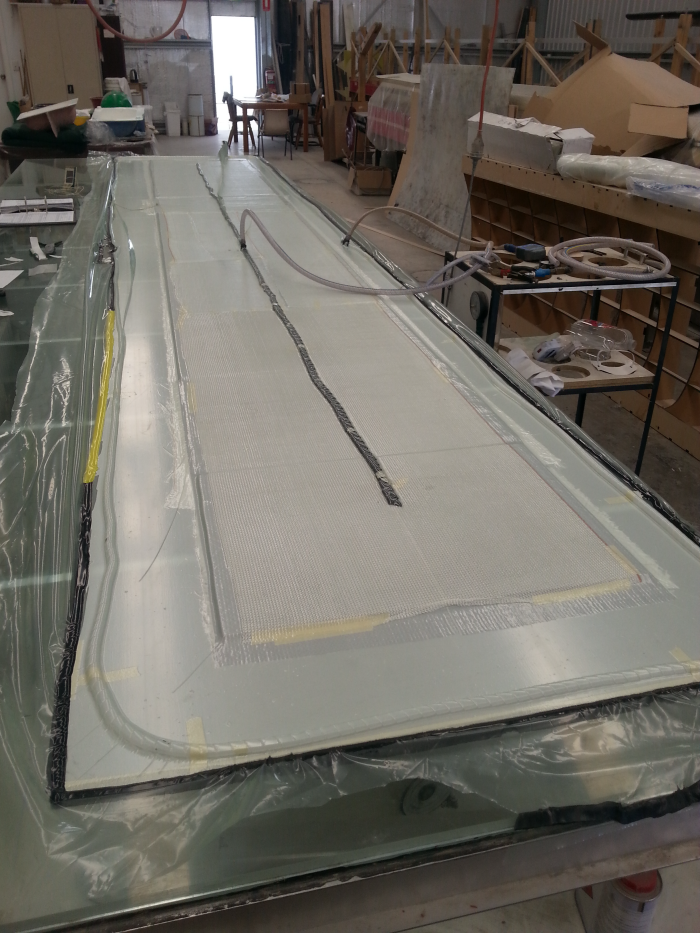
Using an infusion method to create our carbon fiber panel. The material will then be shaped and used as a spar to provide additional strength to the vehicle.
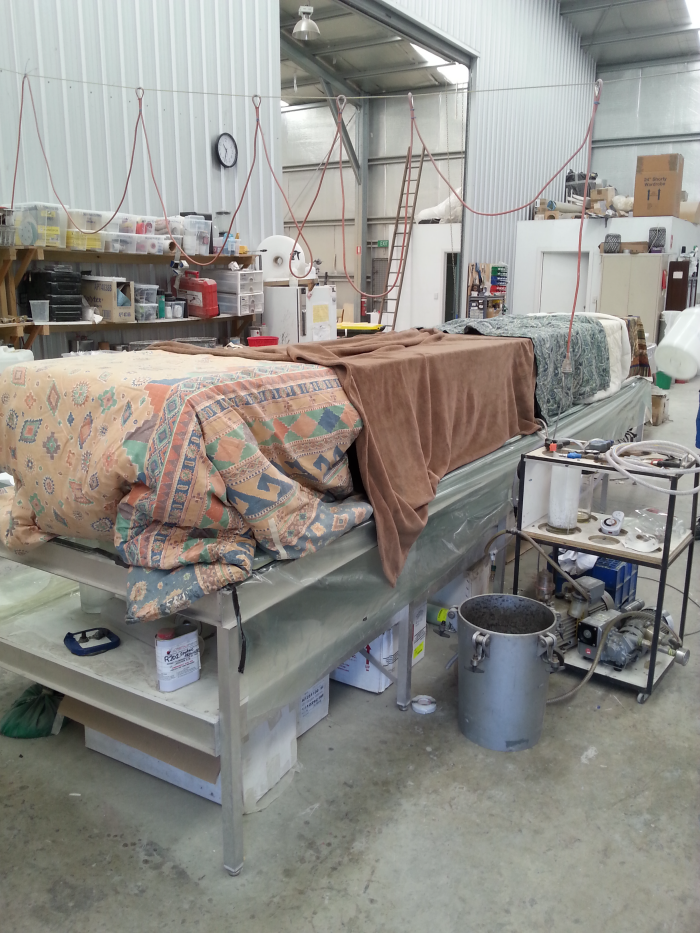
Baking spars to speed up the drying process.
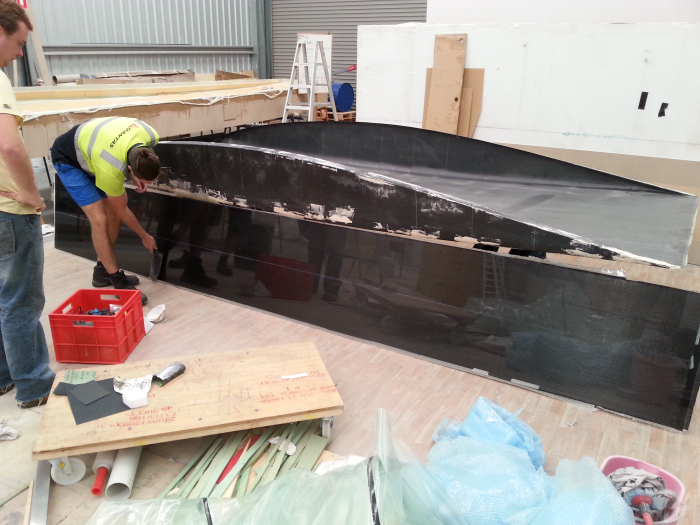
The carbon fiber panel we made that will be shaped into spars to provide additional vehicle stability/strength.
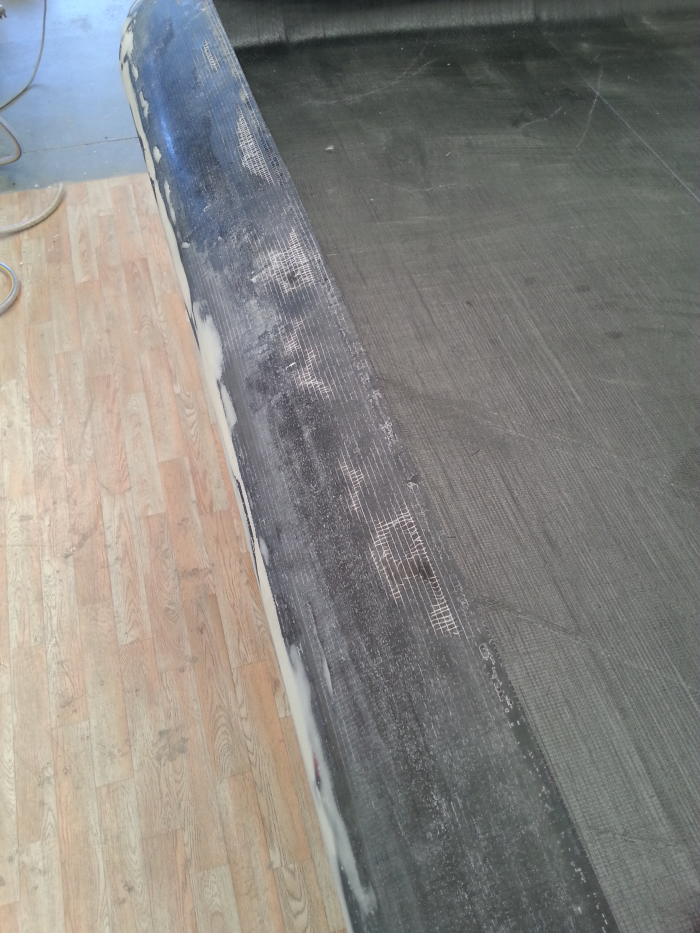
Leading edge of the vehicle.
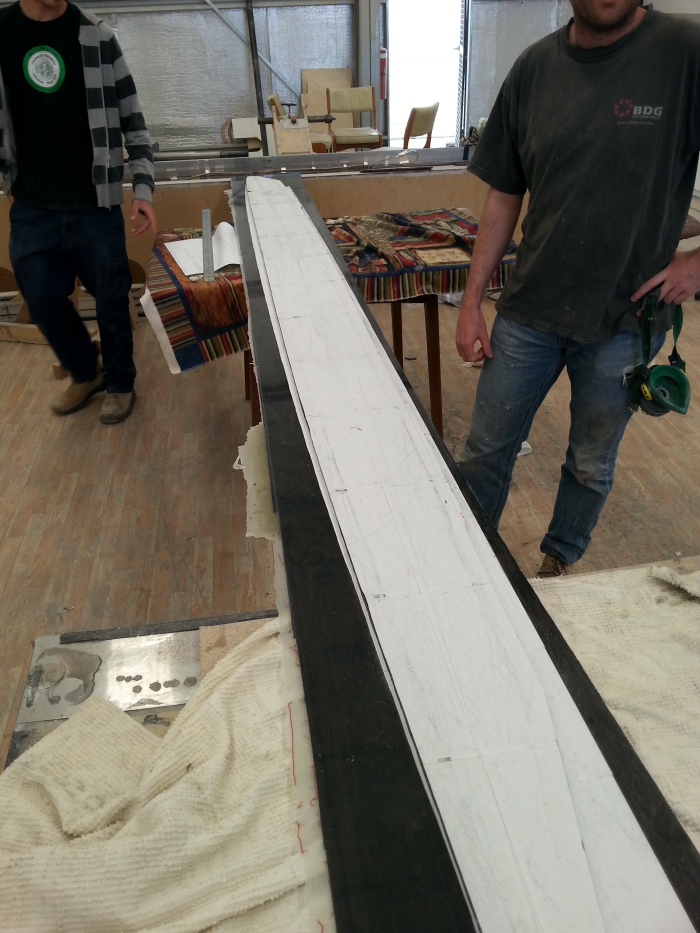
Shaping the profile for the carbon fiber spars.
