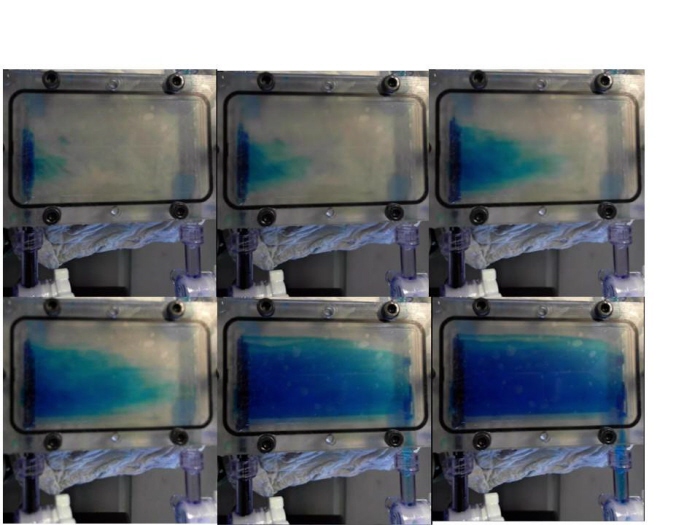
Figure 5: Dye tracking experiment.
A dye tracking experiment was carried out to corroborate the CFD results. Mixing in the settling chamber made following the dye front difficult but was sufficient to calculate approximate shear stresses.
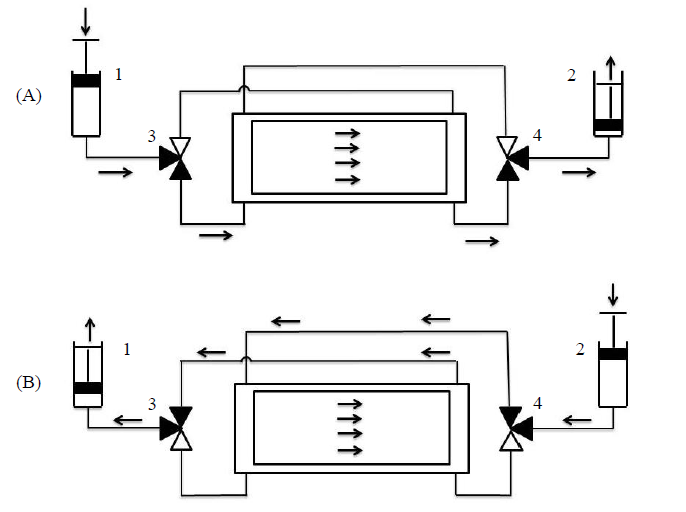
Figure 6: Novel double syringe pump configuration
A novel design for a PPFC capable of applying fluid induced shear stress and quantifiable pressure was proposed. Two actuators and two three-way valves are used to provide a lot of flexibility for when applying mechanical stimuli. This allows fluid induced shear stress and pressure to be applied simultaneously, independently and individually.
gLike