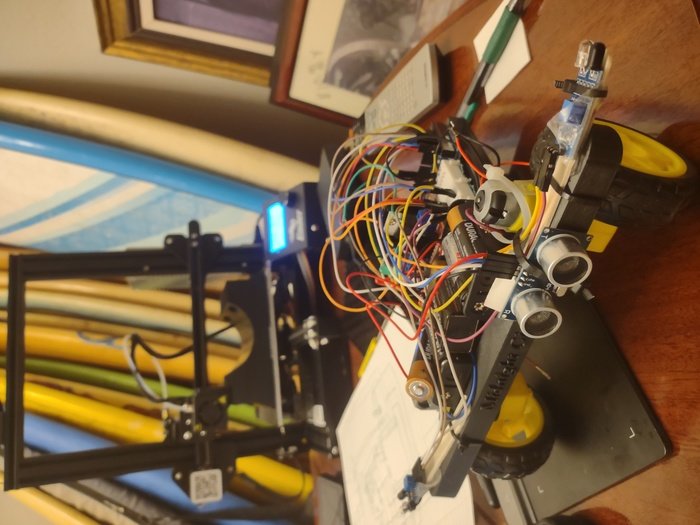
The second iteration of the Mechatronics car uses a 3D printed chasis and motor mounts. The ultra sound and infared sensors provided guidence to avoid obstacles as the car moved from point A to point B.
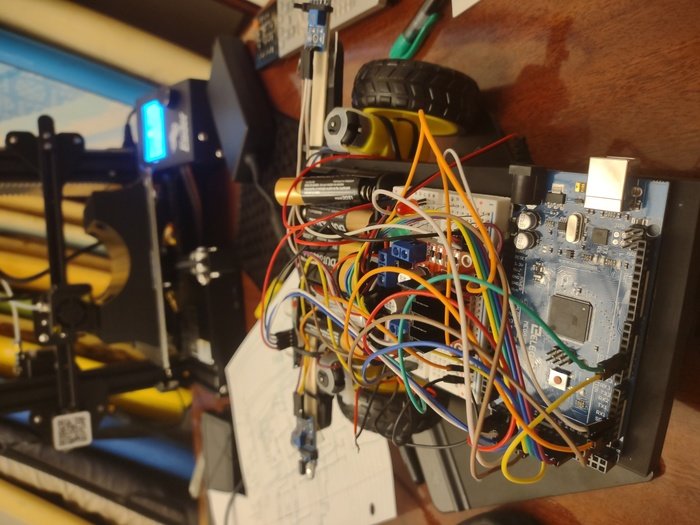
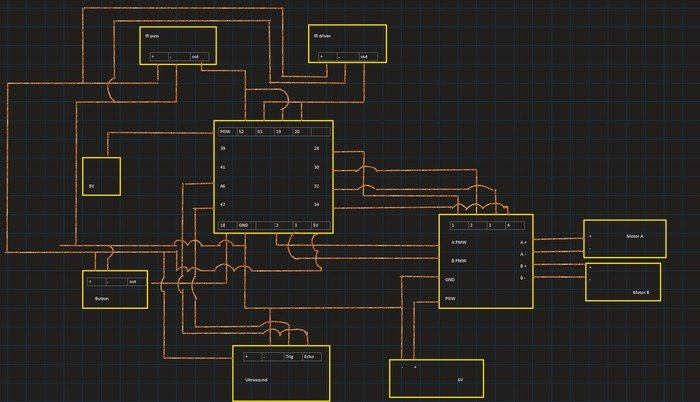
A circuit diagram of the wiring for the autonomous car.
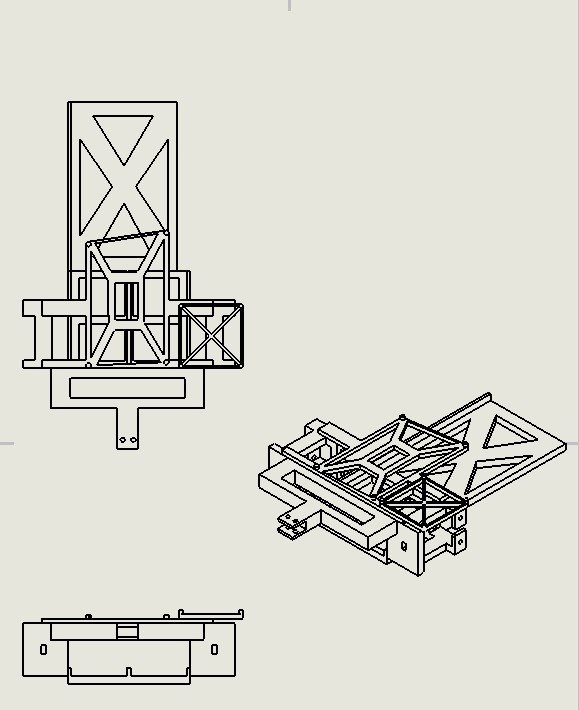
The final design of the car was built to be lightweight as the car had to get from point A to point B faster than other cars. Using a modular 3D printed chasis allowed for the car to be lightweight and easily assembled.