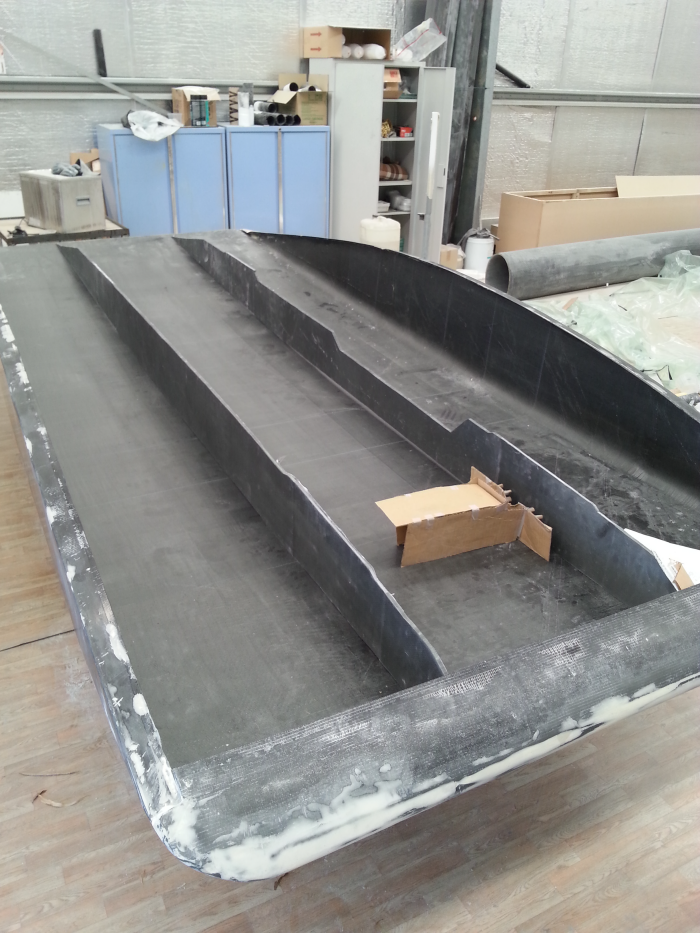
The spars have been shaped and partially installed.
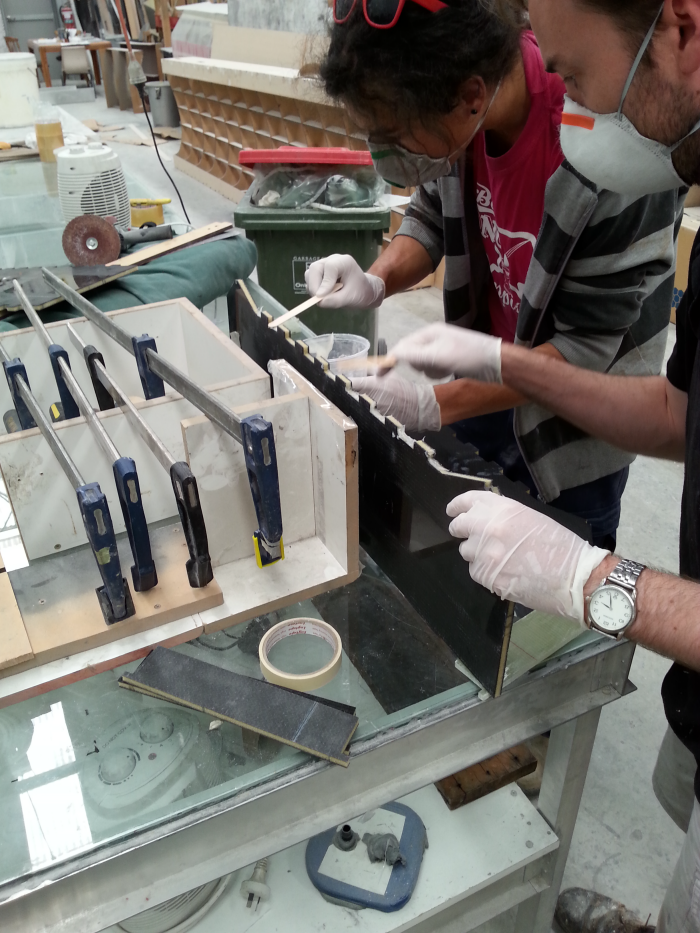
Constructing a torsion box which was attached to the vehicle body and the spars.

Constructing a torsion box which was attached to the vehicle body and the spars.
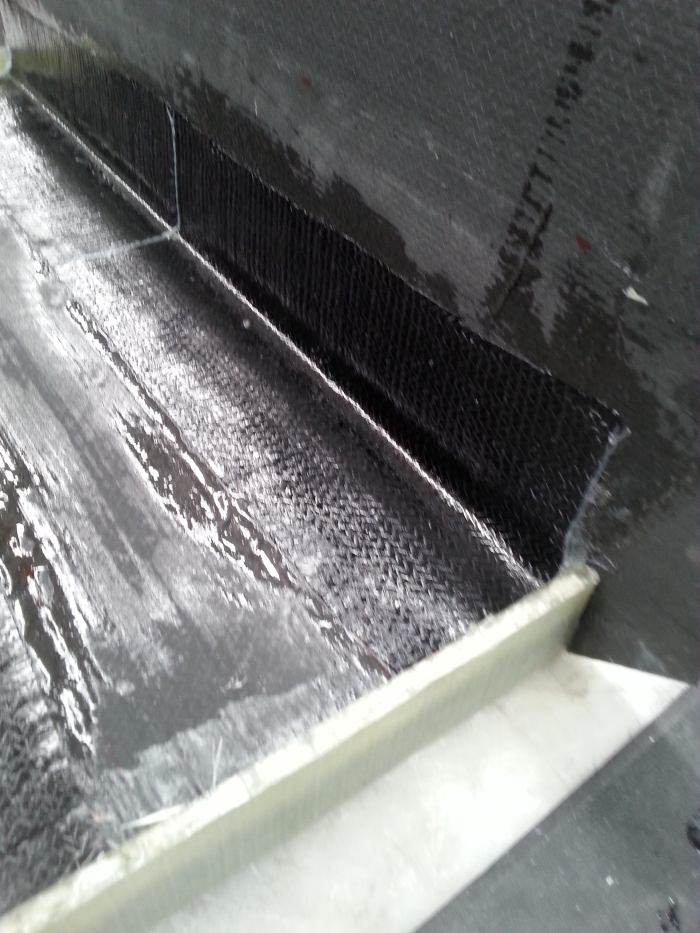
Wet laying the spars to the base of the vehicle to provide additional strength.
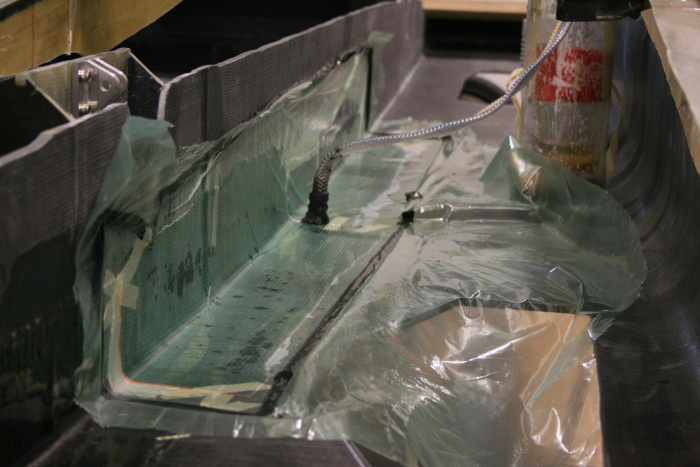
Using an infusion method to secure the spars to the vehicle body.
