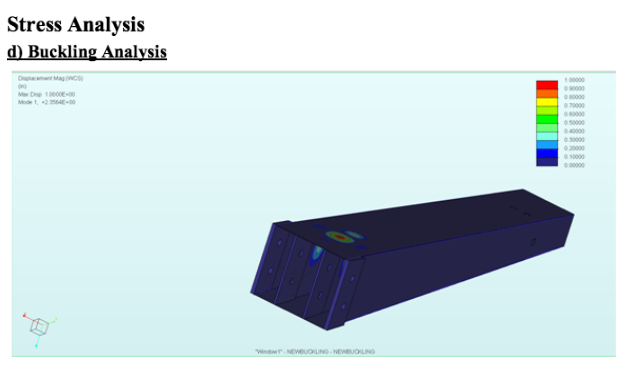
THE PROBLEM
In my mechanical design course junior year, my team and I were assigned to design a boxlift crane that could lift 500 pounds.
Other constraints included a maximum weight of 5 pounds, simplicity and aesthetic appeal.
PRELIMINARY CAD MODELING AND PERFORMANCE SIMULATIONS
We modeled the crane using Creo Parametric 2.0 CAD software and simulated bending and torsional stress tests on this CAD model in order to identify points of highest stress concentration and estimate our material costs.
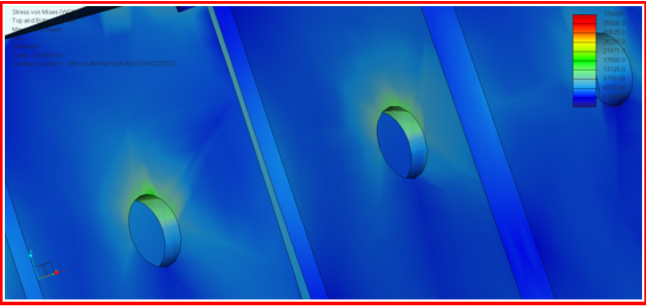
Static stress analysis close-up of pin-holes. We concluded that the pin-holes were acting as stress concentrators. We responded by reinforcing the area around these holes with an extra layer of aluminum.
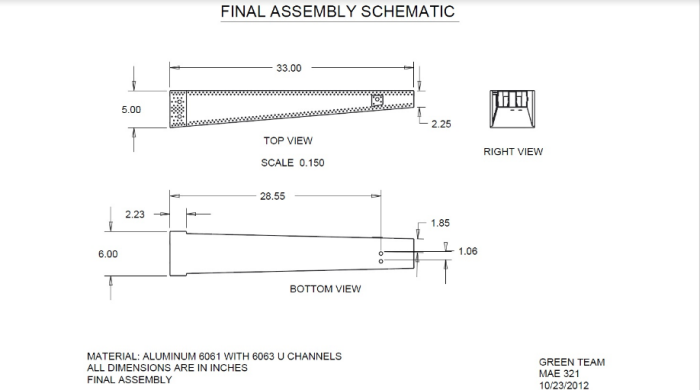
FINAL PRODUCT
We revised our design by adding external plates to reinforce points of stress concentration and by rearranging internal ribs until our CAD model survived simulations of applied stress.
Our final product was composed of aluminum 6061, and reinforced with two internal ribs spanning the length of the crane and two external plates around the pinholes at the crane's base.
We also sanded the surface to make it shiny and visually appealing.
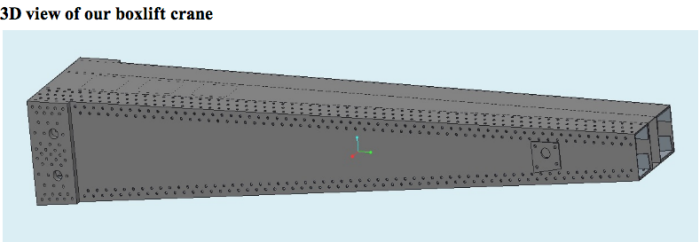
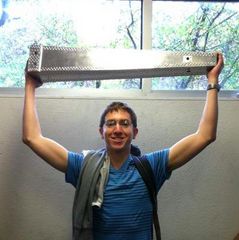
TESTING
Our crane lifted the 500 pounds without fracturing or buckling.
gLike