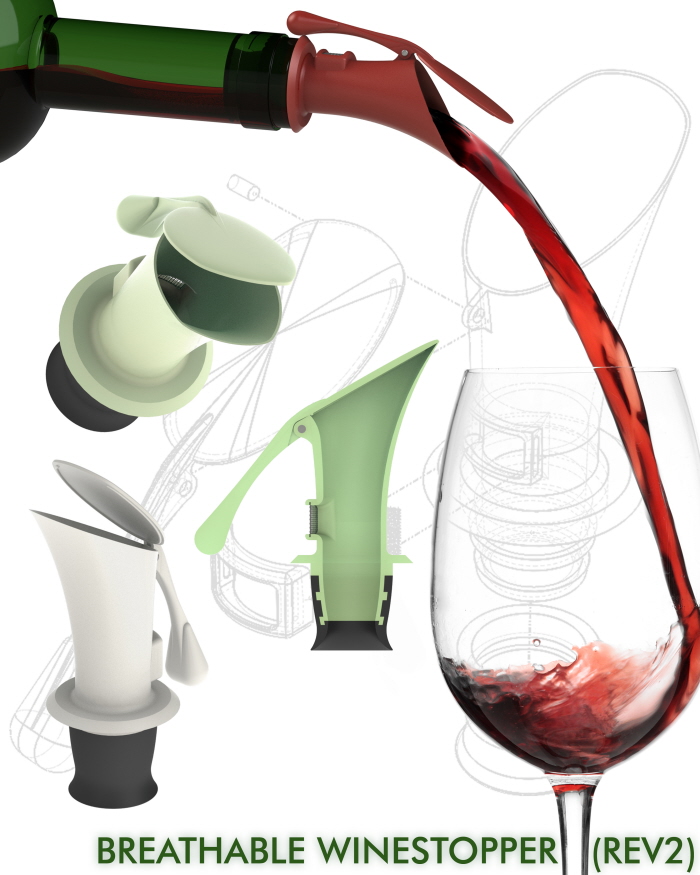
Building on the concepts learned in the first version of this collaborative project with Andy Wilder, the REV2 Breathable Wine Stopper aims to provide a easier wine pouring experience. Firstly, the overall shape has changed dramatically, by removing the 90° bend in the stopper, creating a continuous flow from the bottle. As such, the lid has changed to hinge open when the wine pours out, and can be manually held in place with the counterweight. The shape of the spout lip has also been adjusted based on the shape of the lips of many decanters. This should create a coherent and smooth stream when poured at a certain rate, encouraging the pourer to keep from going to fast and inducing a "glug-glug" effect. The silicone stopper has been redesigned to fit nearly all bottle necks, and its curved shape keeps from creating turbulence in the wine stream. Finally a redesigned mesh screen has been placed on the top of the neck, and features an easy to remove snap cowling.
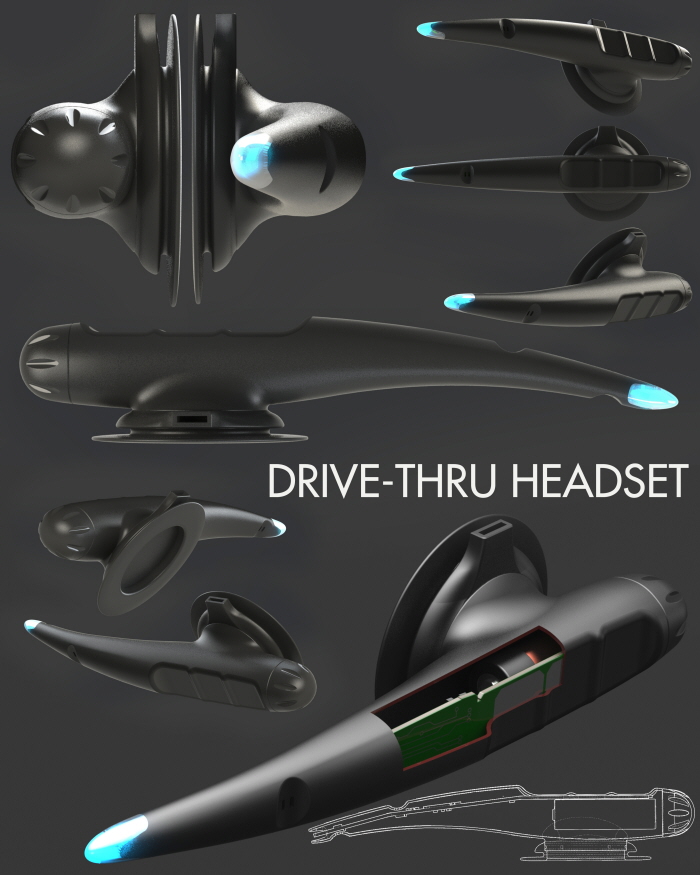
A local electronics company commissioned me to design new casings for their updated fast food drive-thru headset radios. Their design constraints were very stringent, in that it had to conform to the wearer's face, it had to have an LED at the end of the boom, it had to fit their specific