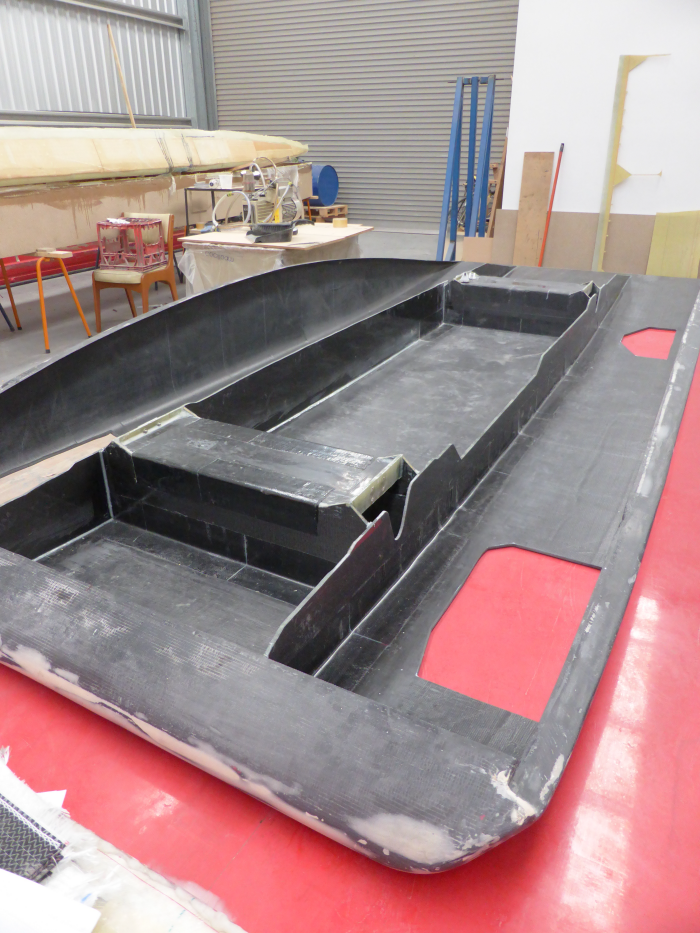
Vehicle body with spars and torsion boxes attached.
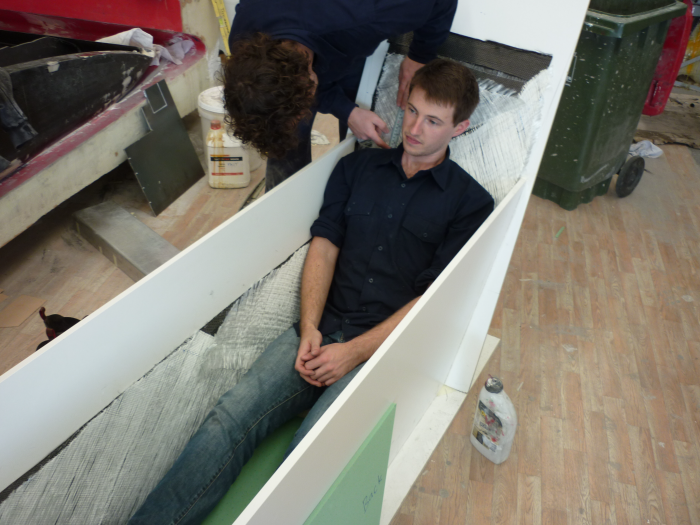
To create the driver tub, a melamine mould was created and then the designed layers of carbon fiber/fiber glass and foam were used.
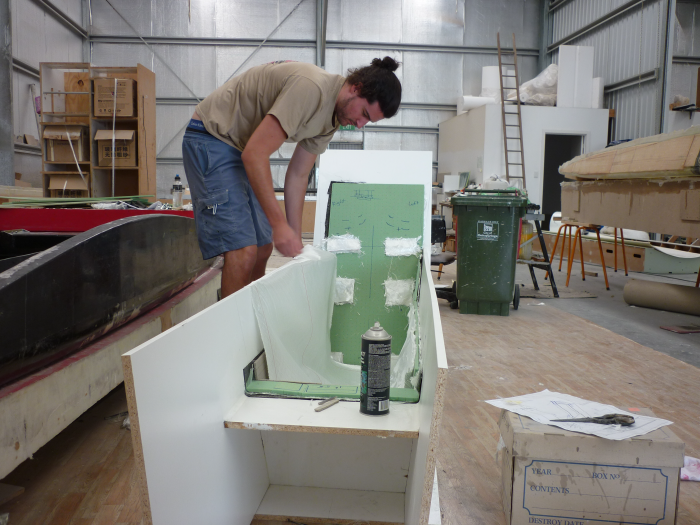
Applying the layers to the driver tub mould.
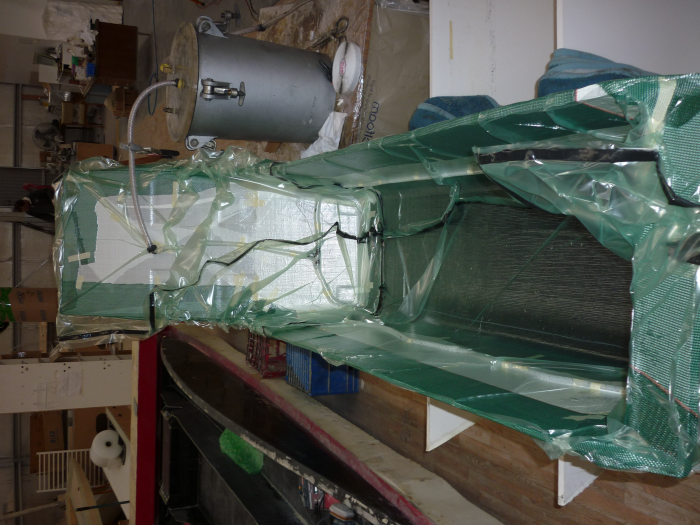
Carbon fiber infusion for the driver tub.
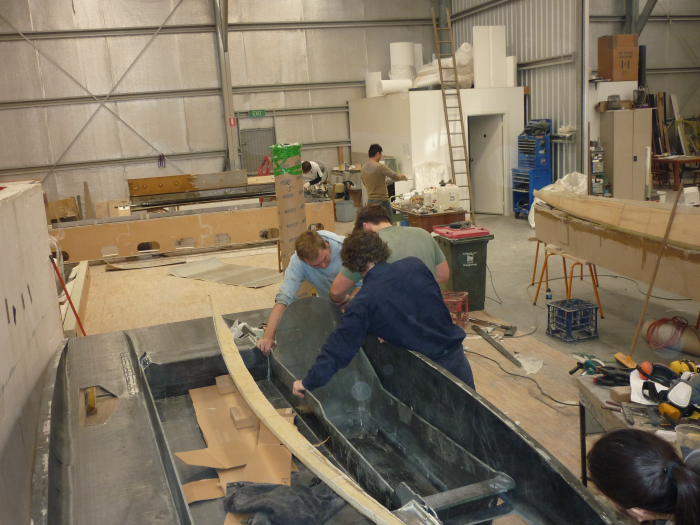
Sitting the tub into the vehicle body.
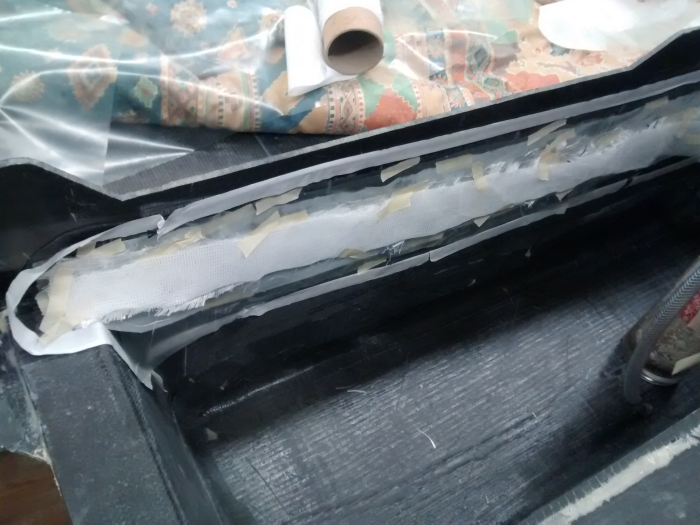
Setting up a carbon fiber infusion to attach the driver tub to the inside of the vehicle.
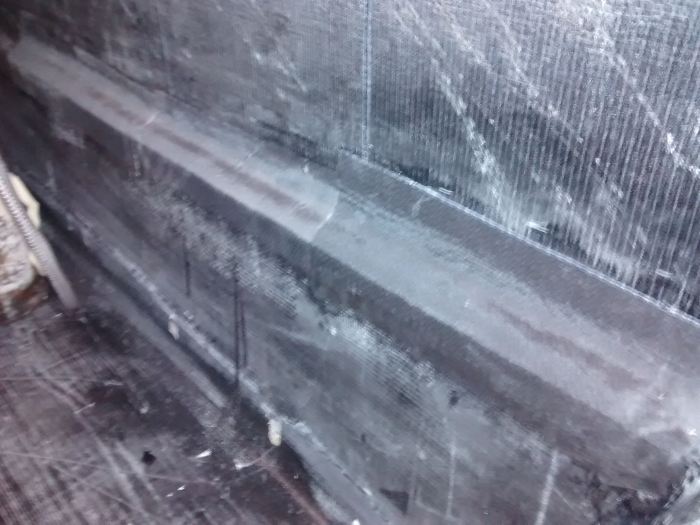
Result of using the carbon fiber infusion method to attach the inside of the tub to the side of the vehicle.
