
Carbon Fiber fairing left to cure
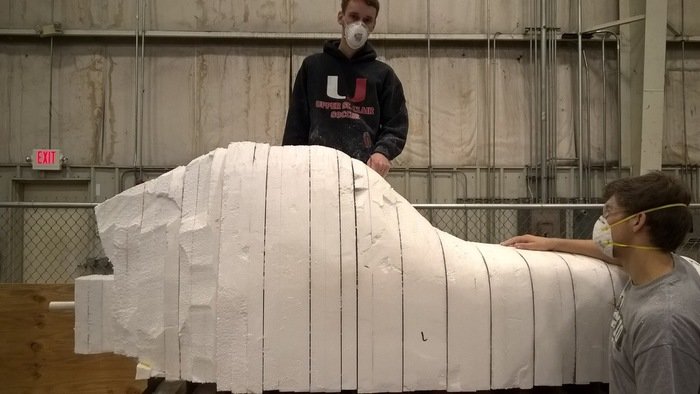
Rough shaping of foam mold
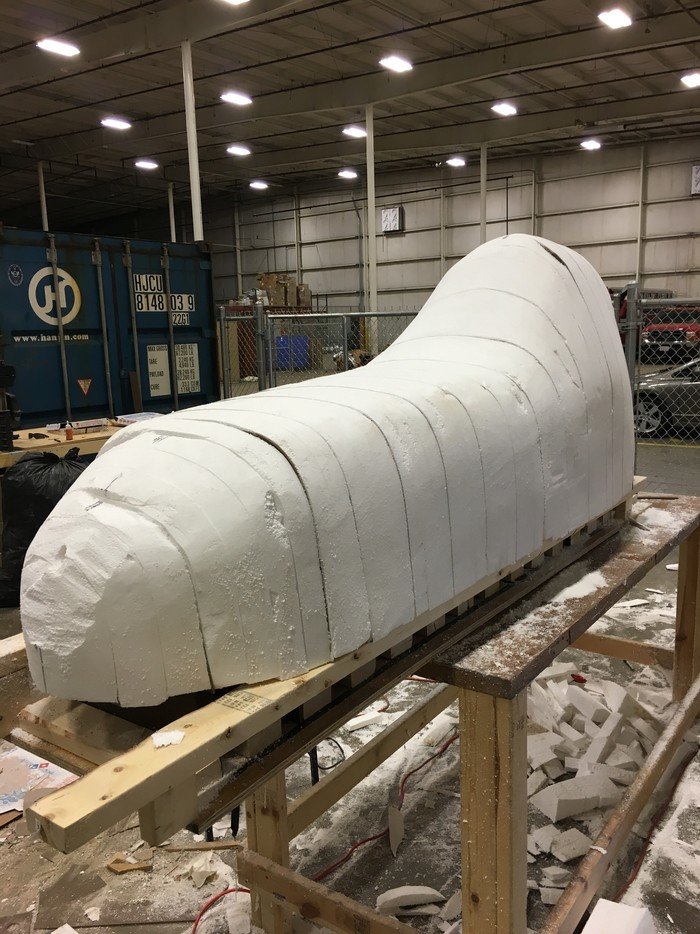
Smoothed out foam mold
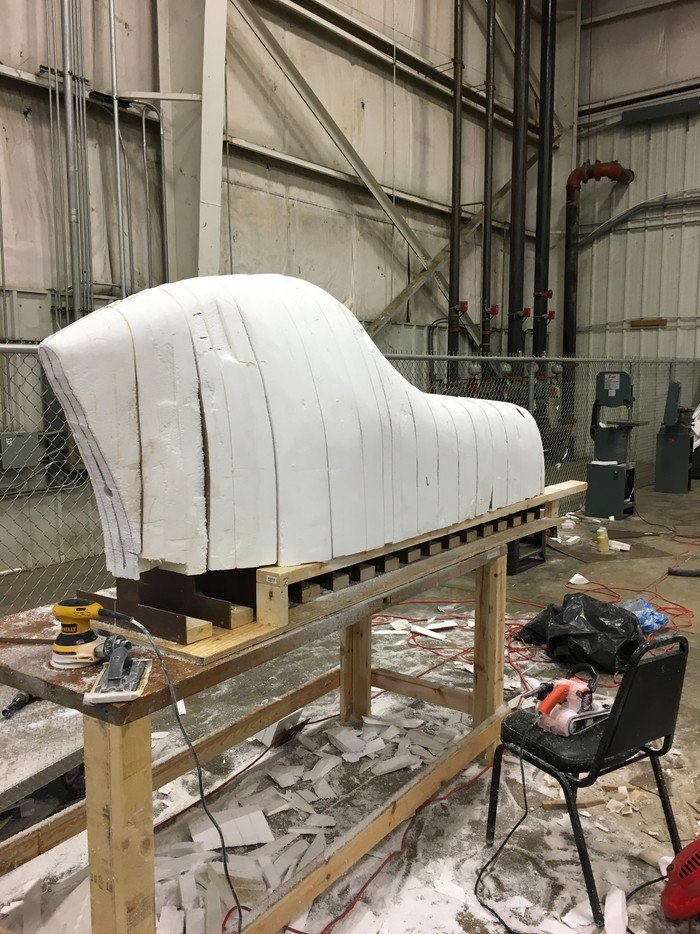
Another shot of the foam core.
