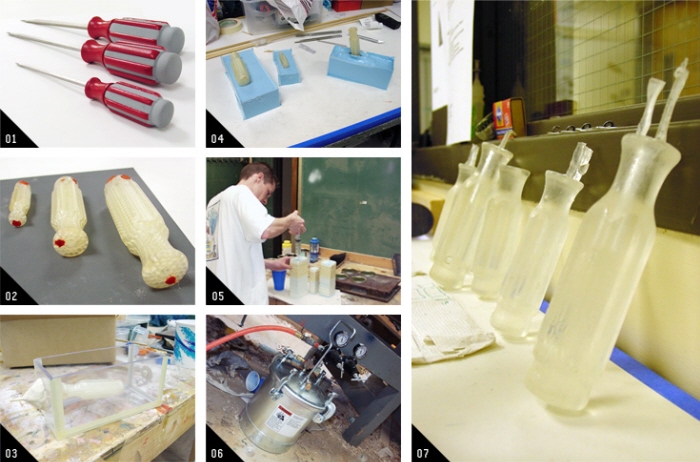
Prototyping of Final Prototype - Image 1: This is an image of the ren shape models I made.
Image 2: The 3D data from these files were used to build SLA prototypes at a local auto performance shop in Auburn.
Image 3: I then built boxes that would allow me to suspend the plug.
Image 5: This is me! Again! I am injecting a two part epoxy into the molds, basically simulating the injection molding process on a small scale.
Image 6: This is a pressure cooker.
Image 7: Final models ready for prepping.
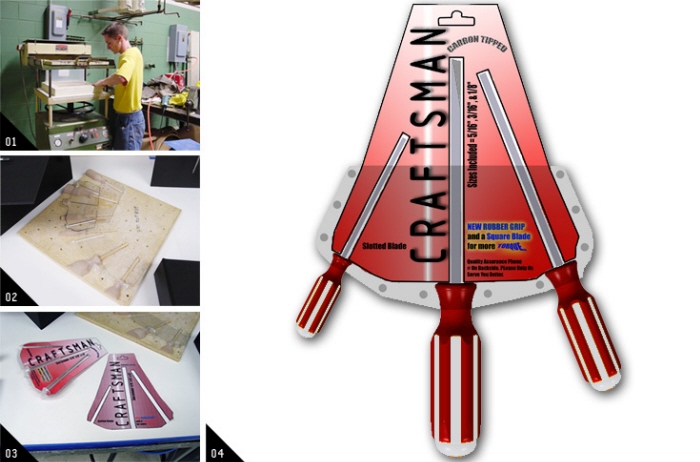
Packaging solution and fabrication - Image 1: It's me again; blah. I am prepping the vacuum former by sealing the edges with tape.
Image 2: This is the plug I made from sectioning handles made from ren shape and gluing them to a piece of MDF.
Image 4: This is a CAD rendering of the final packaging and graphic card inserted into it.
The packaging is designed to allow the user to grab the handles of the drivers, thus allowing them to feel the soft over molding and user focused design features.
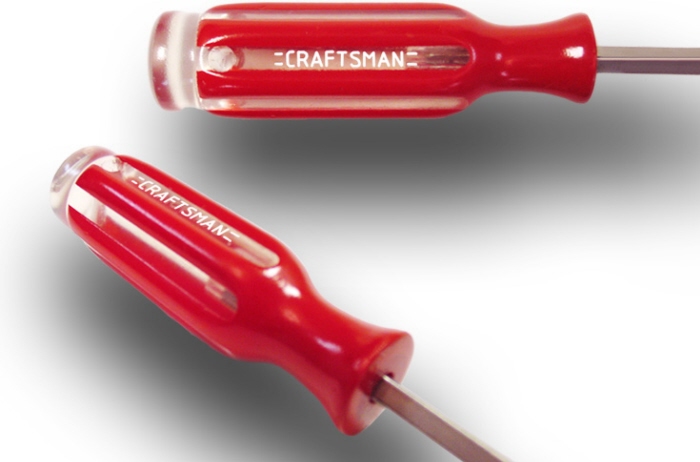
Final Solution - The handle has a soft rubber over molding, shown in red, which reduces slipping and is a key attribute consumers look for on driver handles.
A hole at the back of the handle enables the user to insert another blade into it in order to increase the amount of torque they can apply to a screw.
The butt of the handle has been flattened to reduce the pressure normally felt in the palm of the hand as one tries to apply pressure when attempting to remove a frozen screw.
gLike