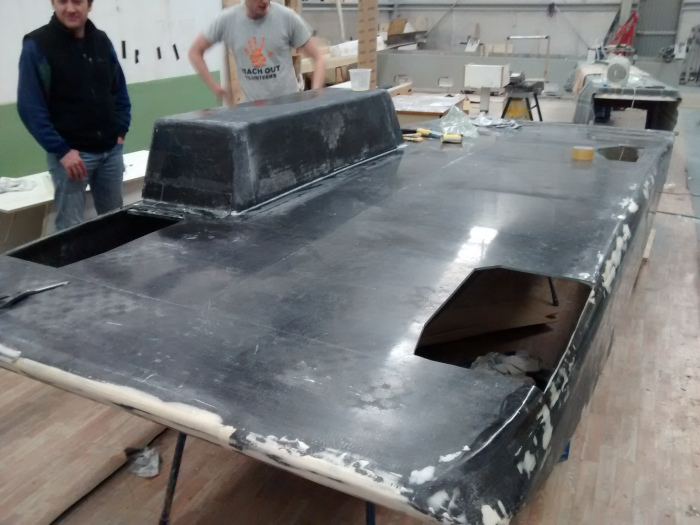
Bottom surface of the vehicle body.
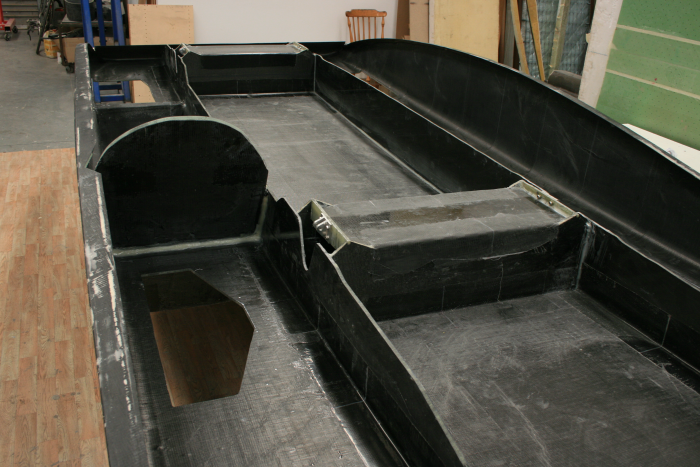
View from the back of the vehicle.

Using a wet lay carbon fiber process to secure the tub to the vehicle body. Strips of removable plastic were used to provide a smooth finishing surface.
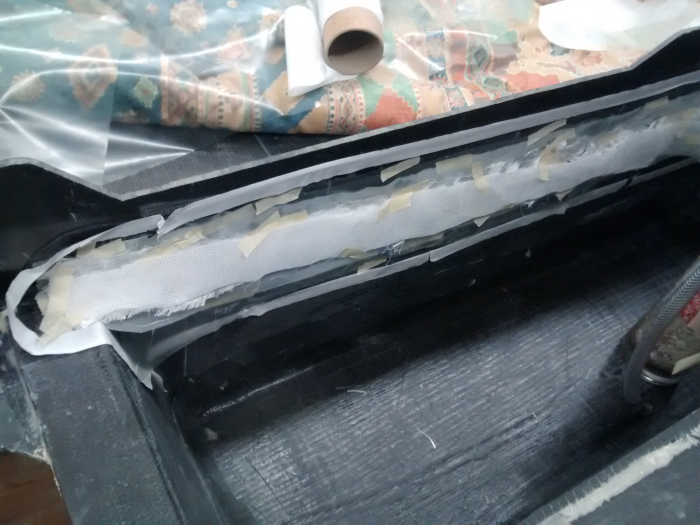
Using multiple methods, we wetlayed the carbon fibre to attach the tub to the vehicle base. Ontop of the wetlay is a thick layer of fibre glass, which was used as a 'sponge'. These layers had a vacuum applied to it. These combination of methods help minimize the additional weight added during the wetlay process.
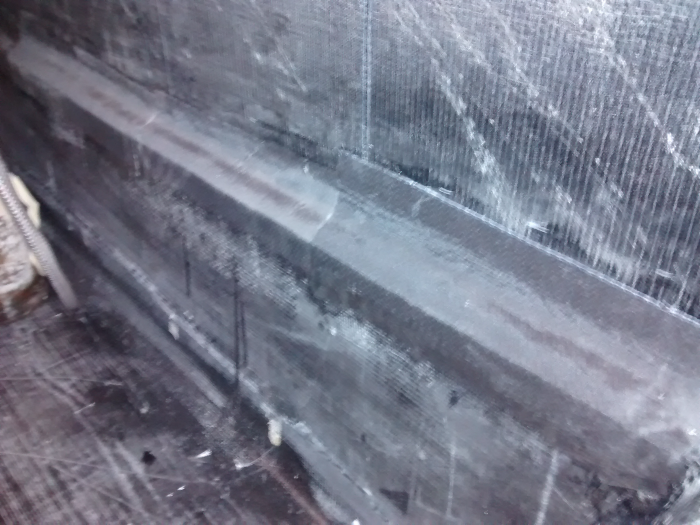
The result of the methods in the previous image.
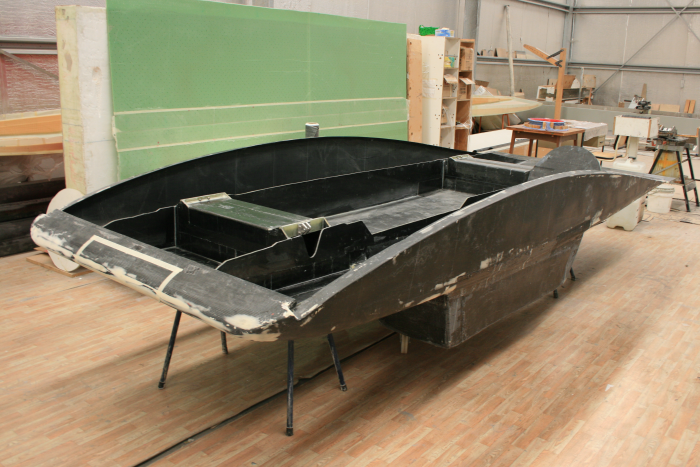
Isometric view of the front of the vehicle.
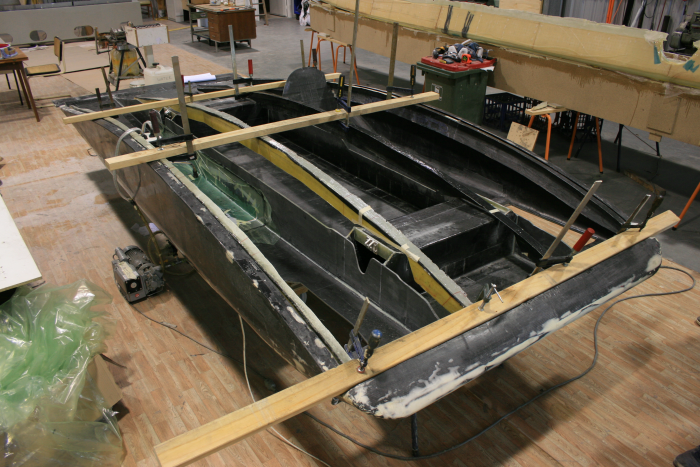
Creating a frame which was then used to shape the fiberglass roof.
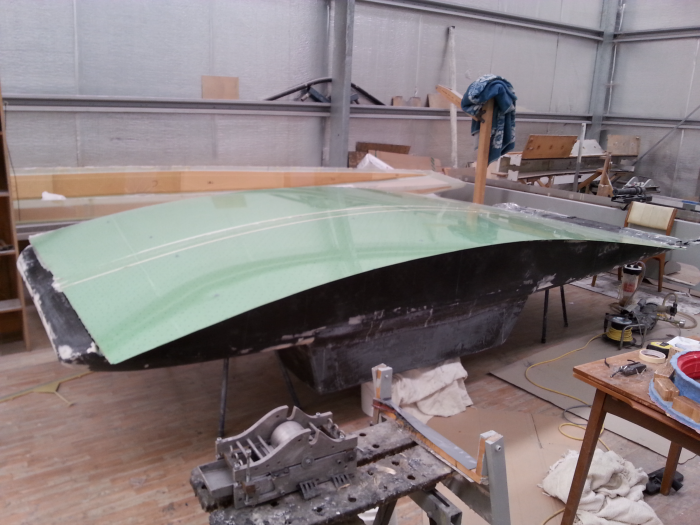
Profile shape of the fiber glass roof.