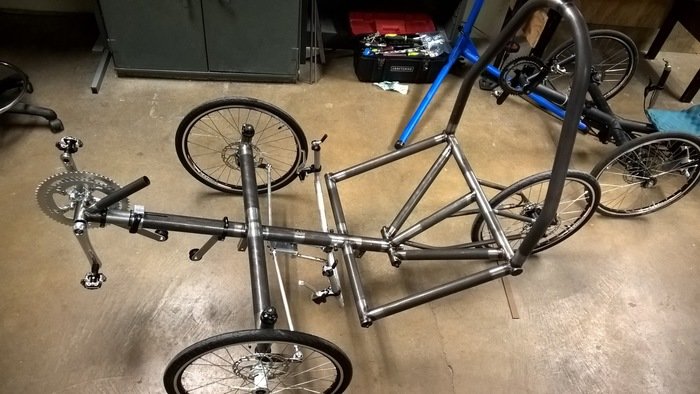
Assembled recumbent bike frame to be used for competition
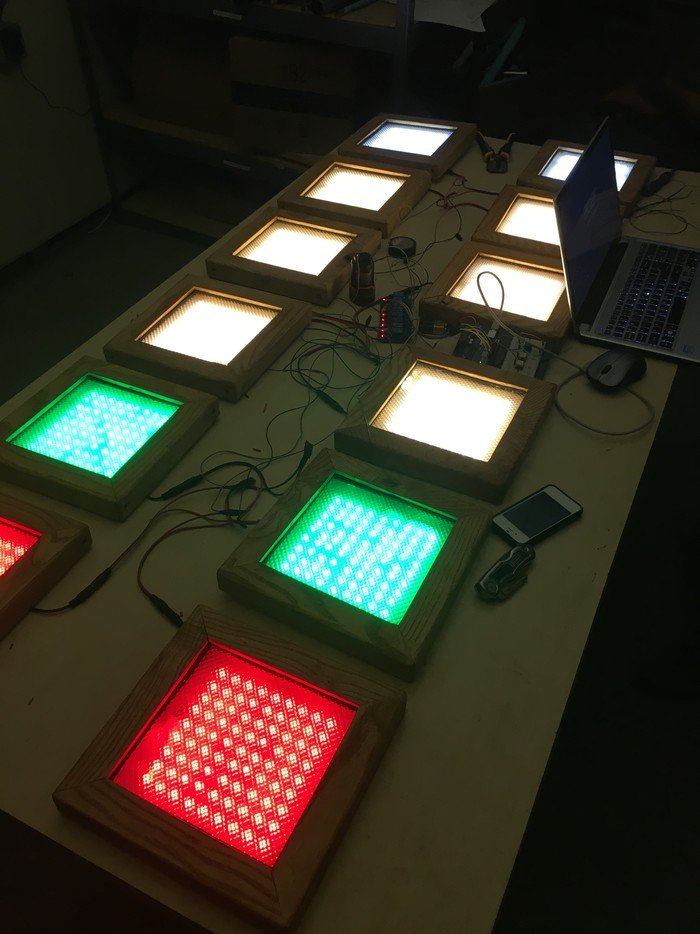
LED light tree to be used for competition. This side-project exposed me to LED's, wiring, and microcontrollers. This picture was taken while the tree was being programmed for the start of a race.
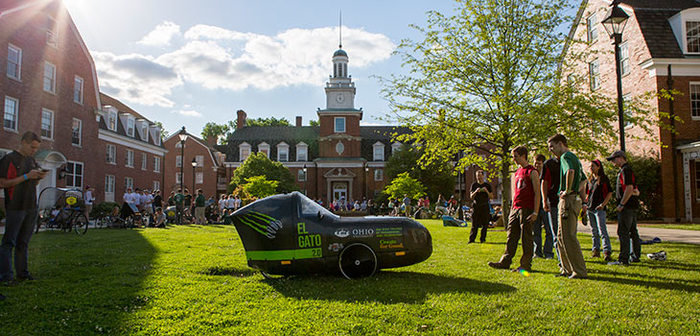
The HPV team's final build pictured at competition. (Photo Credit to Ohio University)
gLike