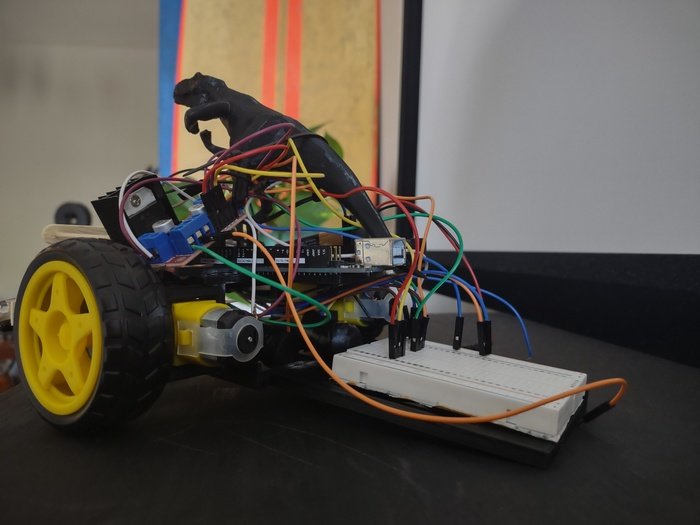
A back view of the final car. The battery storage under the Ardunio and motor controller allowed for a low center of gravity with less weight on the rear of the car decreasing drag.
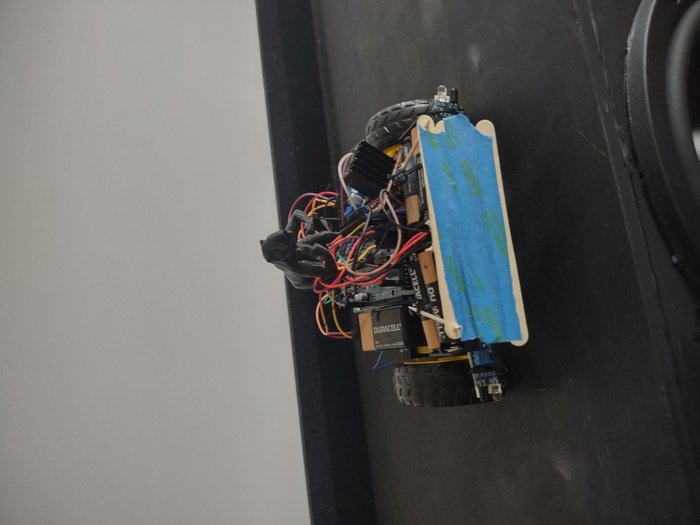
A front view shows the car with a popsickle stick bumper to mitigate damage in the event of a crash. The bumper, also when, clicked stops the car and has it turn 30 degrees and continue foward. The dinosaur on top was added for demostration to the professor as he is a fan of dinosaurs.
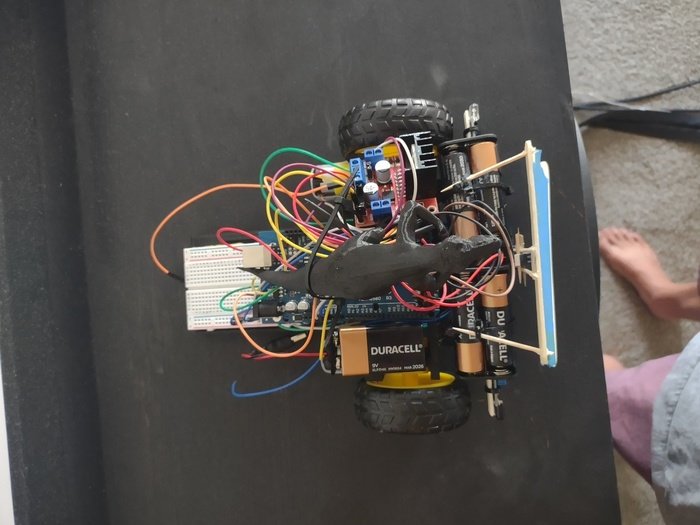
gLike