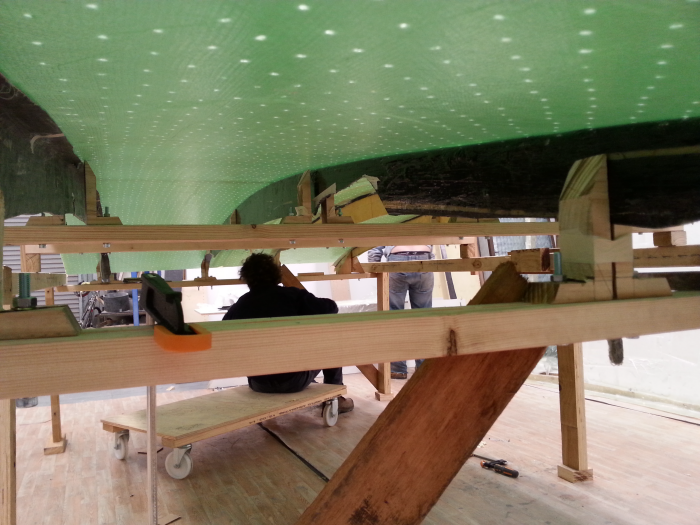
Securing spars to the roof.
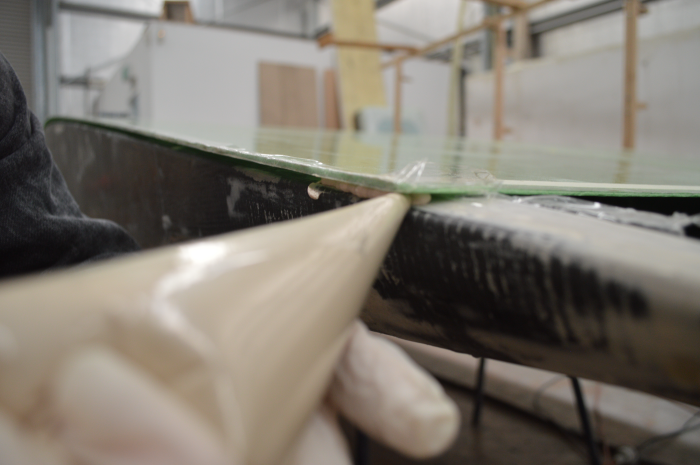
Using a special blend of resin and powder we made smooth surface where the roof will sit on the base.
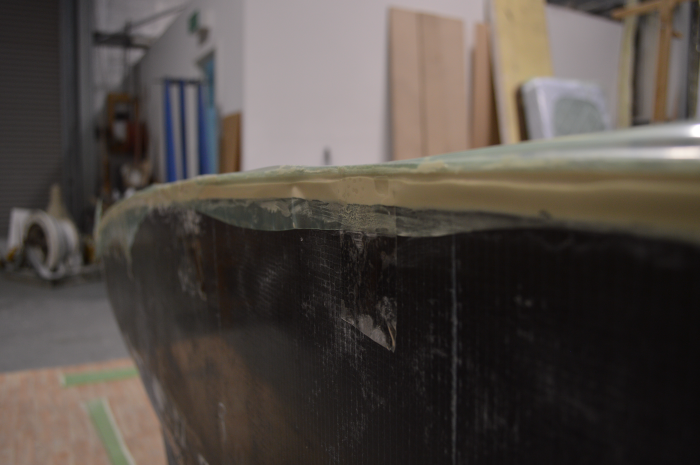
Using plastic to provide a smooth surface and to get the material to where its needed.
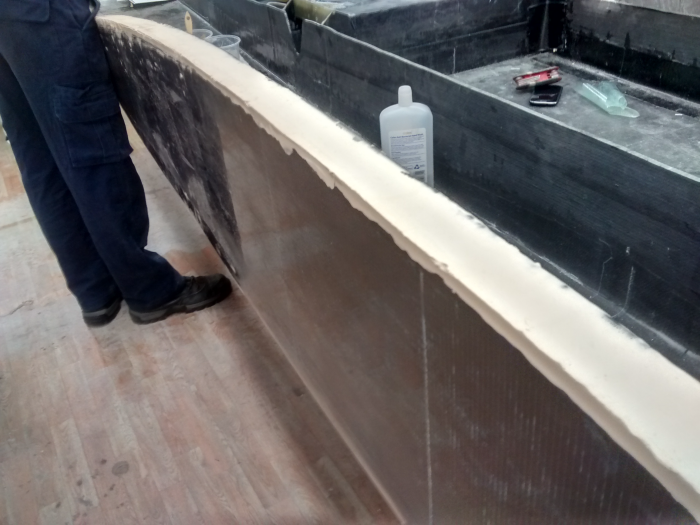
End result of the area where the roof will sit onto the base.
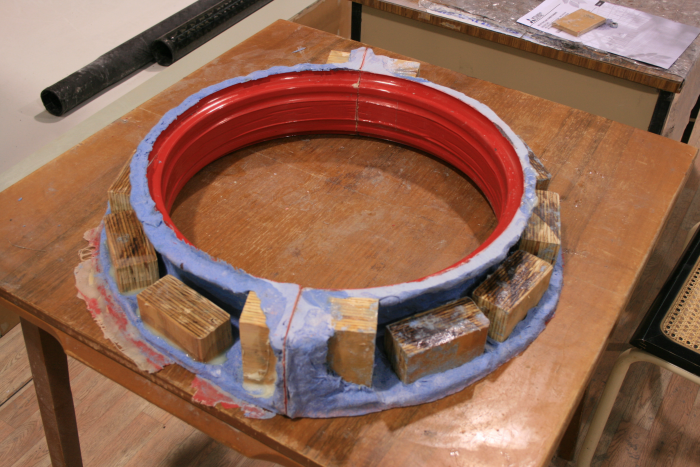
Custom made wheel mould that will be used to make a composite wheel.
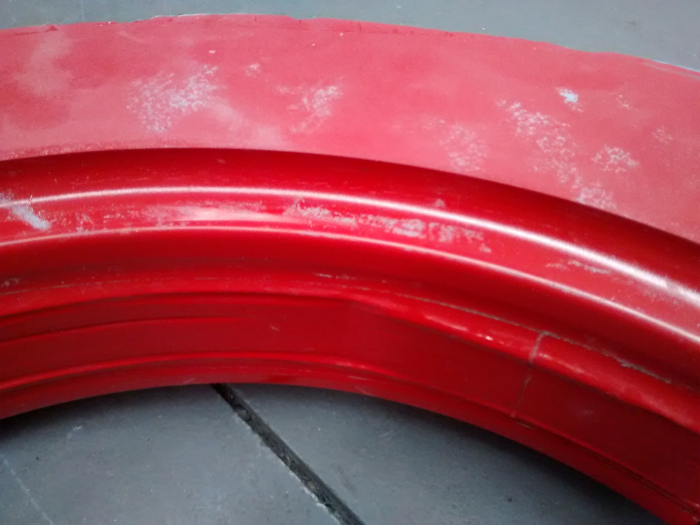
Inside face of the wheel mould.
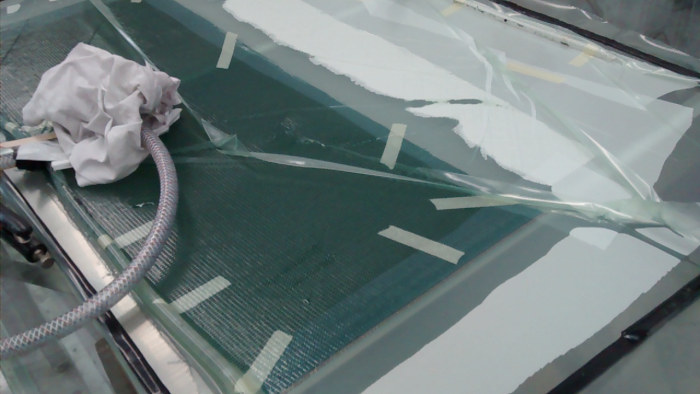
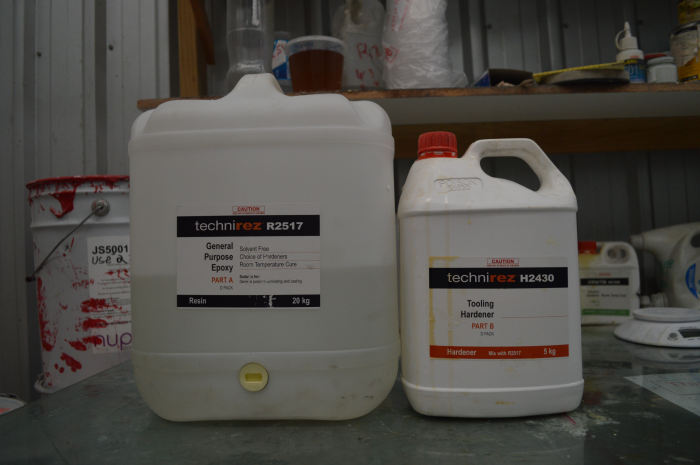
The primary resin we used.