circuit board as well as a standard AA battery. This design fit all of the above requirements, and was perfectly manufacturable doing so with draft angles and fittings in place, as well as structural features that would ensure this device lasts a long time in the rigors of the fast food industry.
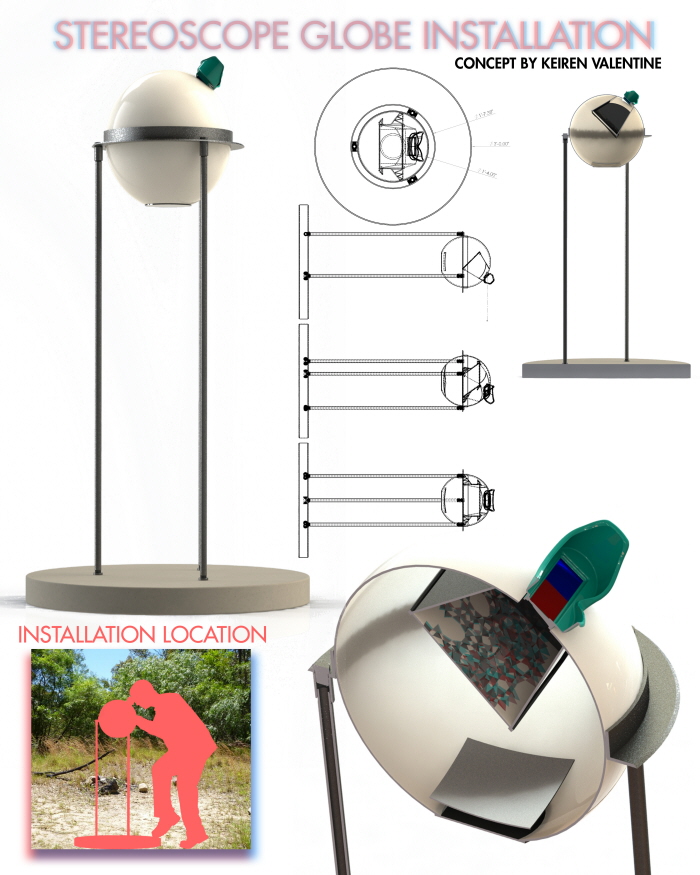
Shortly after moving to Maine, I met artist Keiren Valentine, and we discussed her idea for 10 installation sculptures scattered along a nature trail. She needed a thorough design for a grant application, and I decided to help bring her ideas together. The sculptures were to be roughly globe-shaped, stand at mid-chest height, and invite the viewer to look in and see a stereoscopic 3-dimensional image. I found all of the components online to make the sculptures, and priced them in a bill of materials (required for the application). From there, I used dimensions found on the retailers' websites for the products, and modeled them in Solidworks. The parts then were virtually assembled which allowed me to check fit and function; I was even able to check the optimal placement of the parabolic mirror in the bottom of the globe to illuminate the 3D picture via diffused sunlight through the globe. The images I rendered helped illustrate Keiren's vision and bring life to her grant application.
gLike