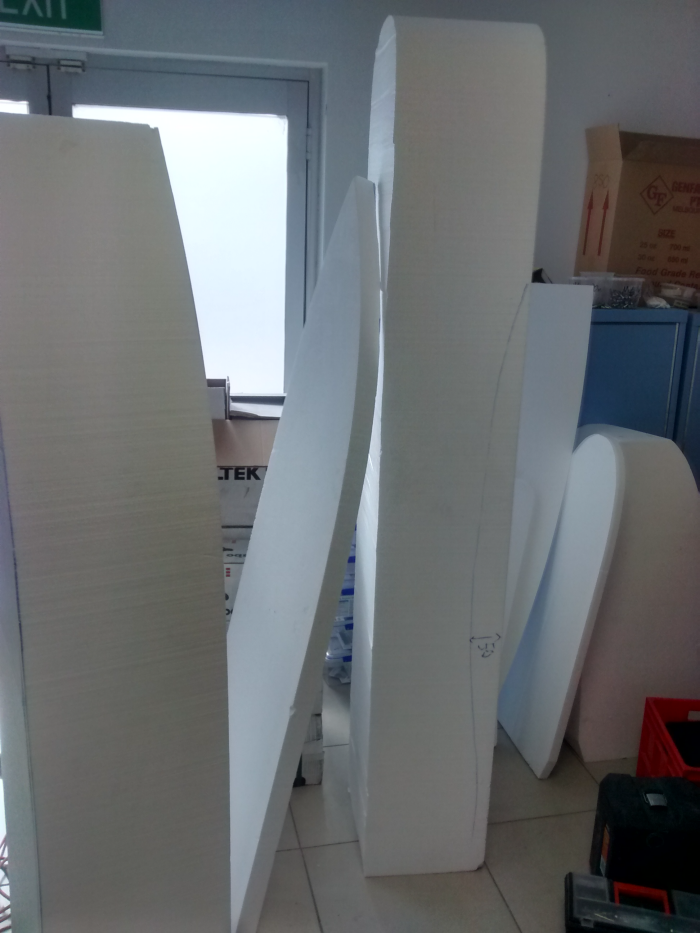
The foam moulds we received from a supplier who had the CNC cut from designs we made. These moulds would go on to be used as fairings for the vehicle.
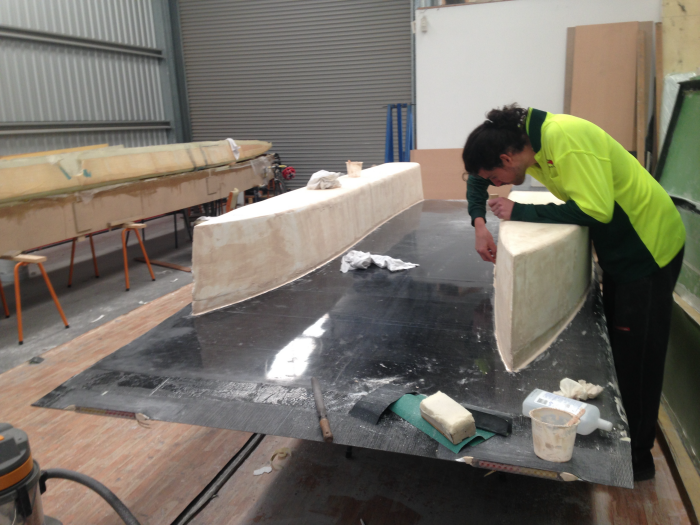
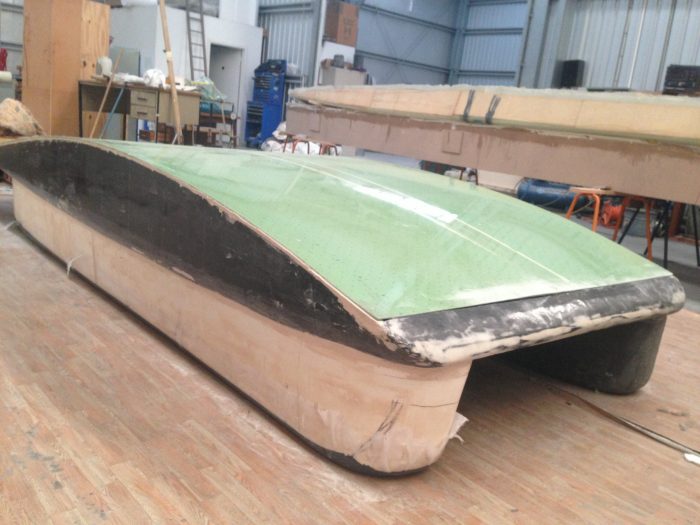
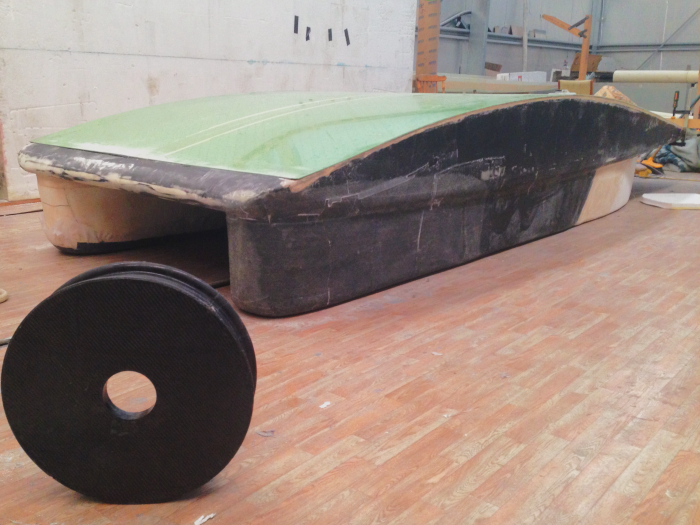
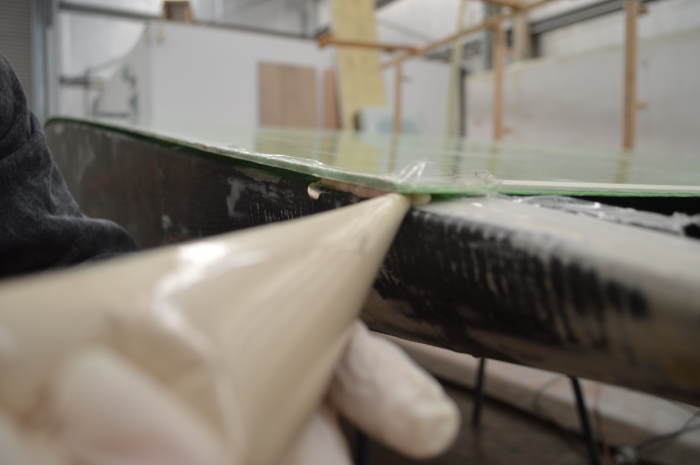
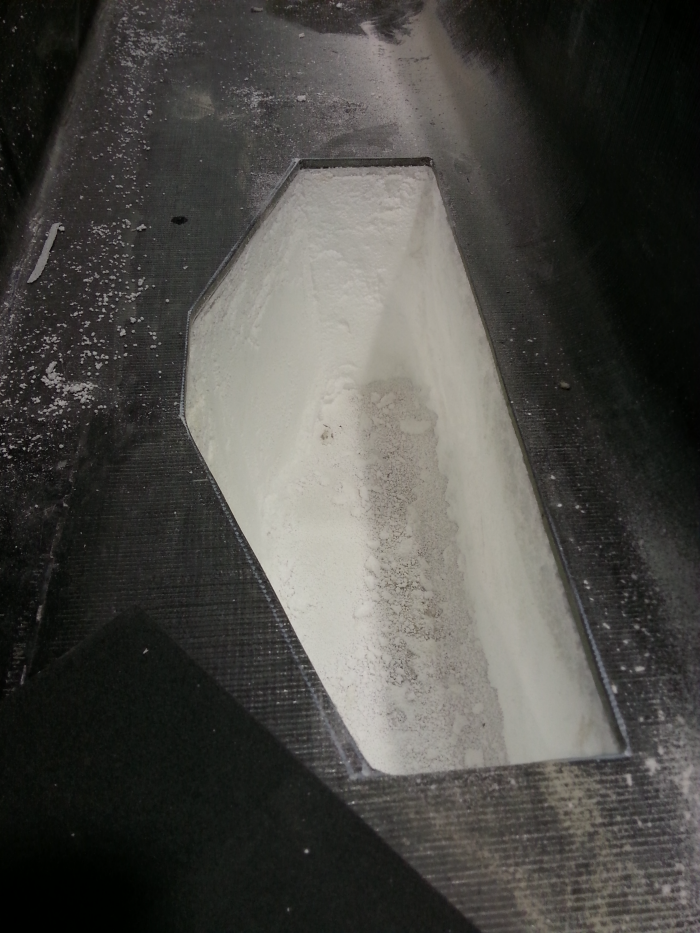
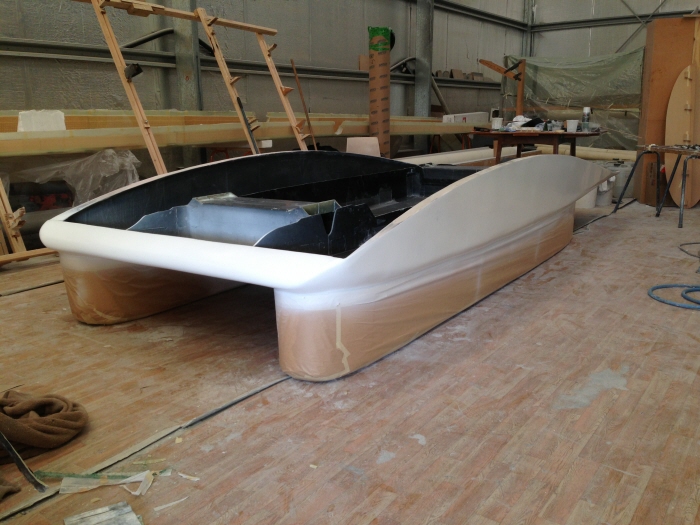
Paint Preperation.
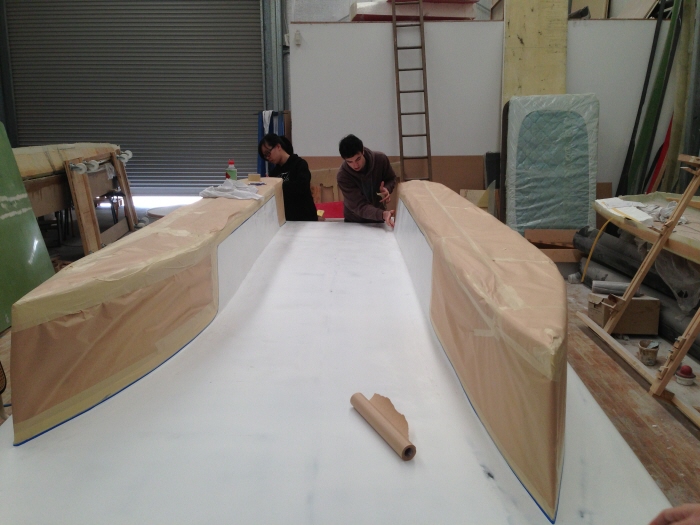
Paint Preperation.
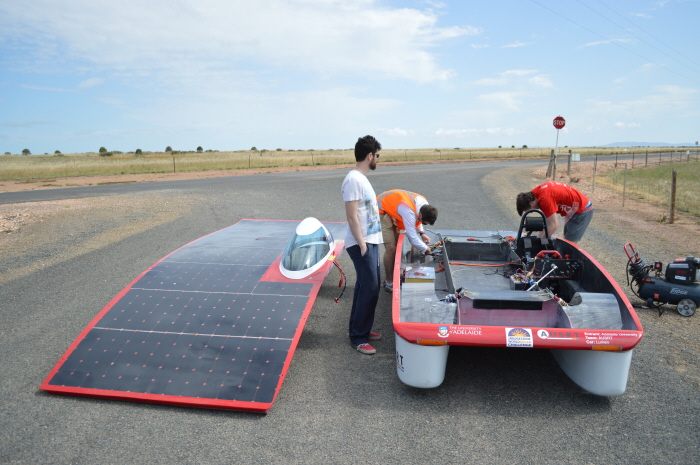
Testing.
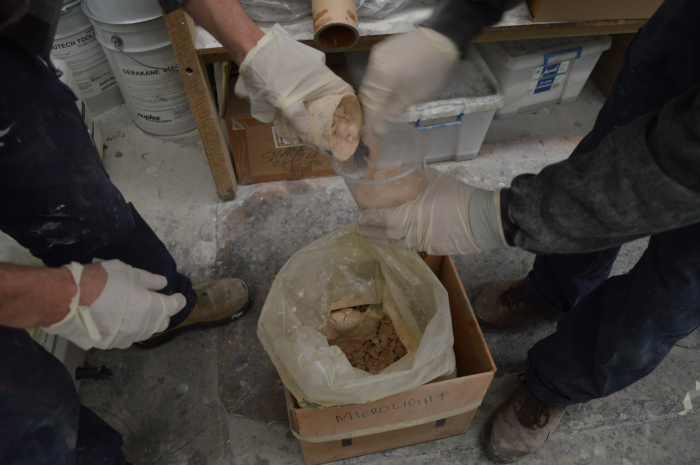
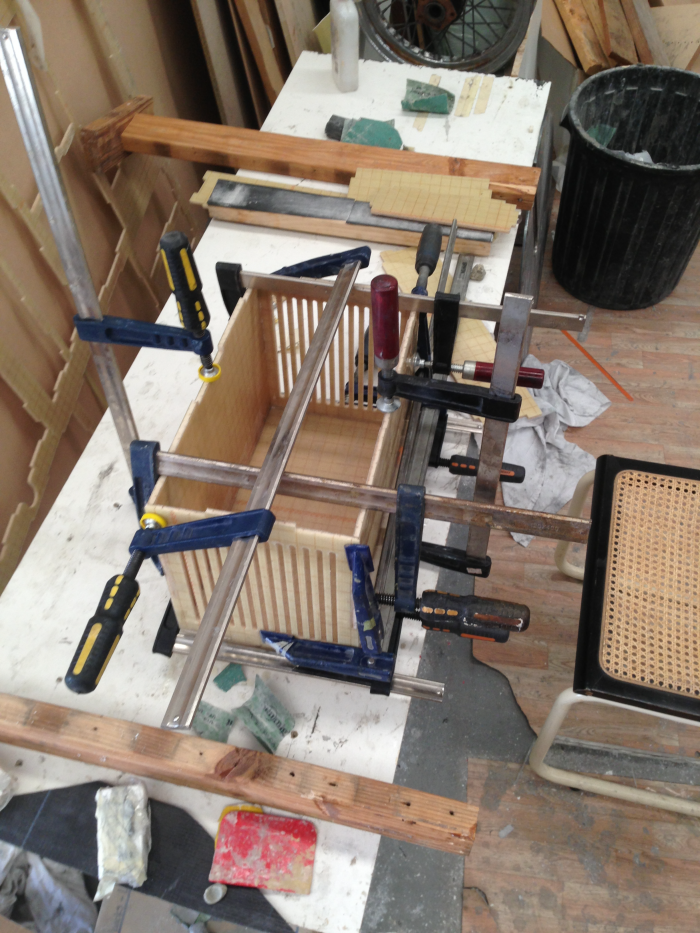
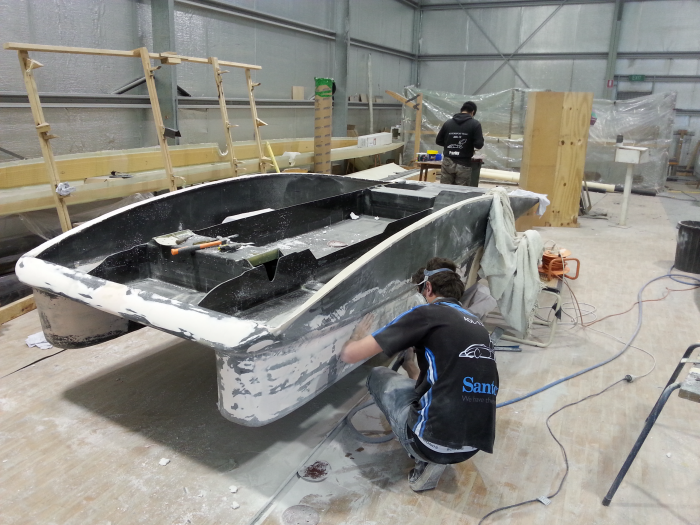
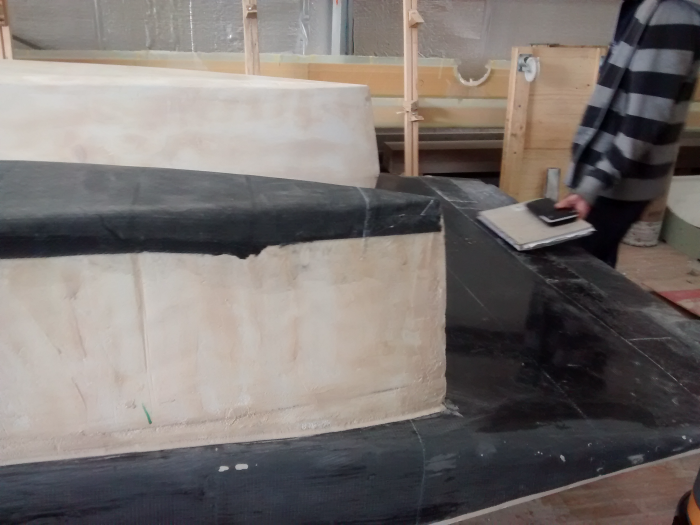
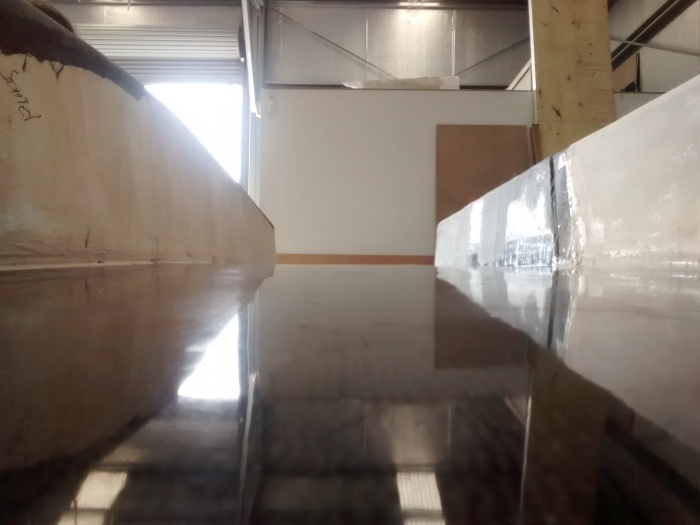
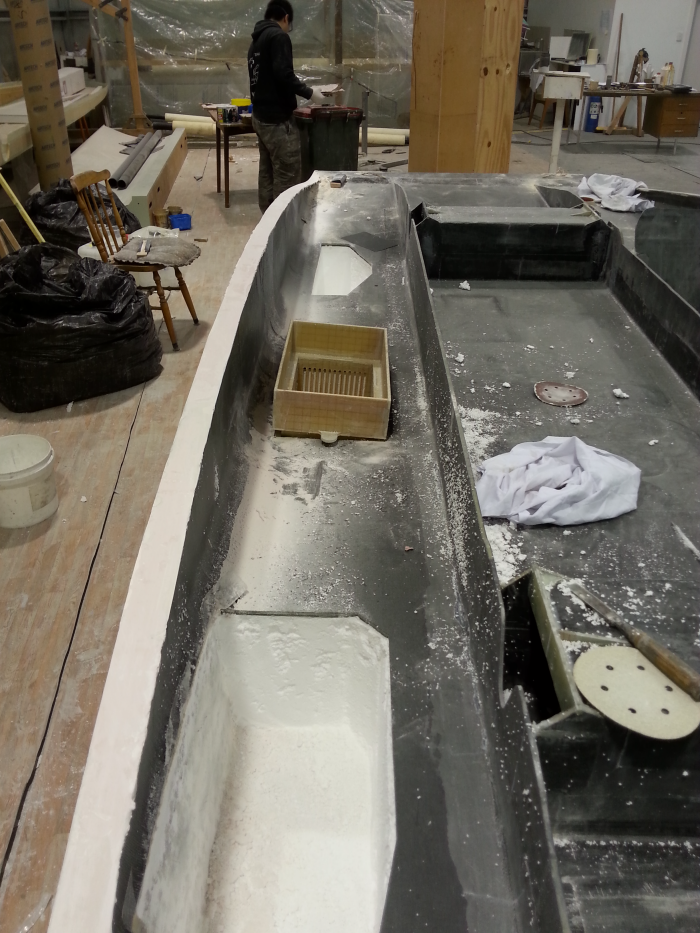
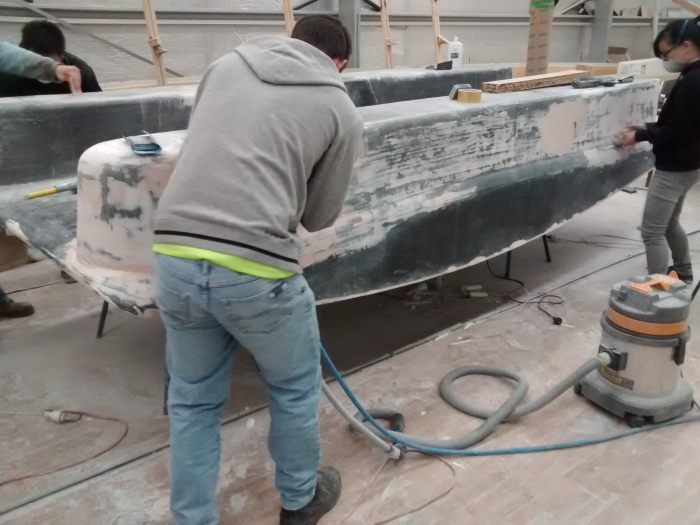
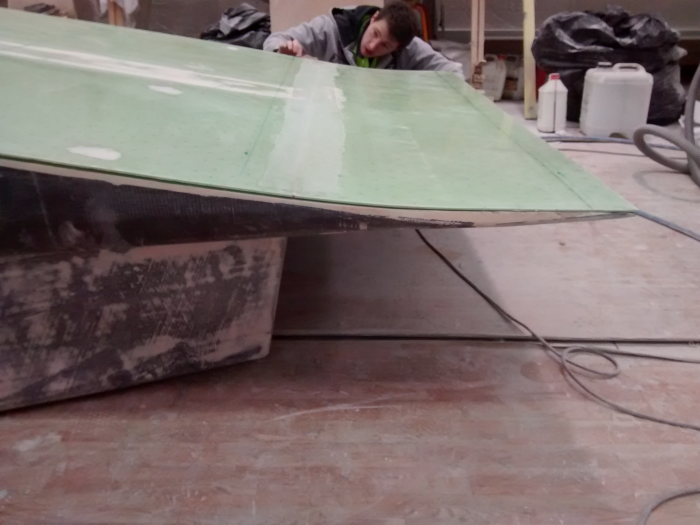
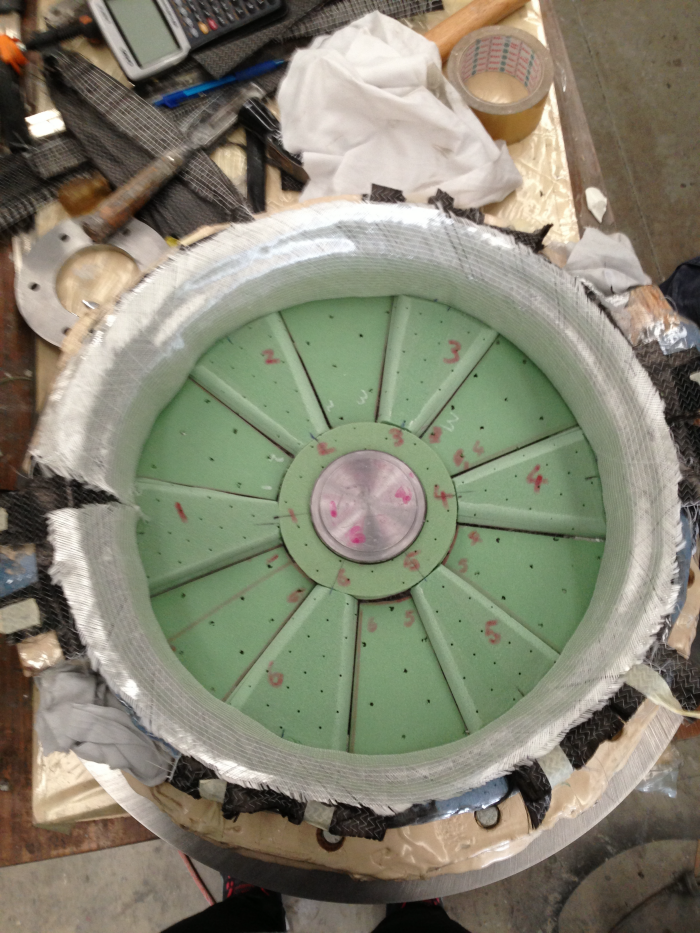
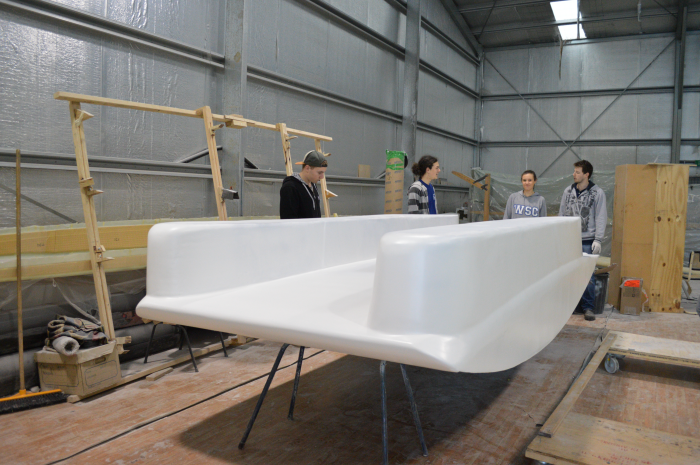
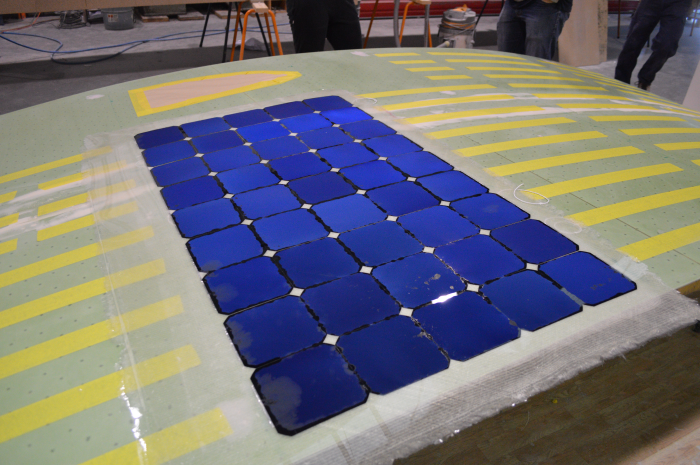
gLike